Club Meeting: 24 July 2024
Report by: Ian Connelly
This demo was of two of the projects the Guild does to support the community. Wig Stands are donated to Look Good Feel Better in support of those going through chemotherapy. Butterfly Boxes are in support of Child Cancer, where parents of those children that don’t survive are given a glass butterfly which is presented in a hand turned wooden box, rather than a small cardboard box.
Both of these projects have multiple project sheets.
Wig Stand
Wig Stand Shafts
Wig Stand – Ball & Vase Shaft
Wig Stand – Drunken Shaft
Wig Stand – Handshake Shaft
Box, Butterfly #1
Box, Butterfly #2
Box, Butterfly #3
Box, Butterfly #4
Wig Stand as turned by Dick for the Demo.
BASE
Mount blank for base between steb centres, check everything is tight, check speed is 500rpm.
With a set of calipers set to 46mm mark the spigot on the bottom of the blank, and then cut the spigot.
Remount the piece in the chuck (standard 50mm jaws). Speed up the lathe and shape the top surface.
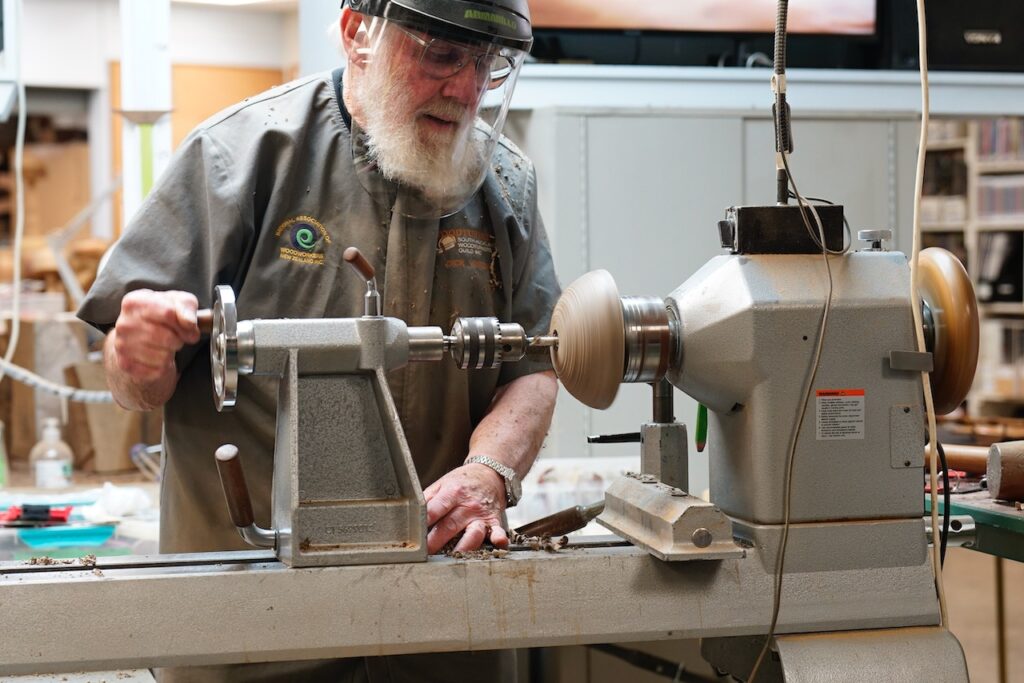
Drill a 26mm hole for the stem, and clean up the surfaces with a sharp gouge (push cut) and sand.
Reverse into Mini Spigot Jaws and tidy up the bottom surface and sand.
HEAD
As with the base – Mount between stebs, but spigot 46mm, mount on spigot.
