Club Meeting: 10 June 2020
Report by: Rio Davies
Terry had pre-poured the pewter into grooves in timber to make rods; easier to work with.
Pewter turns like butter but will scratch easily.
2nd hand pewter from op shops melted down can be ok, but old stuff will contain lead, whereas it is no longer added to new pewter.
Making the base- Use a forstner bit in plywood to make a round mold.
Pewter has a low melting point, a solder iron is no-good however.
Rim – groove with rebate; measure your outside perimeter on blank.
For molten pewter, jimmy a metal spoon onto a long stick, stir to remove slag. If left in will make the pewter brittle from air voids. It will stop skimming off slag when it’s ready.
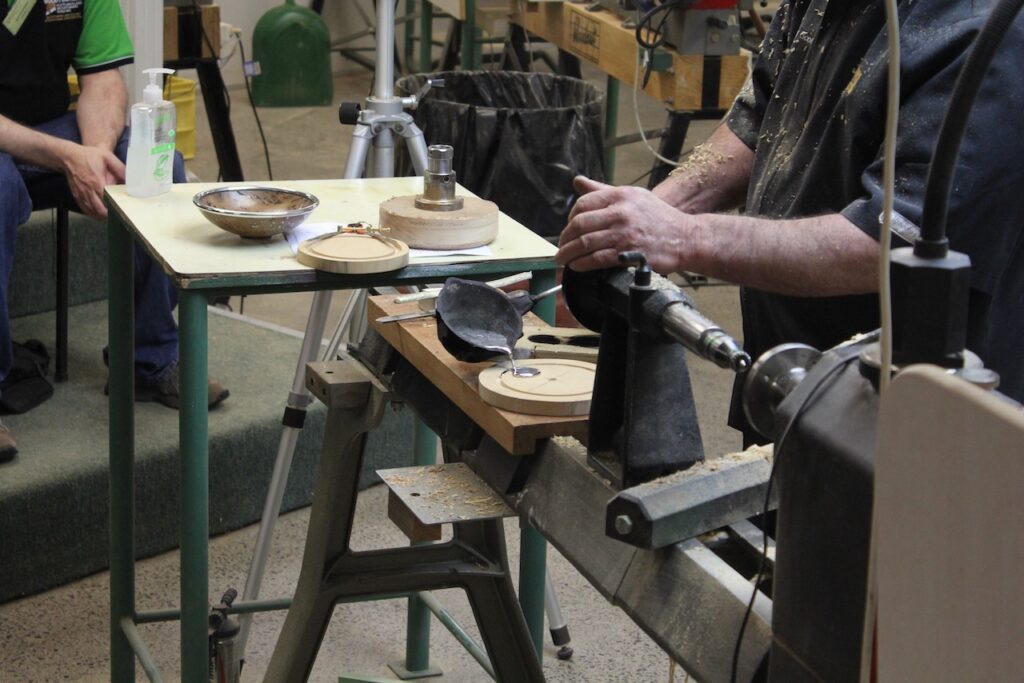
Pour into base mold and rim, Keep continuous even pouring till it crests.
Running it under cold water will weaken it so allow it to cool naturally.
When melting do not let it boil. It will burn the timber and will react with resin in the wood when poured directly into your bowl. Sparks and flames ensue.
Diluted pewter containing lead will also make flames.
To release from mold, sometimes sawing of the wood will be needed.
Terry demonstrates turning a bowl, cutting spigot (54mm), proceeds to make the mess he promised not to (10/10).
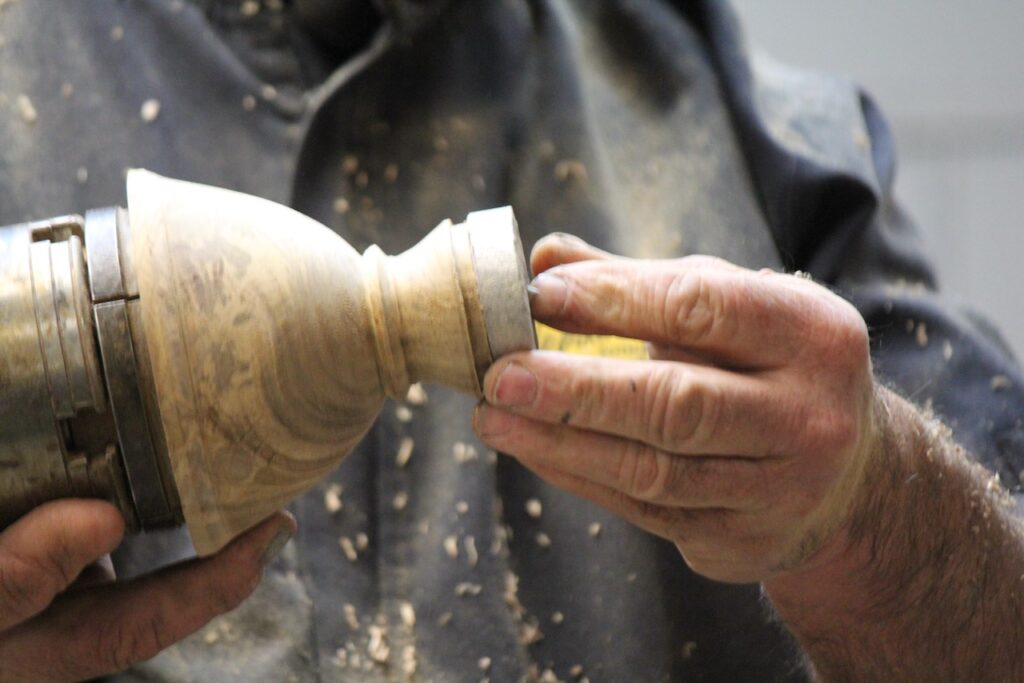
For base, cut rebate for pewter to key onto, 3mm, not too deep so you don’t lose the bottom from the inside.
