Club Meeting: 28 September 2022
Report by: Kieran FitzGerald
Wow! It is the last meeting for term three. Where did that go??? It is fitting that the term finished with another demo themed around the term topic of “Natural”. Bruce engaged the clubbies with a challenging (for some) discussion around design opportunities for wood which still contains original features enabling it to be designated as natural, and which preserve the characteristics which mark each piece as unique.
As an introduction, Bruce told us about a time long ago when he and Ross were members of a Maraetai club when Terry Scott visited and did a demo. This was Bruce’s inspiration to begin woodturning, and he produced a live edge bowl he turned in those early years. Of course club nights wouldn’t be the same if there wasn’t a degree of toing and froing between the demonstrator and the audience, and in this instance the topic was “recess or tenon?”. Terry encouraged tenons based on both practical and safety reasons, but of course Bruce’s early turnings featured a recess to hold the piece.

From his box of tricks Bruce took out a beautiful, large, dark coloured bowl which exhibited all the holey features of a burl. Next he pulled out a smaller piece turned from the same burl, and which still had a flat where it was sawed off the main piece. Finally, from the same burl, a pretty lidded bowl. This last offering underwent a design transformation while Bruce was turning it, because he saw the opportunities to better highlight the natural beauty of the wood. These three pieces, he said, would stay in his possession until his time was up. After that, it was up to his family to decide what to do. Obviously very treasured pieces.
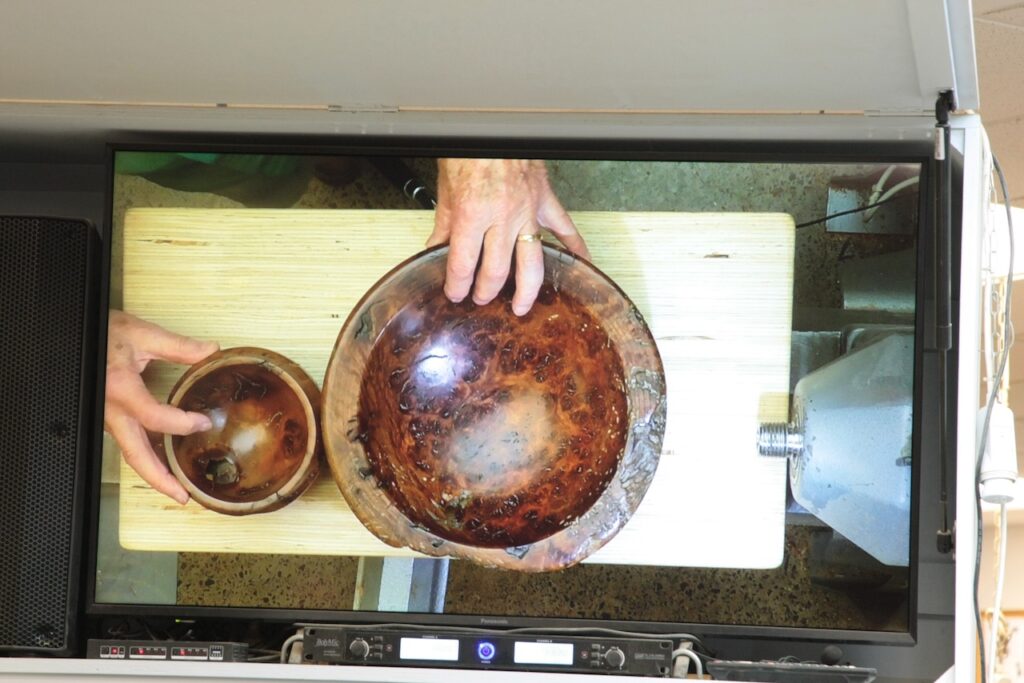
The next block of wood Bruce brought out was a largish block of macrocarpa, chainsawed on all edges. From the front view, it looked like a clean piece suitable for a decent size bowl. But when Bruce first turned it over, it had a large bark inclusion. Once he chiselled out the bark it was a deep river running right through the piece, rendering it totally unsuitable for any conventional types of turning. What to do with it? All saw the inherent opportunities the piece offered, but opinions were varied. I think the majority saw a resin fill as presenting the most suitable use.