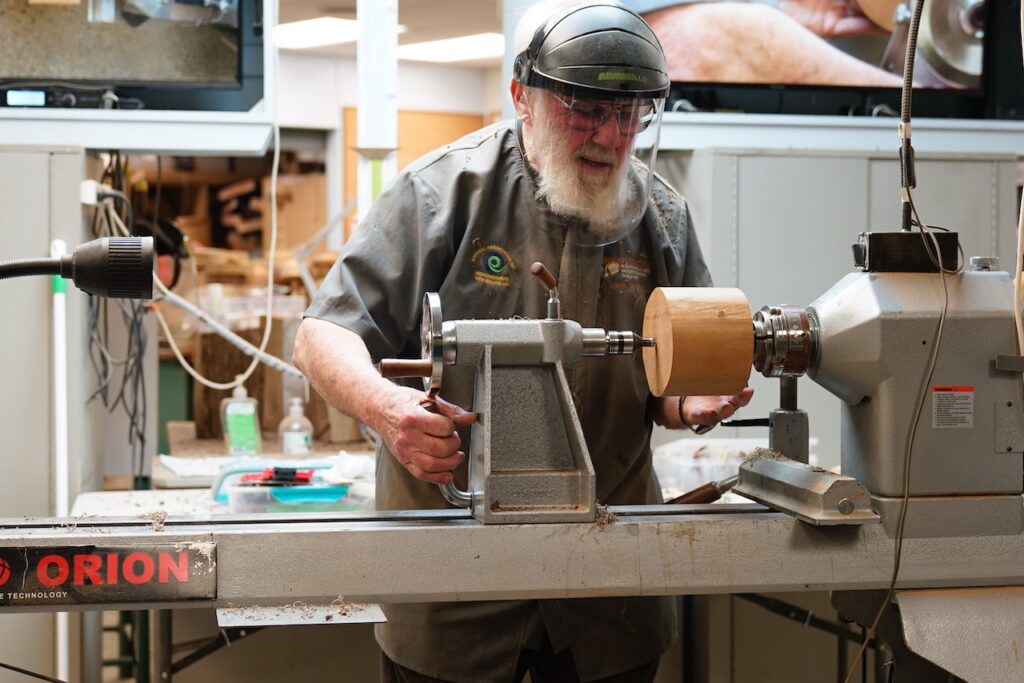
Because Dick was using timber with the grain running along the bed of the lathe, he was able to round the piece with the Spindle Roughing Gouge. He then cleaned up and straightened the bottom with a small bowl gouge, and sand bottom.
Drill a 26mm hole for the stem.
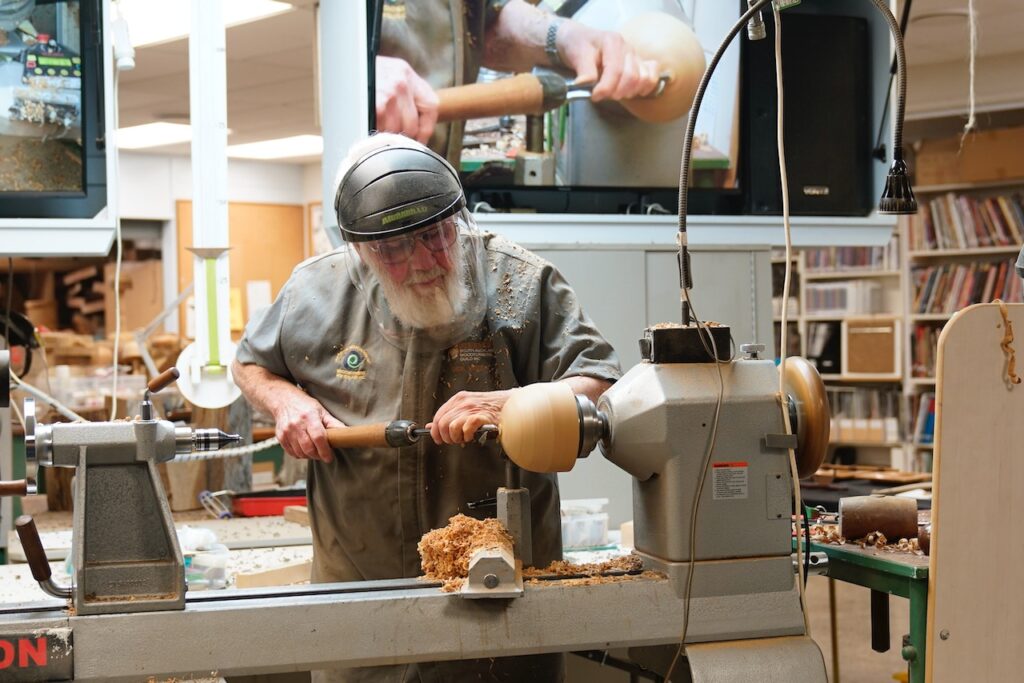
Mount on Mini Spigot Jaws, and shape the top. Sand the top,
STEM/SPINDLE
Mount between steb centres, round with the spindle roughing gouge.
