Photos : Ross Johnson
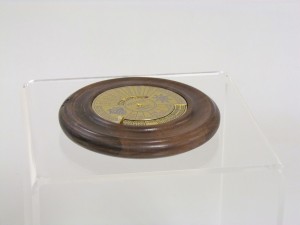
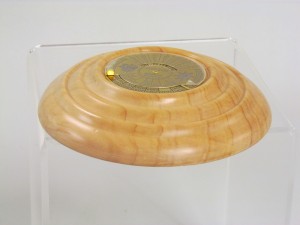
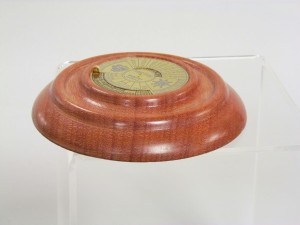
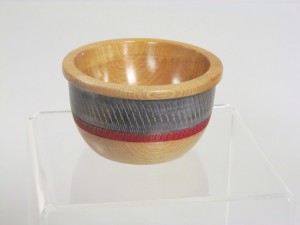
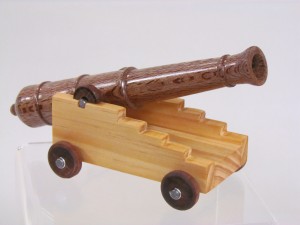
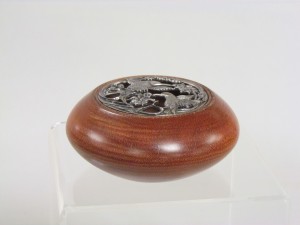
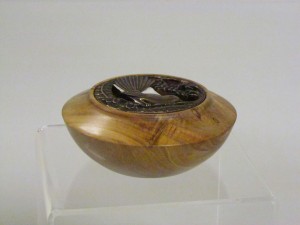
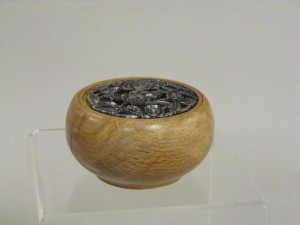
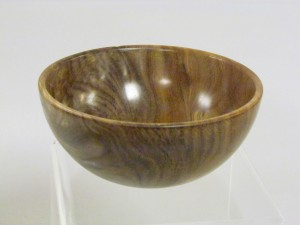
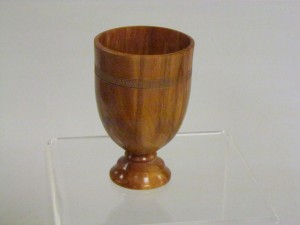
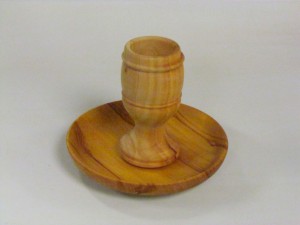
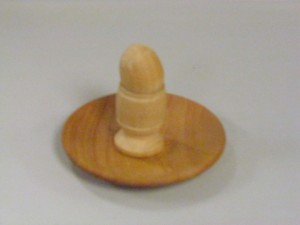
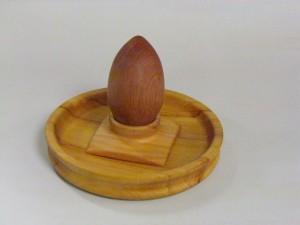
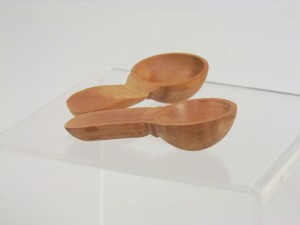
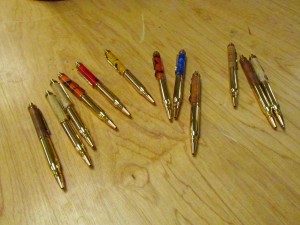
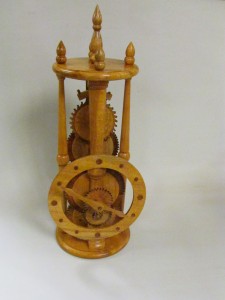
Photos : Ross Johnson
Club Evening; 24th June 2015
Report by: John Smart
Graeme showed some of his work on these Egg Cups with hats on.
He started with some of his thoughts & work on this subject as there are many options; Pointed versions ex Richard Raffan, Round & full bodied ex Grey Lynn. Stories regarding Runny Eggs with lips to hold the juices. Ice Cream look-a-likes all made from different timbers. He makes all of his from all forms of wood like Tasmanian Blackwood which after use ends up with a good gloss plus all other types of supplies coming from the firewood bin and ever looked at wood locker.
His next subject was PENCILS 3 years ago he purchased 3 dozen Pink carpenters pencils and since then has never found one where he stores them he of course blames the Nombessssss.
We then got to the nitty gritty what size egg do we use and that required more discussion. It ended up as a size 7 egg you will find all the dimensions in our projects file EGG CUP.
Graeme created a entertaining evening and showed the skills he has plus a lot of technical advise that he uses which we can all adapt where necessary ourselves
Projects File; Egg Cup
Thanks Graeme
John Smart
Club Meeting: 17/6/2015
Author: Alistair Hancox
The St John volunteers delivered a very informative presentation on Wednesday night to those in attendance. We were given some sound advice on what to do should we or someone close by get into a spot of trouble. An interesting point made was that 30% of all calls to 111 aren’t for urgent emergencies. A key message from the evening was how to identify when to call the emergency line, and alternatively when to get yourself to A&E. If you’re even in doubt on whether to dial 111 for an ambulance, phone Healthline on 0800 611 116. A registered nurse will be able to provide you with advice. It’s important to note that in some cases, it may be quicker to drive the person in need to the hospital or A&E, rather than phoning for an ambulance.
