Club Meeting: 25th June 27, 2025
Report by: Bob Yandell
Our Club is fortunate in having people willing to share their knowledge and an environment that encourages members o ask if they don’t know – There are no dumb questions.
Kieran Fitzgerald was Chairperson and Timekeeper and having received questions, in advance, had passed them to the 2 principal experts Terry Scott and Ian Connelly for them to be prepared. It looked like Terry had brought his workshop minus lathe and bandsaw.
The following are synopsis of the questions posed and of the advice given by the experts and relevant comment from those attending. Many of he answers can also be found on our website under Tips and Jigs.
Chuck size – use appropriate jaws especially for bowls and platters greater than 300mm diameter use of 100 or 75mm jaws achieve a safer result. The opening of the jaws widely to accommodate a larger spigot is not appropriate as it results in 8-point contact, this can result in the spigot being torn off, whereas near total contact is achieved when correctly used. After the item is finished the spigot can be removed or modified, such as transformed into feet.
Chuck – Mounting Safely
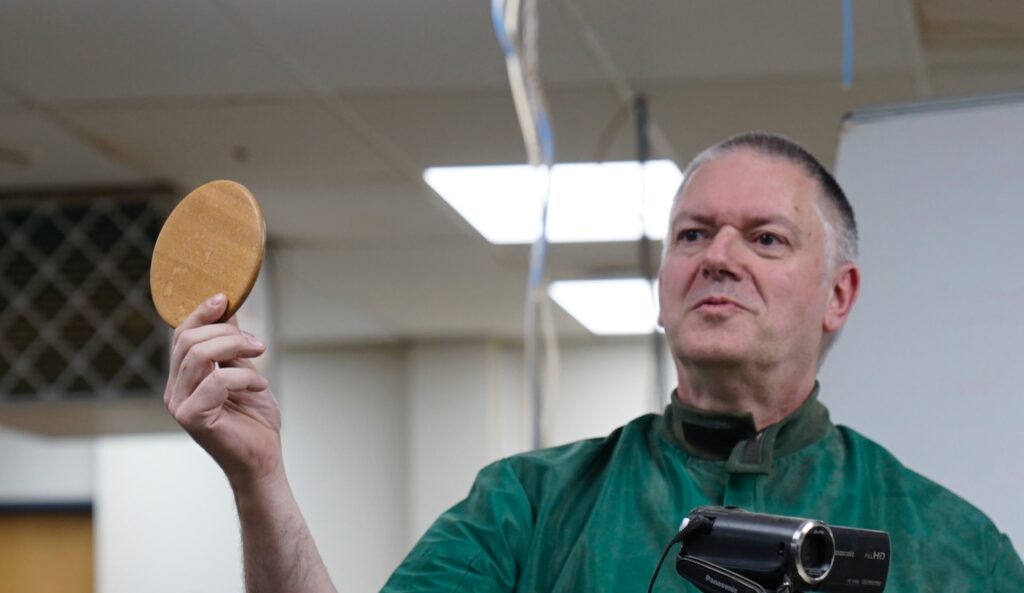
Finishes – Key to choice is “What is the purpose is the item”. There is no one Finish for all items. Avoid waxes when the item is for food or will be handled many times e.g. lid in a much-used box. Hard oils such as Danish should be applies in warmer temperatures thus ensuring they dry. Humidity and temperature affect drying time. First coat to be light/thin as it is the one that acts as a key to subsequent coats and best left 24 hours. If applying a spray, the first should be a mist coat as it is again going to be the key to following coats.