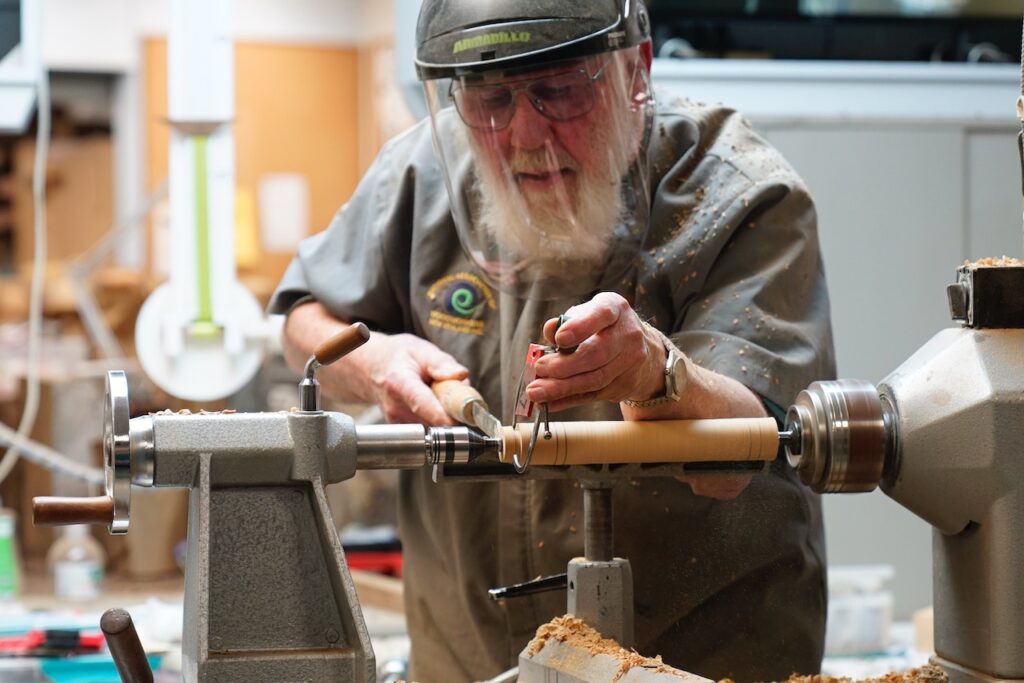
Dick then marked up the pattern he was planning for the spindle – 14mm each end for the spigot, then a bead at each end. From the top he then marked out for a cove, another bead then a longer ogee shape.
The spigots were formed with the parting tool. The parting tool was then used to mark out the transition points of the other features.
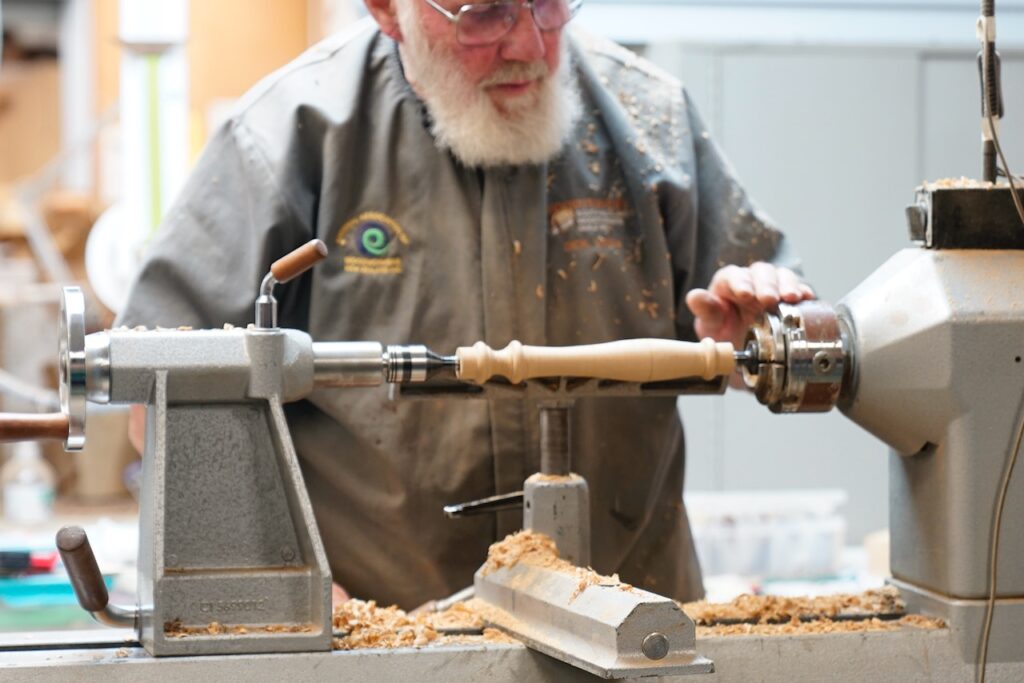
A spindle gouge was tehn used to form the beads and the cove, and then back to the spindle roughing gouge the shape the ogee. Sand it all up.
