Meeting: 11 September 2019
Report by: Murray Wilton
The first problem to resolve is “what exactly is a bonbonnière”?. Well, if you know what a bonbon is you are halfway there. Of course, it’s French for candy, so a bonbonnière is a container for bonbons. But Warwick’s subject was “How to make the world smell sweet”, and it was fragrance, rather than a carbo-hydrate fix, that was to be demonstrated. Warwick gave a short dissertation with samples of various small containers, from an incense burner dating from the 4th century A.D. to various types of fragrance containers for joss sticks, potpourri and coloured scented wood shavings. The Day home must be redolent of wonderful aromas! The word “pomander” was used throughout the demo, another lexical item of French origin meaning a globe made of scented materials, or the container for them. Thus, Warwick’s presentation was to be the turning of a pomander, with resin lid, texturing, colouring and vents.
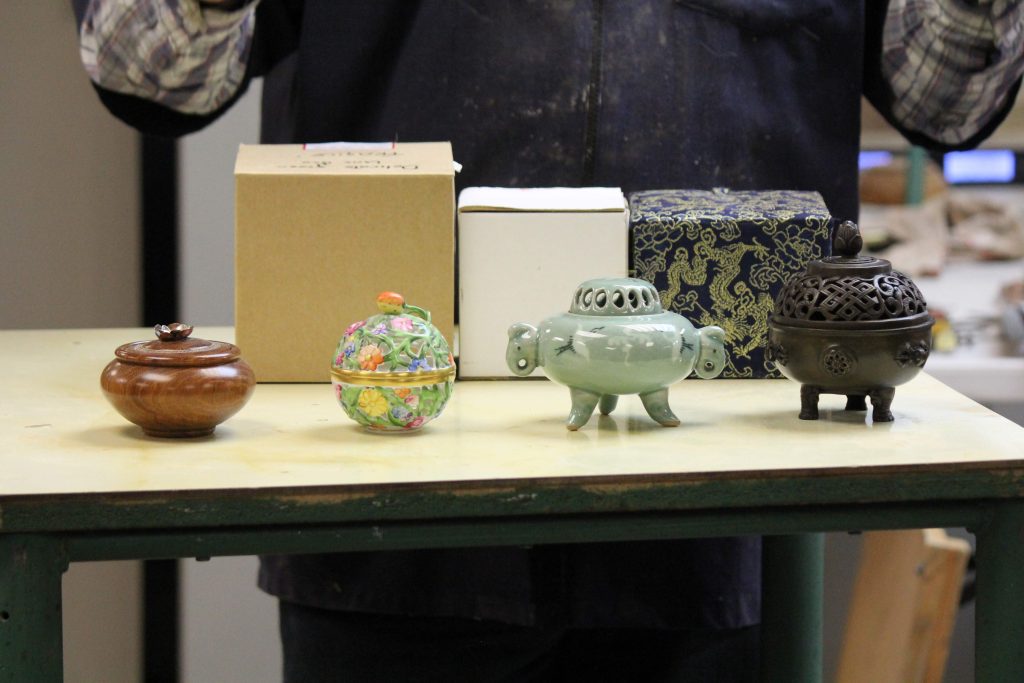
Reacting with his usual aplomb to the audience banter, Warwick selected from a dazzling array of carefully honed tools and gadgets (he’s a self-confessed tool junkie) a spindle roughing gouge to turn square to round, the block mounted between chuck and steb centre. Rounding included marking the spot where the lid would be separated from the body, if a wooden lid rather than a resin one is chosen. After parting off the lid he used a bedan tool to form a spigot. (What a learning experience! This reporter, at least, has never heard of a bedan. Warwick explained that it’s the one tool with which you don’t rub the bevel.) [Day Hint No. 1: when you buy new tools pay cash, get cash out when you are at the supermarket, tell wife inflation is rife in the food bills.]