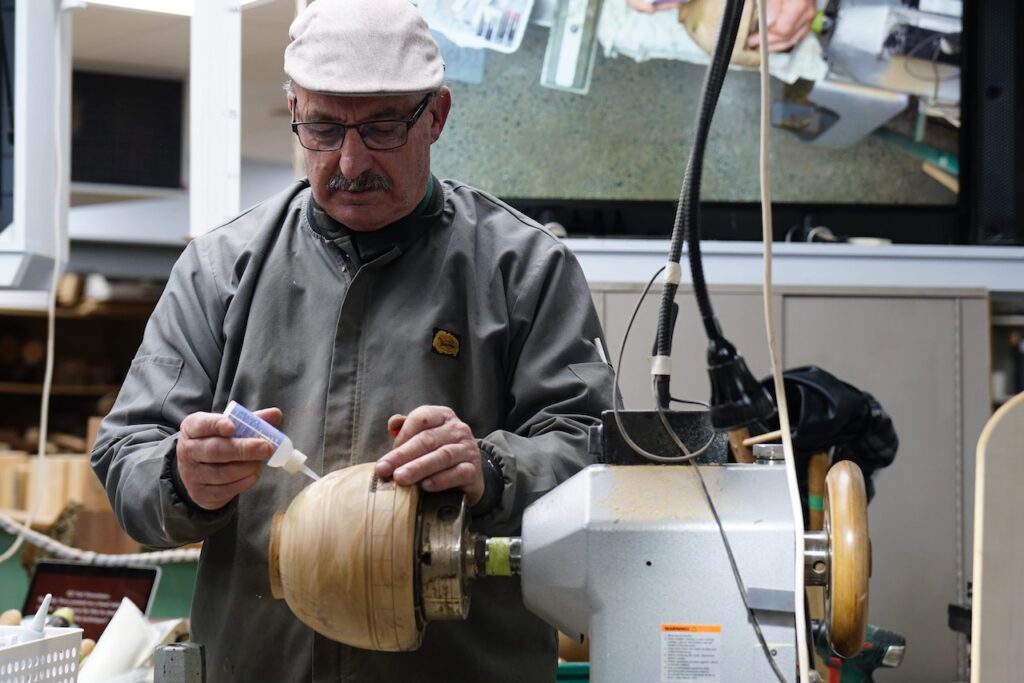
Inlays – To fill a void and enhance the look of an item you can use powders such as copper and turquoise. The void should be clean and to reduce the amount of powder used spray the surface with Accelerator the fill with sanding dust to a level below the finished surface. On a curve you may need to build a dam using hotmelt glue. Put in the powder higher in the centre of the void and tap it down, like the dentist doing a filling, apply CA glue (Thin) but no accelerator. Continue until proud of the surface. Tip – Store your powder in a bottle, like that used for CA glue as this will assist in minimising the amount of powder applied. Sand the filled void area with care as the inlay is harder than the wood.
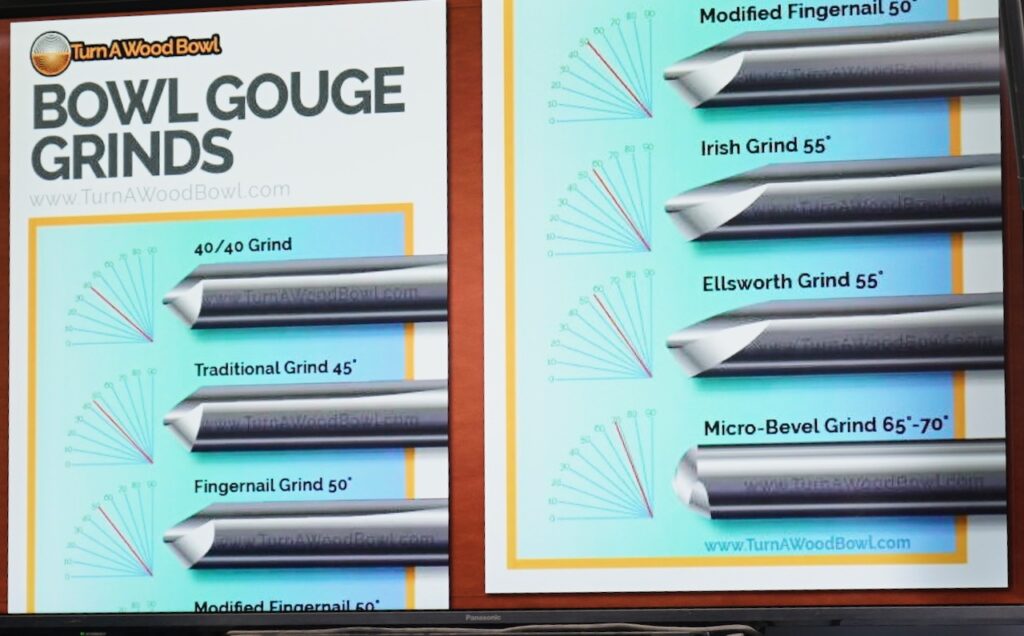
Fingernail And Other Grinds – The choice of grind angle is a personal decision and changing the angle to follow a particular turner won’t solve a problem. The basic principle of rubbing the bevel, angle of the flute and speed, both across the wood and of the lathe must be first and foremost in the process.