The next process is you take it off to test fit, find your spigots are too big, put it back on to trim….
Finally you glue it together with a good wood glue, and spray it with lacquer/polyurethane or another hard finish that will not transfer to the wig.
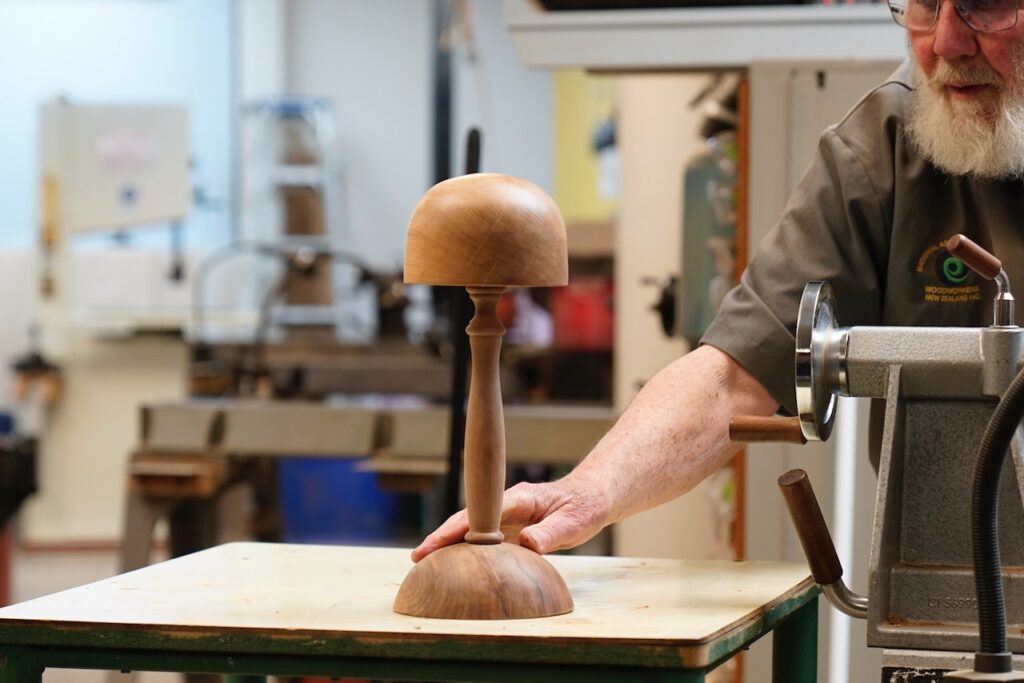
Butterfly Box
Mount between centres, make a spigot.