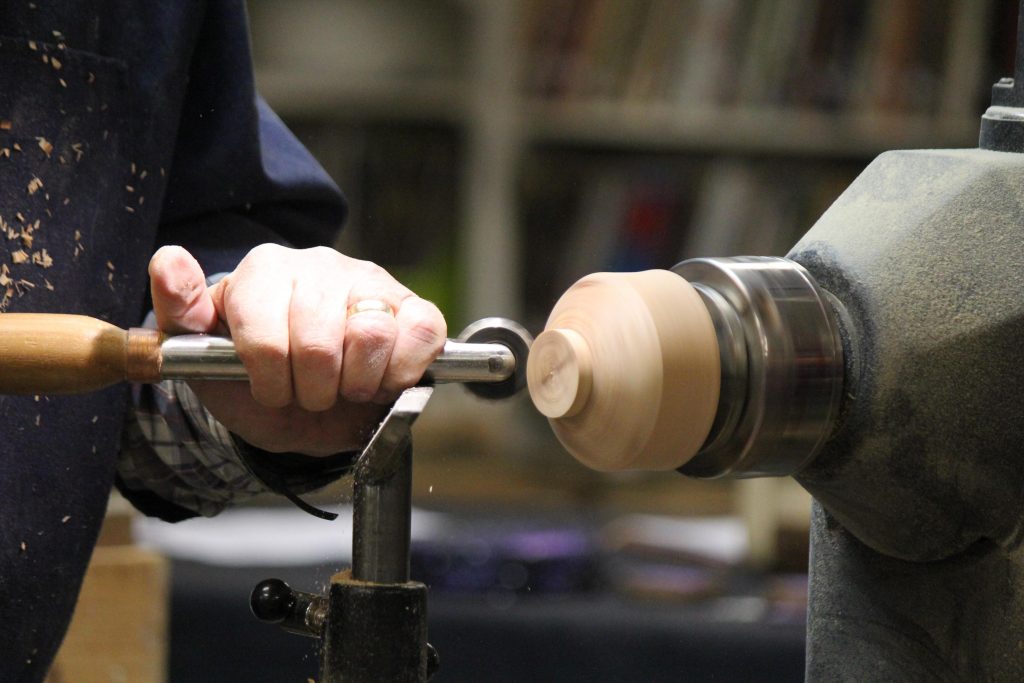
Warwick then rounded off the bottom half of the pomander, finishing with 400-grit sandpaper in preparation for texturing. The piece was then turned around and installed in cole jaws in order to turn off the first spigot and form the top half of the “bowl”. [Day Hint No. 2 (serious one this time): to avoid tearing when sanding end and difficult cross grains, apply sanding sealer to the work, then sand as usual.] Next he marked and drilled the vent holes using a brad-point drill, yet another item to add to your wish-list of must-have tools and equipment.
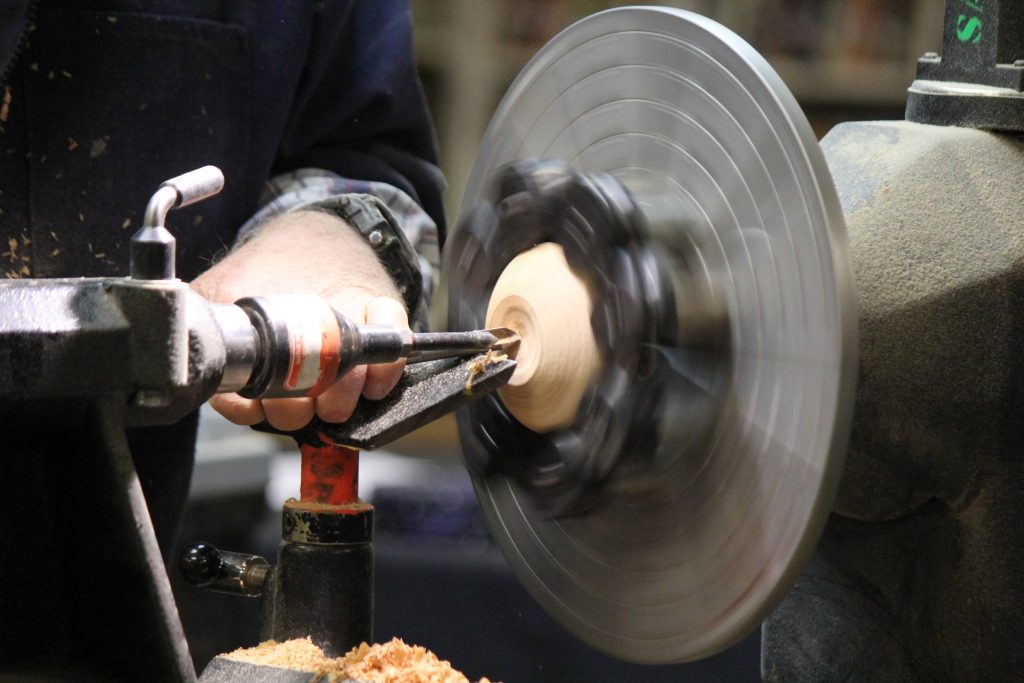
After texturing the upper half of the “bowl”, Warwick applied colour using gilders’ paste softened with sanding sealer (loves his sanding sealer, this turner), using his wife’s kitchen scouring pad to finish off. Then the hollowing can begin, first marking where the lid will sit. Warwick used a 10 mm bowl gouge to start the hollowing and, when a depth of about 25 mm was reached, changed to a spindle gouge. From his vast collection of tools he chose a cup tool, a hook tool and the now famous bedan to achieve final hollowing. [Day Hint No. 3: use slower speeds for hollowing.]