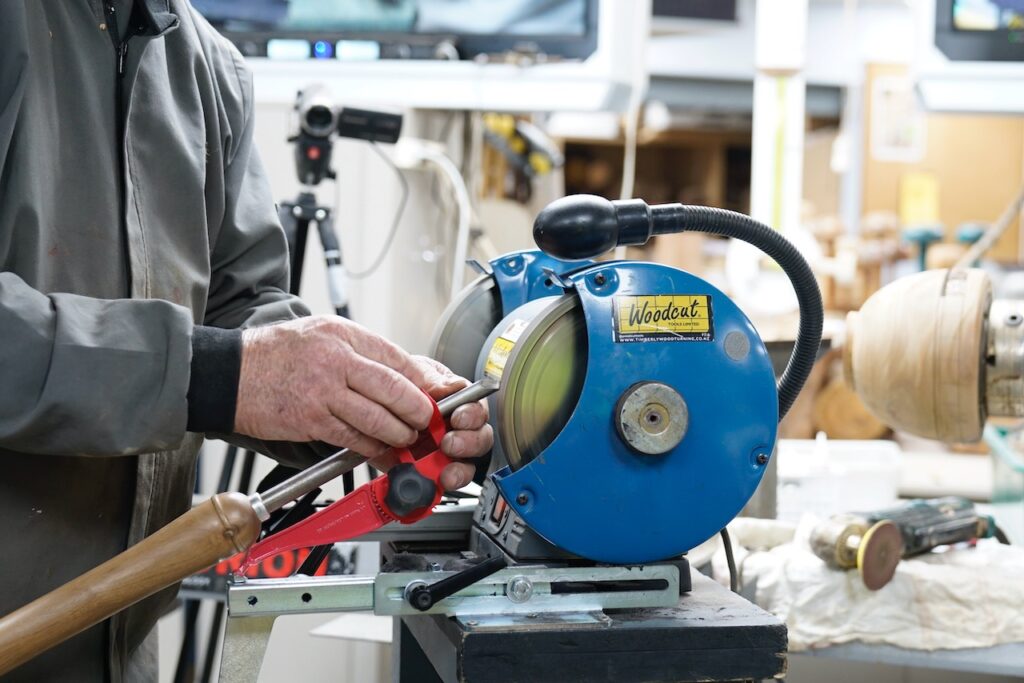
Terry’s Fingernail grind starts with the standard 55 grind then by moving the leg of the Woodcut Tru-Grind holder from the parallel to notch 4 and grind the back from the tip.
Go to the links on our website
Sharpening – Other Grinds
Sharpening Process
Sharpening Settings
Sharpening Spacers
Sharpening Station
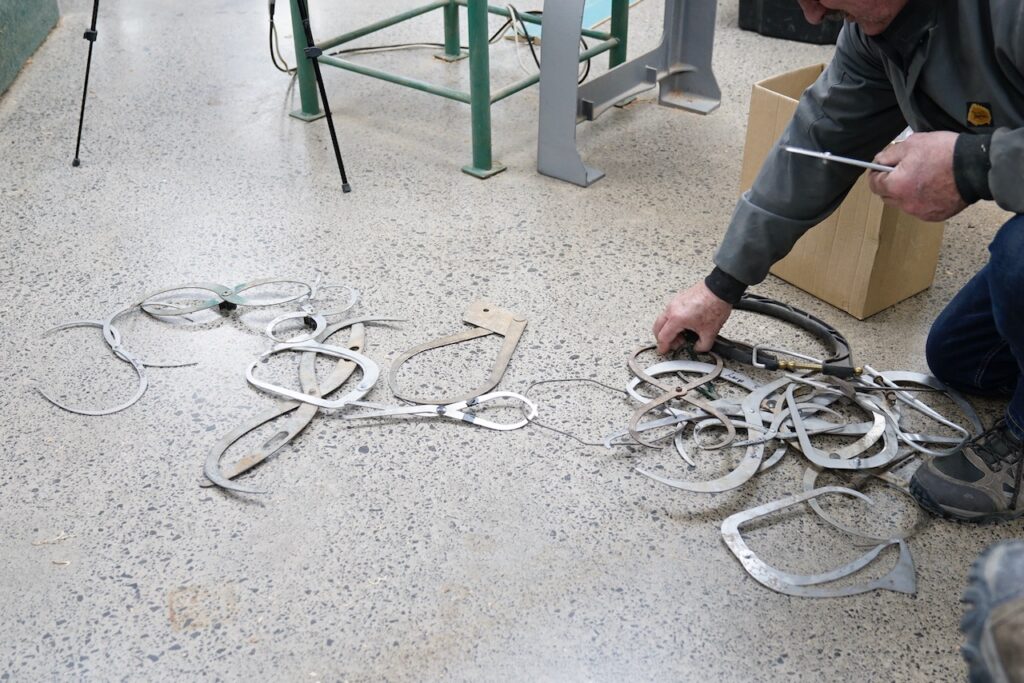
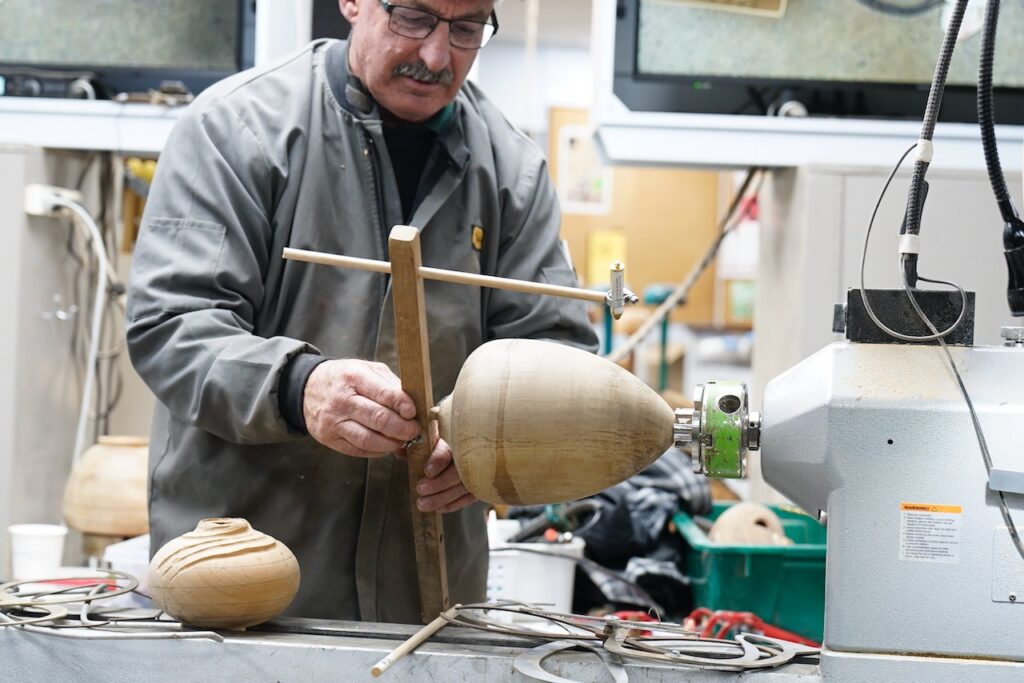
Gauge the thickness at the base of a Hollow form – Terry showed various ways to measure the wall thickness and base. They were the