Club Meeting 24 June 2020
Report by : Janet McDonald
The 24th June 2020 Bruce Wood gave a great Demonstration of an Offset Box. Bruce followed the project sheet in our website of a project Guilio Marcolongo is well known for. So in this report I will not reinvent the wheel by giving you the box instructions, but leave a link to the website project instructions. https://sawg.org.nz/sawg/wp-content/uploads/2020/03/Guilios-Burl-Top-Box.pdf
But in among the demo Bruce reminded us of lots of general woodturning things to help achieve a great look.
- If you are using callipers for measuring wood; round off the ends of the metal pincers slightly so the tips don’t grab the wood.
- You can find a chart for suggested speeds for using a forstner bit on the lathe in our website: https://sawg.org.nz/sawg/wp-content/uploads/2019/04/Drill-Speed.pdf
- Bruce showed us how he used his “Digital Tailstock/Drill Press Measurer”. You can follow the instructions here to make your own: https://sawg.org.nz/sawg/wp-content/uploads/2020/06/Tailstock-Measurer.pdfhttps://sawg.org.nz/sawg/wp-content/uploads/2020/06/Tailstock-Measurer.pdf
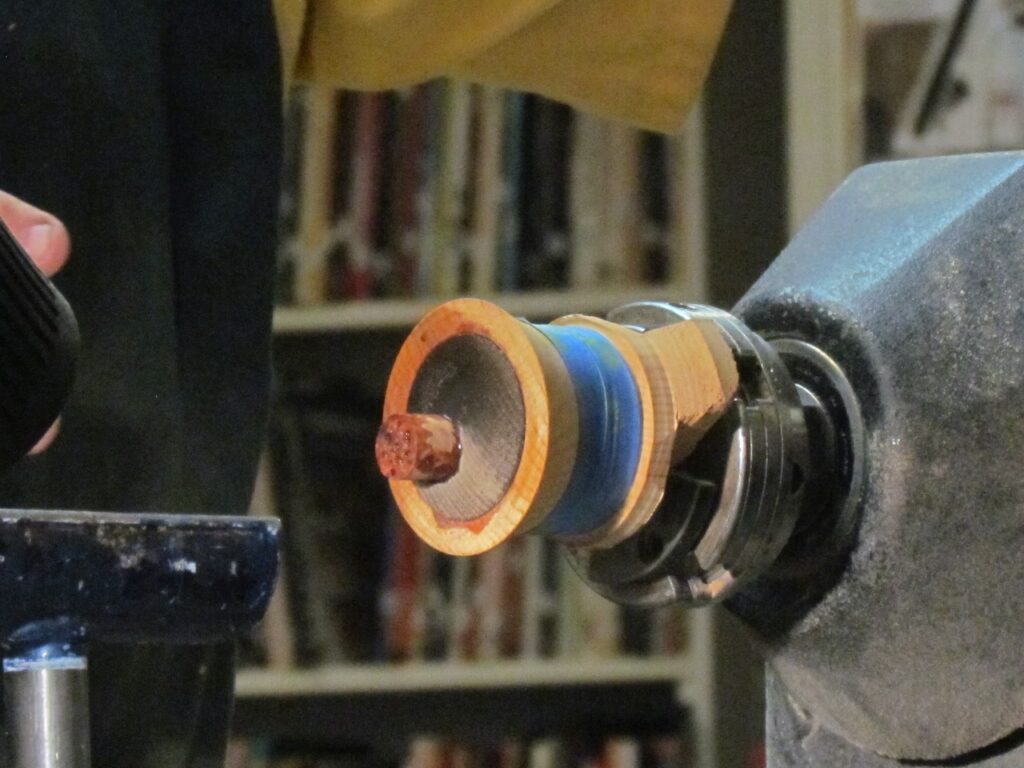
- Being the professional turner Bruce is, he showed us it must be ok to accidently drop 11 things on the floor during a demo.
- Bruce used a micro light that is attached to the tool rest which allowed him to see inside the box while turning and see exactly what he was doing. You can see the light here: https://www.woodgrainnz.com/apps/webstore/products/show/8148180?fbclid=IwAR0tBNT3iAbBAyB3gf11GQ8x5jE6_uaSmOttlzskJPE2aiPdnDV95coTnS4
- Use a fine wire brush on your sandpaper to unclog it and get more life from it.