Remove from chuck.
‘New turners can’t imagine a concave curve’, isn’t that always the way.
Plywood backer behind the pewter base disc in the chuck.
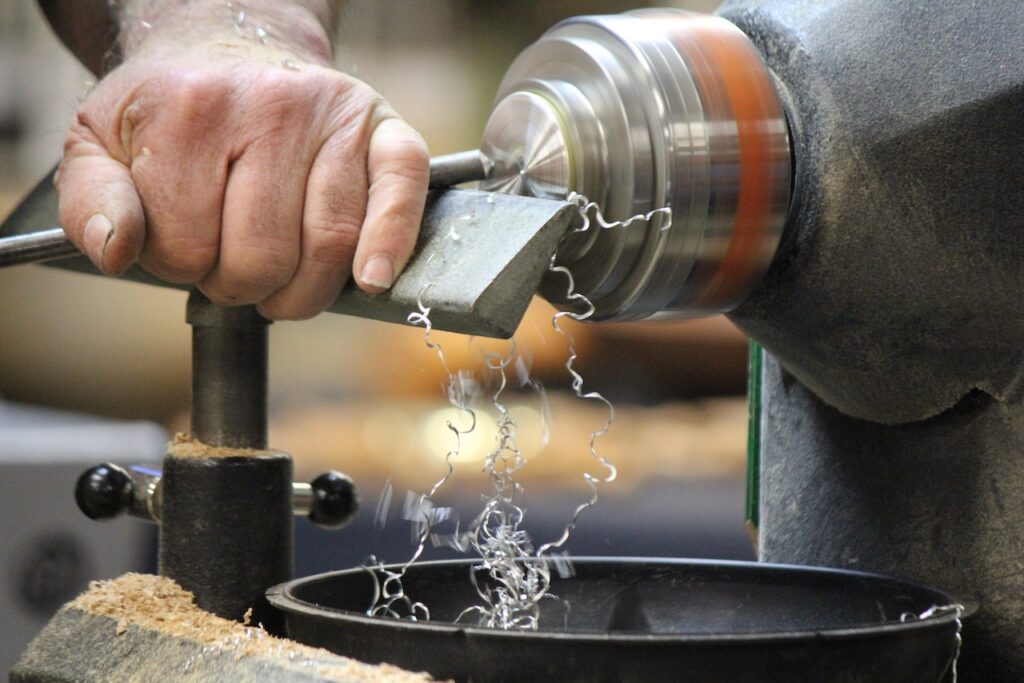
Levels pewter, knocks over his shavings bowl.
Cut corresponding rebate in pewter.
Turning the tenon, flat or slightly concave is ok.
Turning the rim, add spigot. Chattering that can be heard is the pewter moving in the mold, can use superglue to hold it.
Check rebate depth is the same on both sides.
Back to bowl. To avoid going back-and-forth buy a second lathe (but only from Terry of course).
Match rim to bowl with calipers.
To glue use 24hr araldite , quicker setting (5 min) is ok to get turning sooner but not as strong.
Use tape on the chuck to avoid gluing the jaws shut (Terry has extras of course).
Turn away wood on top to reveal Pewter rim, round and tidy.