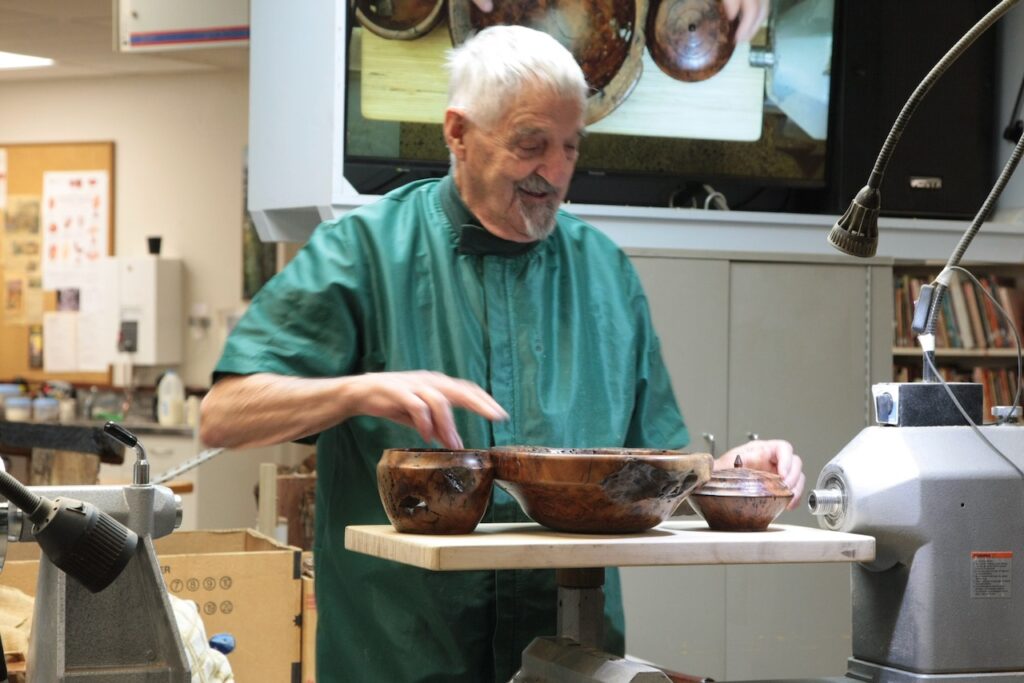
Next up was a nearly finished turning of a large, three sided, winged bowl, too big to fit over the bed of most lathes. This attractive piece, pepper I think, was thin-turned with stepped-down thicknesses on the underside of the wings. Having lots of natural cavities, the challenge was how to remove the tenon and finish the foot. Suggestions indicated that this was not as difficult as it might seem. Dick said that covering it with gladwrap and using a vacuum would be a satisfactory method. Alternatively taping it to a big faceplate.