Bruce used Ondina Oil to wipe over his turned wood just before sanding. This stopped a cloud of dust cloaking the front row of spectators. Read more about this oil here: http://www.timberlywoodturning.co.nz/products.php?product=Woodturners-Sanding-Oil-%7B47%7D-Shell-Ondina-Oil-15-%252d-1-litre-
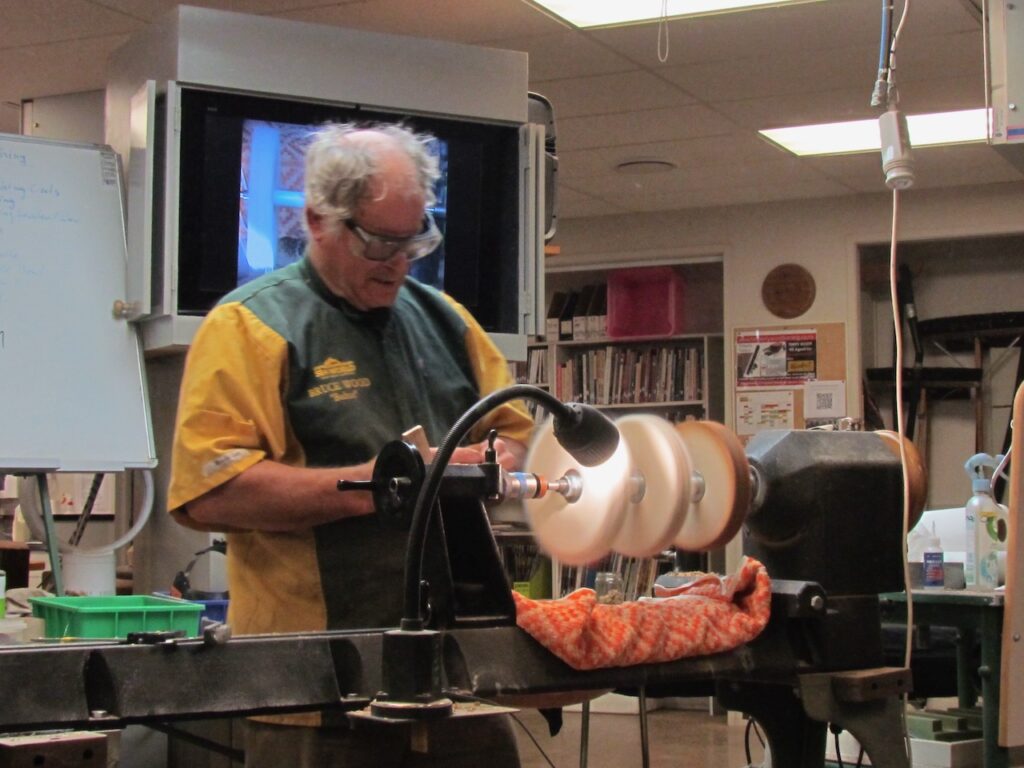
When using buffing wheels on your lathe it is easy for your turned object to fly out of your hands. So Bruce laid a folded towel over the lathe bed, so if the object flew it would not get dented on the lathe bed.
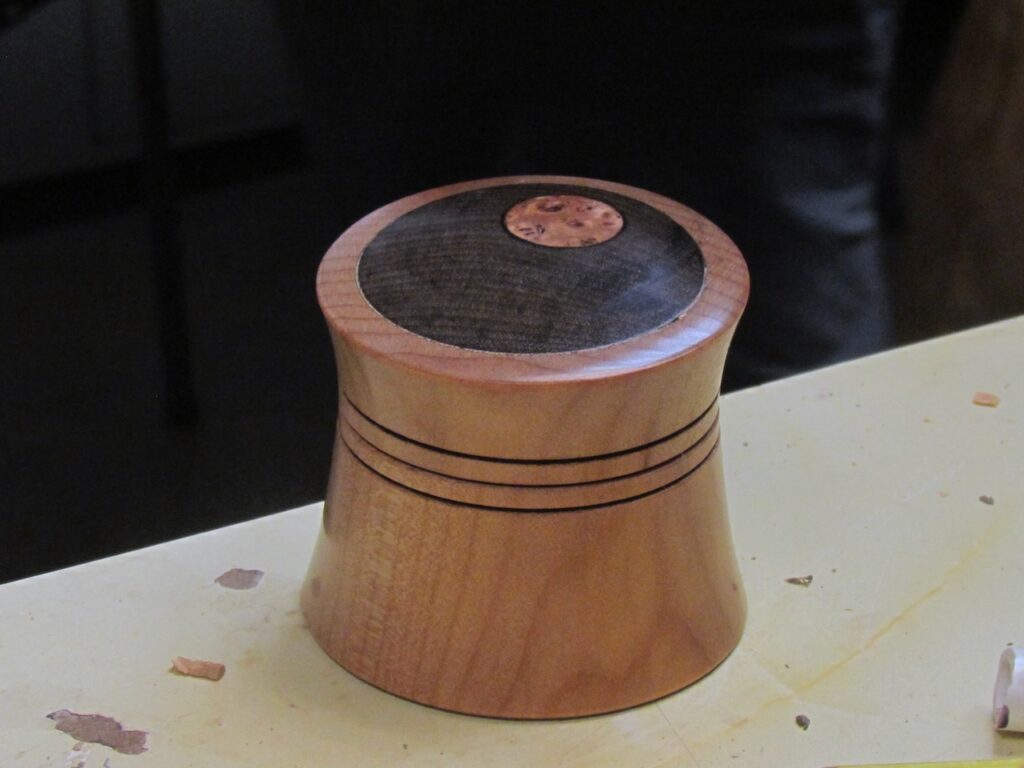