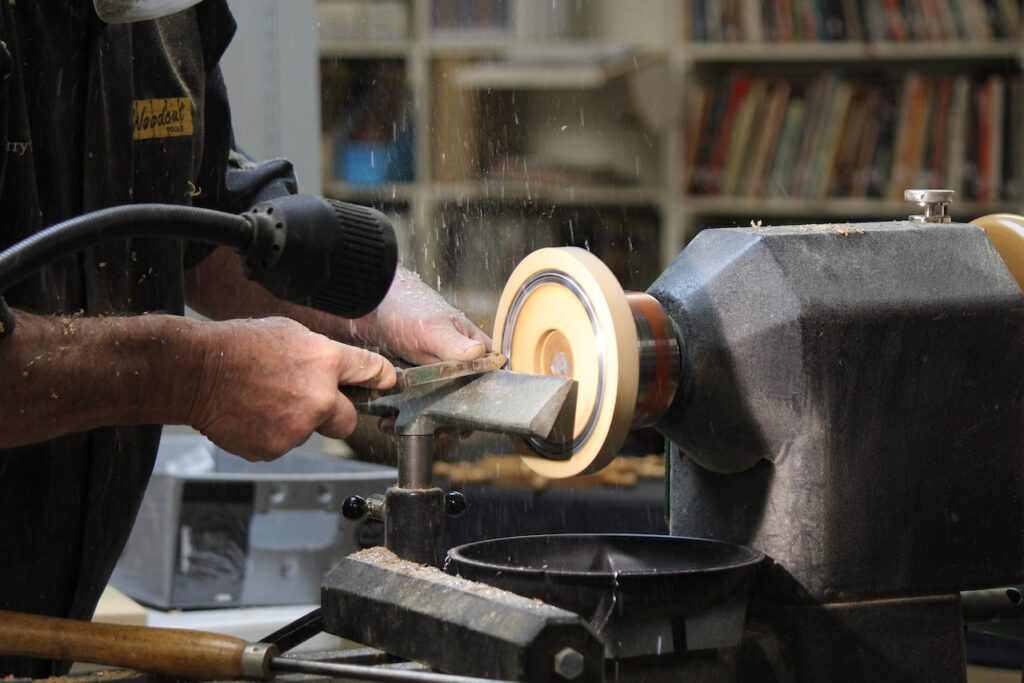
Pewter embellishes nicely, a leather punch will work and can accent with Indian ink in the grooves.
Terry uses a texturing tool.
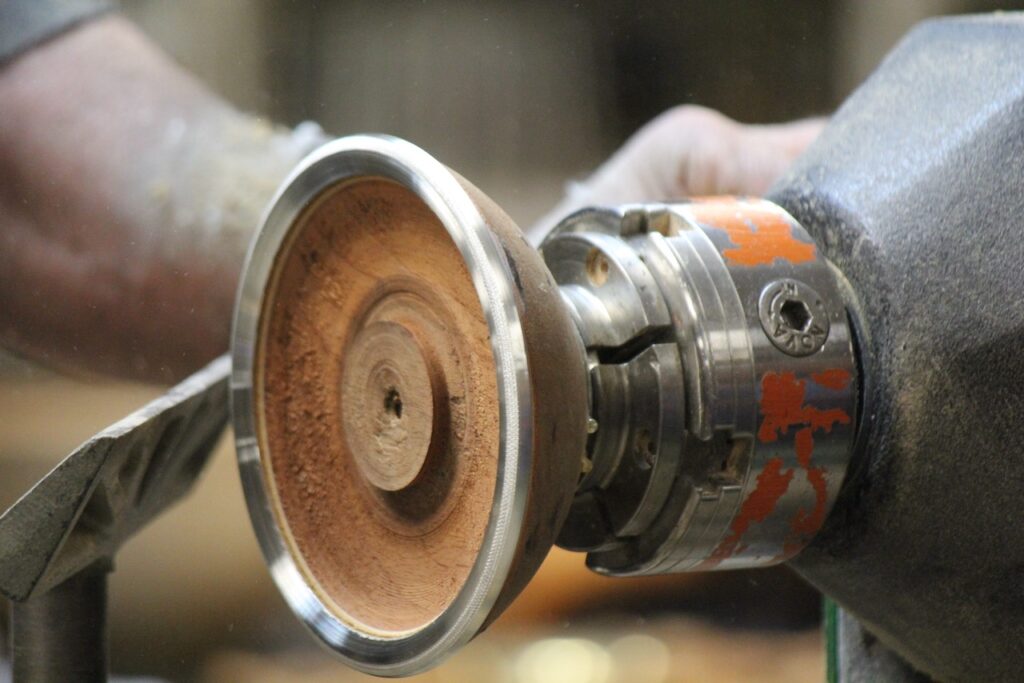
For sanding, 400 through to 2000.
Don’t use Danish oil- black comes off pewter into the wood.
Turning inside of bowl, finish rim first because the heat from the glue can move it.
Sand inside w/ 240 grit, through to 400.
Use jam chuck to reverse bowl, Terry uses next bowl to hold it however, turn RPM down.