The resin lid can be made by pouring resin into a mould with a wooden peg for fitting into the chuck, once again holding the other end with a steb centre. Warwick set the speed at 1500 rpm working from slightly above centre on the tool rest (normally the tool is below centre for timber turning). Out came an Easy Wood Tool (carbide cutter for scraping), because as Warwick says normal bowl gouges tend to chip the resin. For finishing work, wet the sandpaper to stop it grabbing the grains and finish with wet sanding pads.
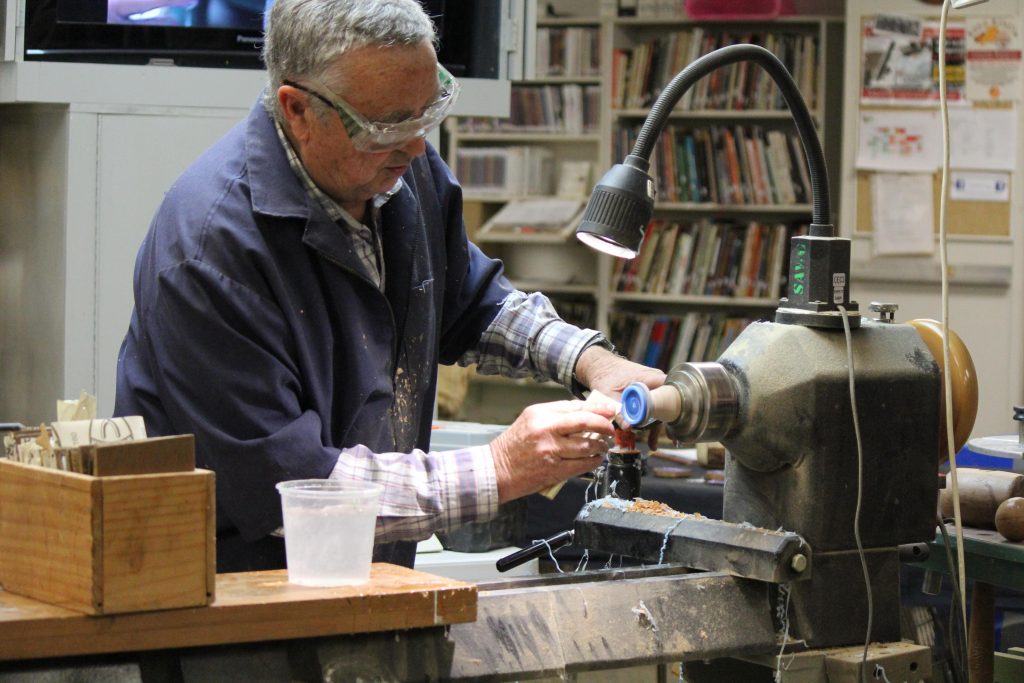
Another great demo from a master turner with a flair for clear and informative instruction. Many thanks Warwick, both for the demo and for adding some useful words to our vocabulary.