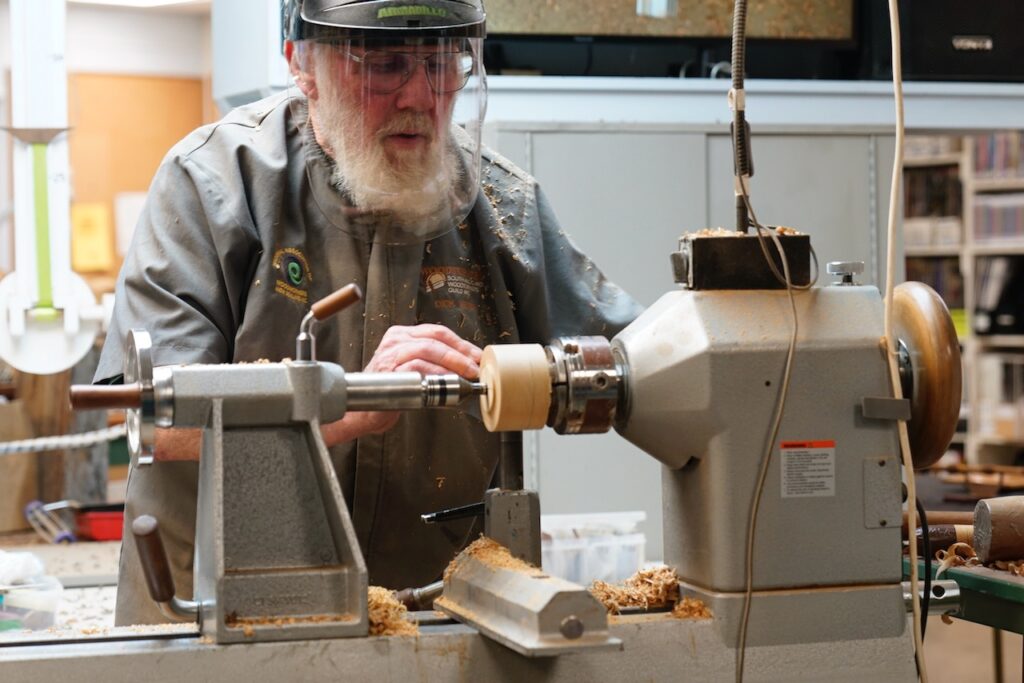
Mount on the spigot – tailstock up and round the wood.
Put a spigot on the other end.
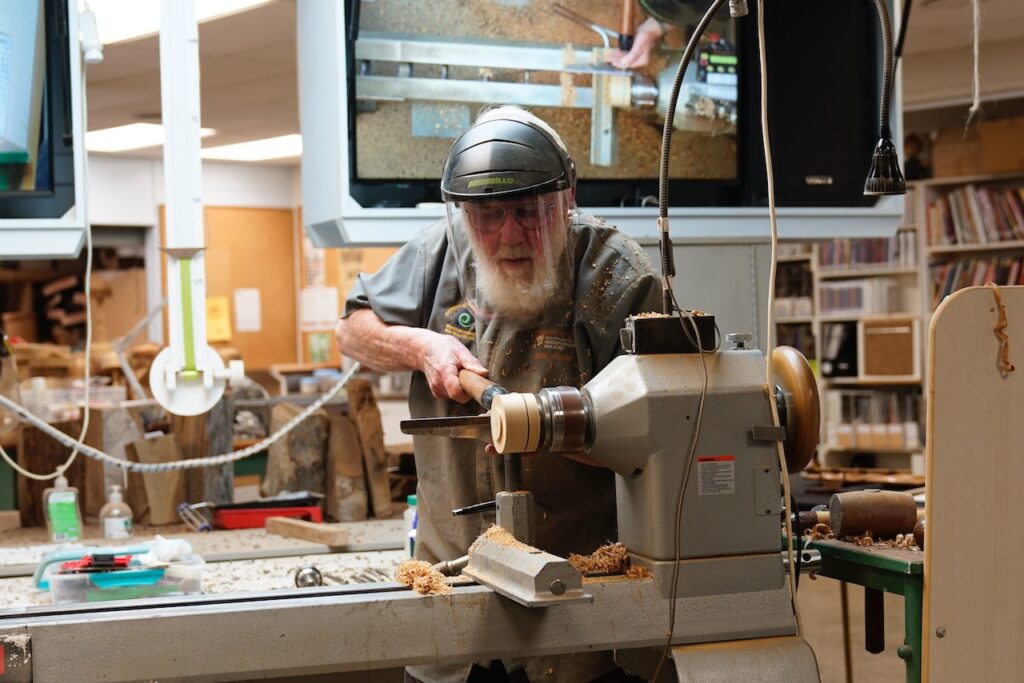
Part off the base, the lid remains in the chuck.
Clean up the lid, make a step in the edge as the lid will sit inside the box.