Their main points of the presentation can be broken down into a number of key topics, outlined below.
Bleeding
The first question to ask is what’s the severity? Is if from a main vein or artery? If so, call for an ambulance. Some wounds can be associated with injuries beneath the skin. The first priority with bleeding, is to try and stop it. Apply pressure and wrap with a pad and bandage. If blood is leaking through the bandage, add another pad and wrap again. Do not remove the previous bandage.
Triangular Bandage
It’s important to elevate any bleeding and bandaged part of the body. We were given a demonstration on how to fold a triangular bandage to rest a wounded arm in a sling. During the audience participation, the room began to resemble a scene from the television show M.A.S.H. It was just as entertaining too.
Foreign Objects Embedded in a Limb
Do not remove! Leaving it in until you are being seen by health professionals will avoid additional internal damage. If you can move and you can manage the bleeding, get to A&E. If not, phone an ambulance.
Amputation
Apply pressure to the severed end. Take the detached appendage with you in a sealed plastic bag. Do not put it on ice. This will damage it and make reattachment and recovery harder. If you can get yourself to A&E, do so. If not, phone an ambulance.
Heart Attack
It’s important to recognise the early warning signs: Chest pain, pain down the left side of the body, rapid or irregular pulse, blue colouring of the skin, or a feeling of impending doom. If someone is having a heart attack, call 111 and put them in the W-position. This is lying/sitting on the ground with your knees brought up. This will take some pressure off the heart.
Eye Injury
Don’t rub the eye. Try and flush out anything that gets in there. Look straight. If you can’t get out something which has got in your eye, go to A&E.
Strokes
A stroke is caused by a blocked blood vessel in the brain. Recognising the signs of a stroke are important (Facial droop, loss of mobility in ones arms or legs, slurred speech, etc.). It is very important to get the victim to the hospital as quick as you can. At the hospital, an injection is given which can break down the clot. This must be administered within 2 hours of the stroke for the best chance of recovery.
CPR
CPR should be done on someone who has become unconscious, isn’t breathing, and/or doesn’t have a pulse. The first instance in this situation is to call 111 for an ambulance, then begin giving CPR. CPR should be given in a sequence of 30 chest compressions to two breaths. You should be aiming to compress the chest by about 1/3. The patient should be on a firm surface, like the floor, not a bed. Chest compressions should ironically be to the beat and timing of Another One Bites the Dust by Queen. Keep CPR going until an ambulance arrives. CPR will unlikely bring someone back by itself, though it should keep the patient alive long enough to get a defibrillator to them. Defibrillators are becoming common in places like supermarkets or other community centres. They are very easy to use and increase the chances of survival dramatically.
Recovery Position
The recovery position should be used when the patient is breathing and in a stable condition. Lay the person onto their side with their lower arm pointing straight up. Their head should rest on this arm. The lower leg should point straight down. Bring the knee up of the other leg.
Choking
If someone is chocking, grab them from behind and give them 5 strong compressions to the chest (Not the diaphragm!). Compressions to the diaphragm can cause damage to a victims internal organs. Follow up the 5 compressions with 5 hard smacks on the back. Repeat as necessary.
Club Meeting: 4 June 2015
Report by: Bill Alden
Photos: Ross Johnson
Rolling Pins can be traced back to the 9th Century. Commercial production of them started in the 18th Century and were made from Pine, probably a harder wood than we are used to. They were also used for crushing Oats. In the late 18th Century JW Reid patented a rolling pin with a central rod handles on each end which could be held firm in use. In the USA 650 to 700,000 are sold pa. They are made out of a wide range of materials. Some are patterned to leave an impression in the dough.
They can have handles or be just a straight cylinder with many different diameters and lengths. Smaller ones are used for icing sugar. A French rolling pin has a taper from the centre to each end.
Colin demonstrated some beading with a bead cutter on a small pin in order to pattern the dough. Black Maire is a good wood as it is heavy and turns well.
We discussed ways of keeping the cylinder equal along its length. Sight the tool rest with the bed and follow that, another method is to Part down to a given size using callipers slightly larger than the required finished diameter.
Thank you Colin for an informative evening.
Club Meeting: 27 May 2015
Report by : Ian Connelly
Photos: Ross Johnson
In typical Terry fashion the demo started with a story about the history of the caddy spoon and how valuable tea was etc. etc. then he finished by saying what he read on the net was very interesting and we should all go and read it because he had forgotten and just made up everything. Terry had many different spoons to show, which ranged from functional to purely decorative.
Caddy Spoon
Mount a 47 x 47 block, in a 50mm chuck with a steb centre in the tailstock
Round with the roughing gouge
Smooth with the skew
Mark out a ‘ball’ at the spoon end, using a parting tool to defined the sides and round roughly
Shape the handle
Terry used a sharpened pipe to tidy up the rounded ball (ideally the pipe diameter is less than the ball diameter ehh Terry)
Remove the tailstock, and clean up the end
DON’T PART OFF YET!
Take out of chuck and use bandsaw to split down the middle (the square end makes this easier)
Make a jam chuck to hollow the spoon, some people may find the hot melt is also required to help hold it.
Sand the spoon and handle.
Cooking Spoon
Mount flat piece of wood between steb centres. (Terry used wood about 12 x 80mm)
Turn the handle
Sand
Part off at end of handle
Shape spoon with bandsaw, grinder, sander, dremel …… (hand tools probably work too, but Terry avoids these)