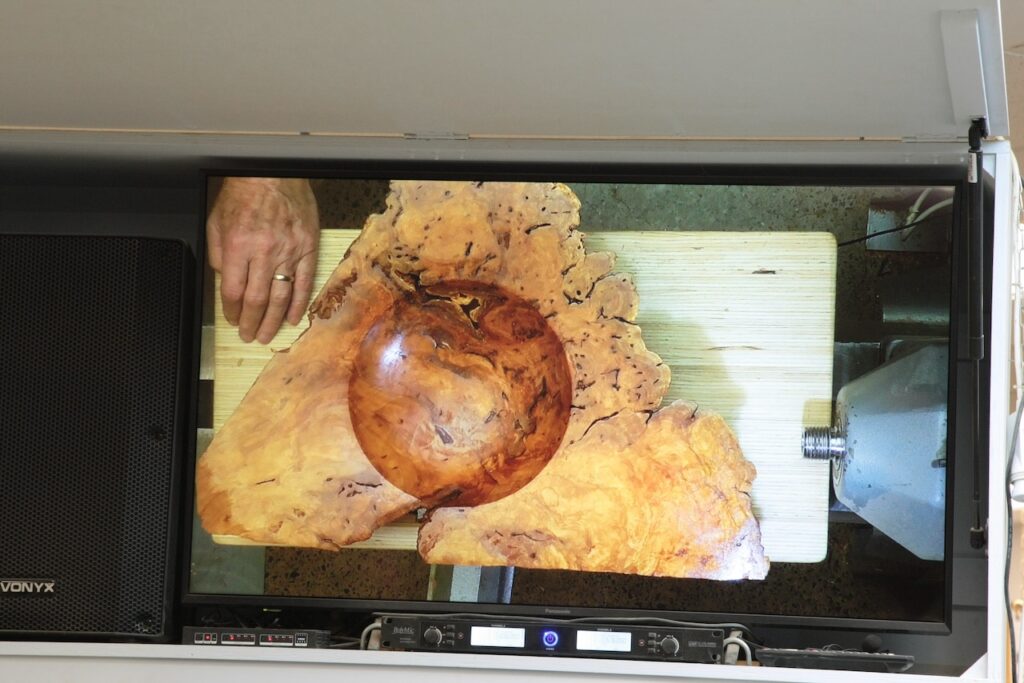
Bruce showed another burl which was milled in such a way to retain a small burl on one face, and from which a number of small burls had already been cut off for various types of use. He had a live edge pepper turning, and then unwrapped a pepper burl which he had started to turn. This burl had a very coarse bark adorning the top, and was semi turned with straightish sides angling towards a foot near the bottom. The problem with this piece of burl, Bruce said, was the triangular, V shape in which it was cut made it difficult to envisage a design which maximised the bark, grain and colouring etc. Much discussion ensued with the final outcome being that it needed to be re-positioned between centres so that the top would be better balanced. Some height would be lost off the bottom, but it would be an opportunity to create a more graceful external shape for the sides. The top would probably benefit from applying the 1third 2 thirds rule for determining the ratio of bark to bowl size.