Mount the base in the chuck, initially hollow with a bowl gouge. Dick finished the hollowing with the Soren Berger end grain hollower. (this could be done with the square scraper)
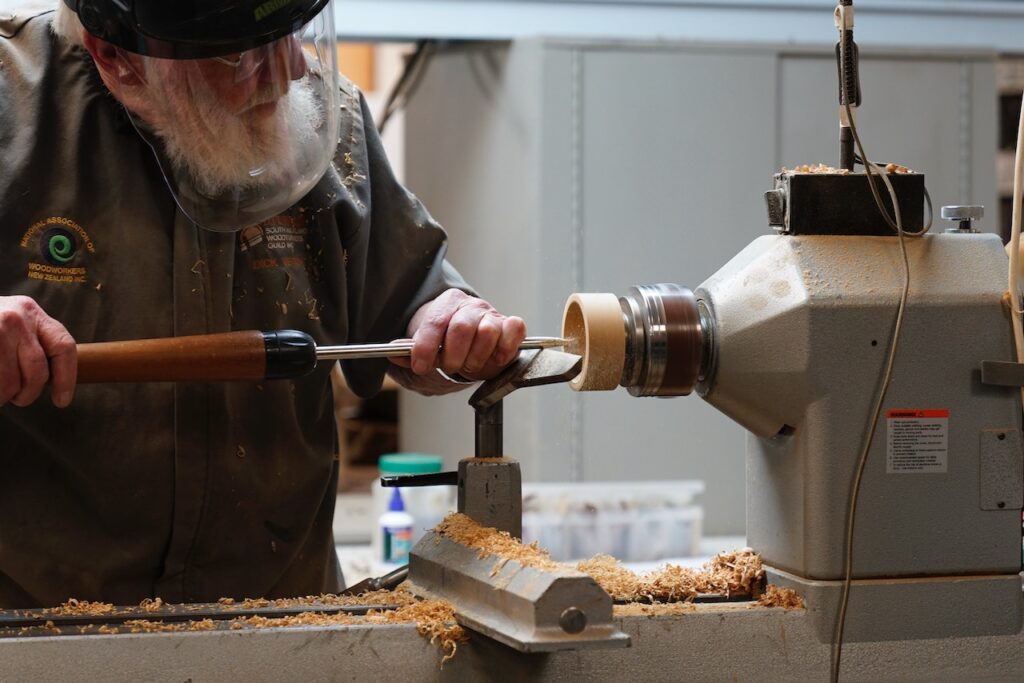
Disk then worked on fitting the lid, tuning the size with a skew as a scraper.
Your can then tidy up the spigots using a method of your choosing.
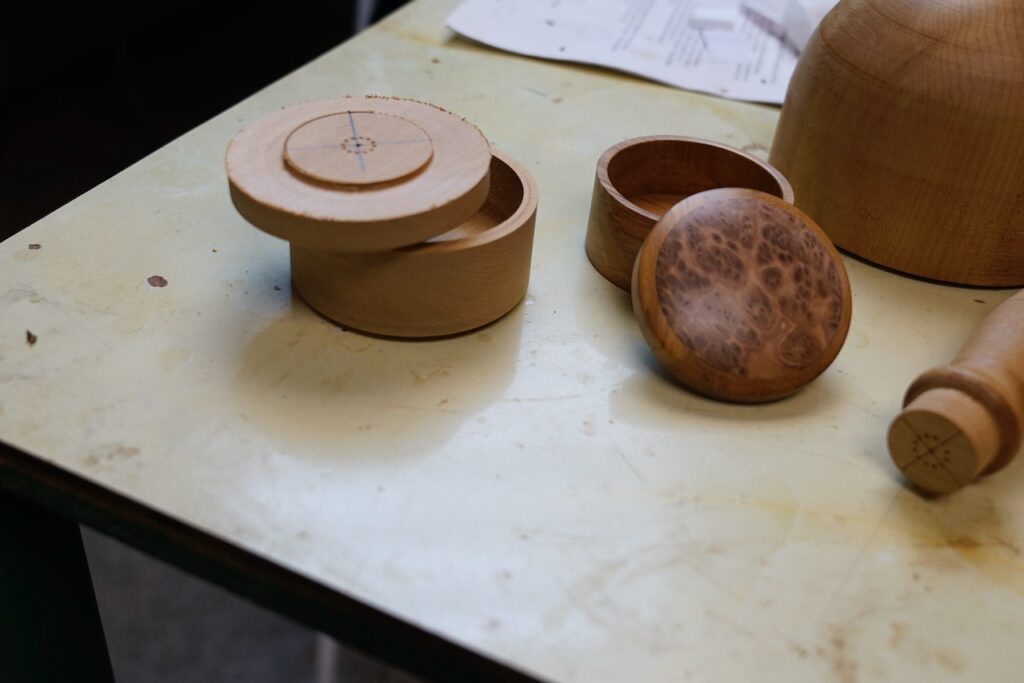
As with always it is a pleasure to watch Dick with some wood and the chisels, always got a tip to share and demonstrates a mastery of the tools we can all aspire to.