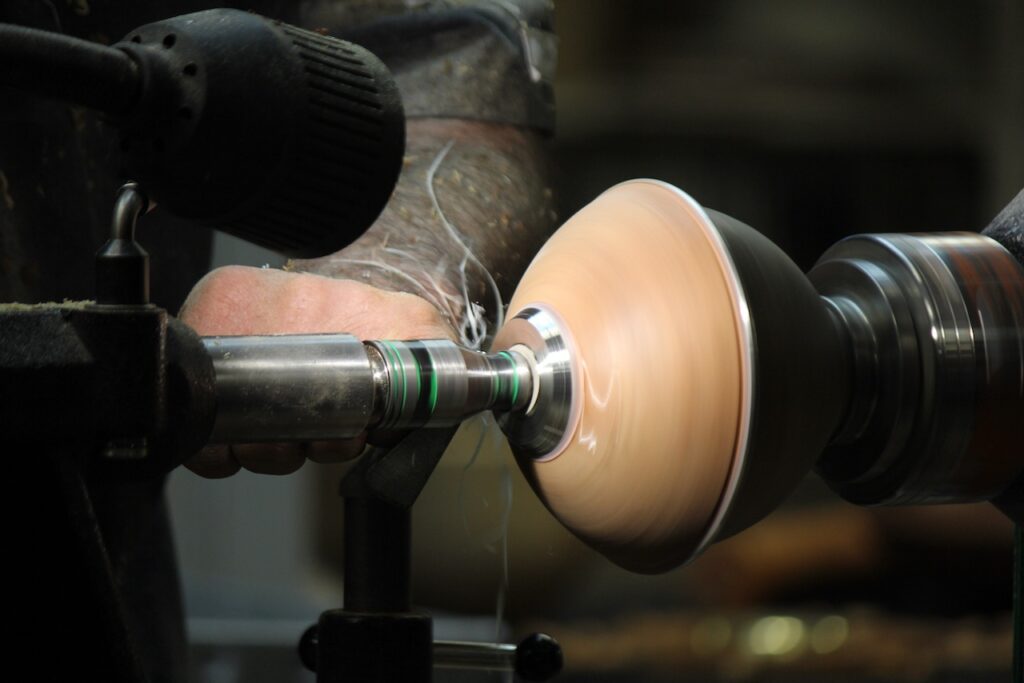
Cleaning the base pewter, pronounce concave of the base to remove weight.
Tidy and sanding exterior of the bowl.
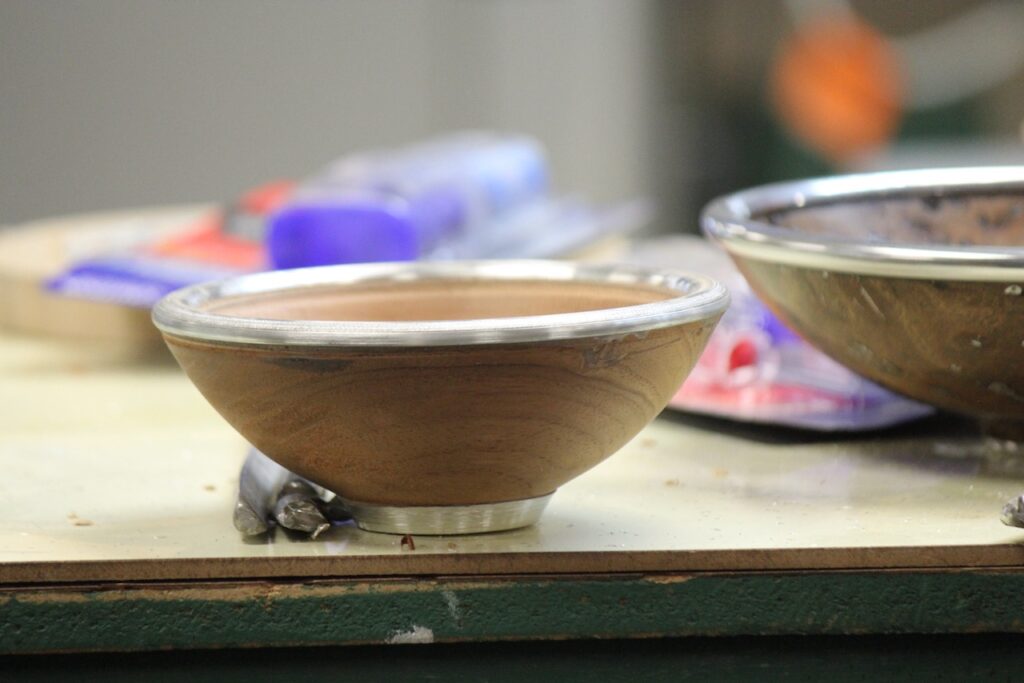
Warned to use mask with mahogany as the dust is sharp and dangerous to inhale.
The base foot pewter can scratch easy but won’t need polishing like silver.
Completed.