manufactured, the self-made (using wire coat hanger, wood and dowels, laser light). Too many and too difficult to write about, see Terry!
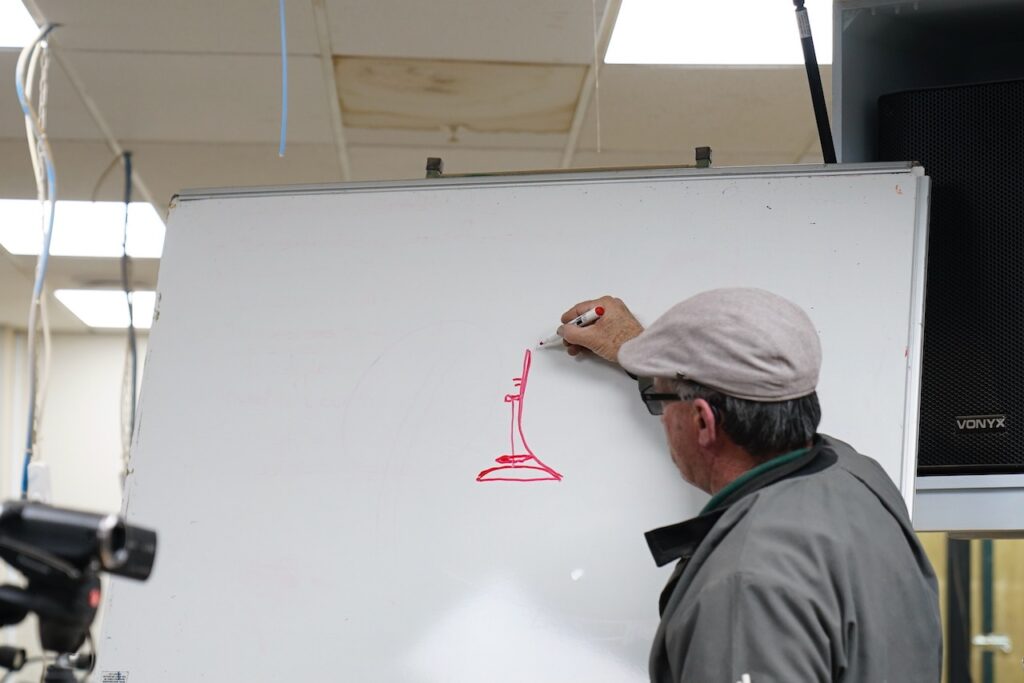
What makes a good Knob or Finial – The basic rule of thirds or Golden Ratio or Fibonacci sequence (0, 1, 1, 2, 3, 5, 8, 13…), where the ratio of consecutive numbers approaches the Golden Ratio. The design of the Finial or Knob must not be considered alone but as part of the total image. It is part rather than an add on, it is complimentary. Reference Cindy Drozda (www.cindydrozda.com).