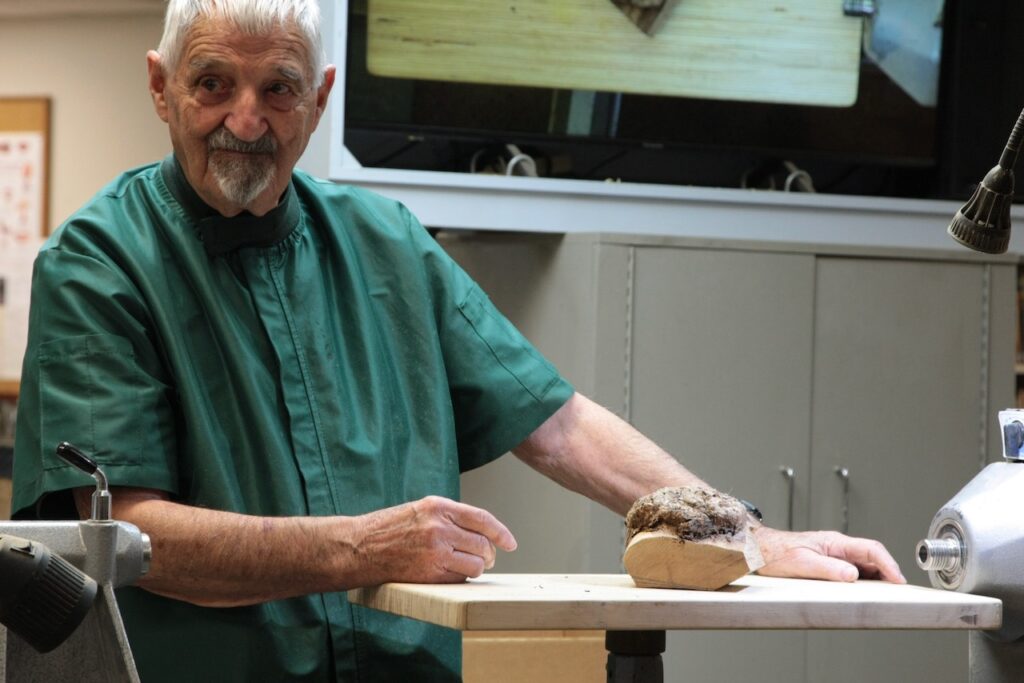
The last piece of wood that we looked at was a small burl, I’m guessing about 80mm diameter, sitting fairly centrally on a length about 120mm. The consensus was that this could quite simply be turned in to a nice bud vase. Bruce positioned it between steb centres in long grain mode and turned a tenon on the bottom. Grabbing it in the chuck, he drilled a 21mm hole the right length for a glass insert, before shaping the neck with a spindle gouge. With a bit of off-lathe finishing, this will become a distinct and unique bud vase.
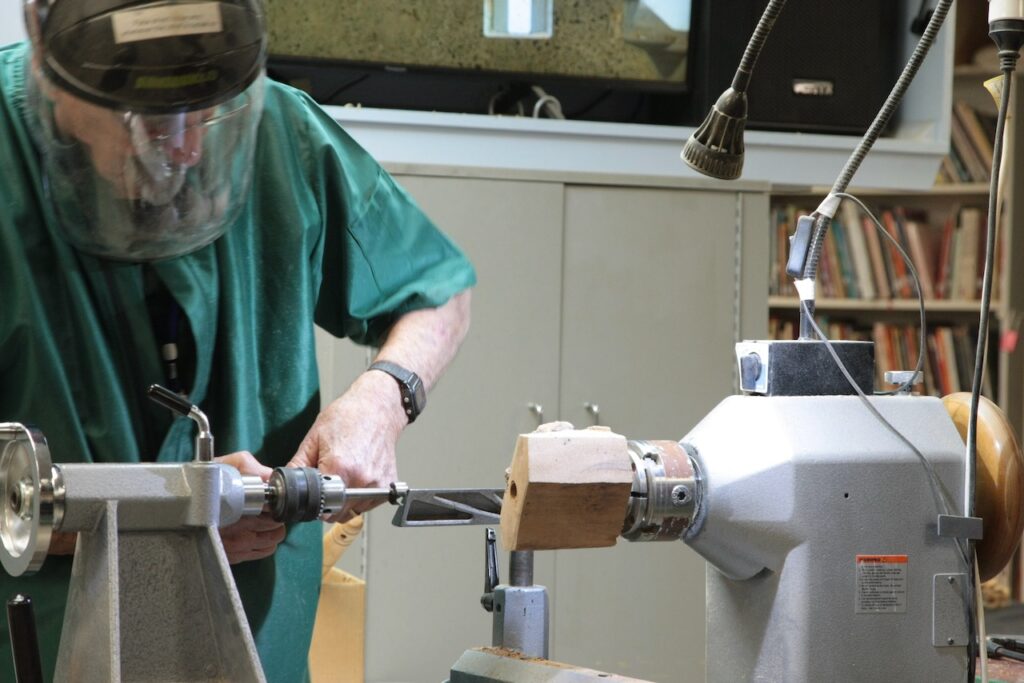
Bruce’s demonstration was an interesting foray for all present in to the endless possibilities for design and form options with these beautiful natural wood formations. Sometimes they look impossible to get something out of, and at the same time, actually have so many possibilities that it is difficult to know what is the best option. Thank you Bruce, for closing out our third term with a thought provoking examination of design opportunities.