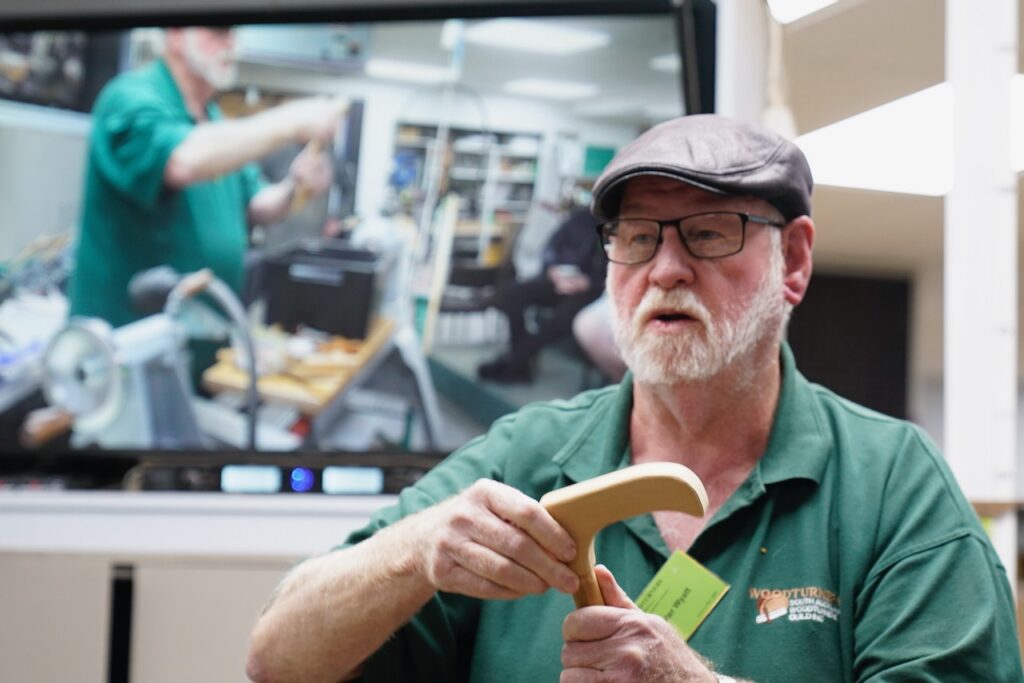
Making a Walking stick – This was explained by Peter Wyatt. Peter has 3 basic sources for the shaft – Old and damaged sticks from Op Shops; square wood 40 x 40 x ?? and Teatree (Manuka) of a diameter suitable. People love the twists and curves. Handles are also from various sources – door handles/knobs; deer antler; golf putters etc. A 7mm hole is drilled in one end of the staff/shaft to a depth of 38mm and a 7mm hole is drilled into the handle to a depth approaching 38mm, subject to material. A 6mm galvanized rod is cut to 75mm and inserted in the staff and glued in place with 2-part epoxy and the handle is also secured with epoxy. Variance in diameter 6mm rod and 7mm hole accommodates alignment. If a Ferrel is required it cut from tubing (Copper, Brass or Stainless Steel. Turning the staff/Shaft requires 2 steadies and the end thirds are turned first.
Paper Joints – This is the method whereby pieces of wood can be joined using PVA before turning and then separated, by a chisel at end grain, before rejoined so the turned profile is now the internal part of the project. The paper of preference is newspaper because of its construction.
A successful event and a future such event may see the remaining questions answered.