Wednesday 2nd December 2020
Report by Emma James-Ries
This week we were treated to a well organised demo by John Whitmore. John’s demo was solely focused on parting off and all the tools and techniques you can use to achieve this, a first for our club!
I will note here, that I felt having a background in engineering would have been very beneficial in my understanding of all the techniques in this demo, but alas I still gained a lot regardless. John started by explaining his title, a quote and exchange between Romeo and Juliet, highlighting the ‘sweet sorry’ that comes with the parting off and the conclusion of a project.
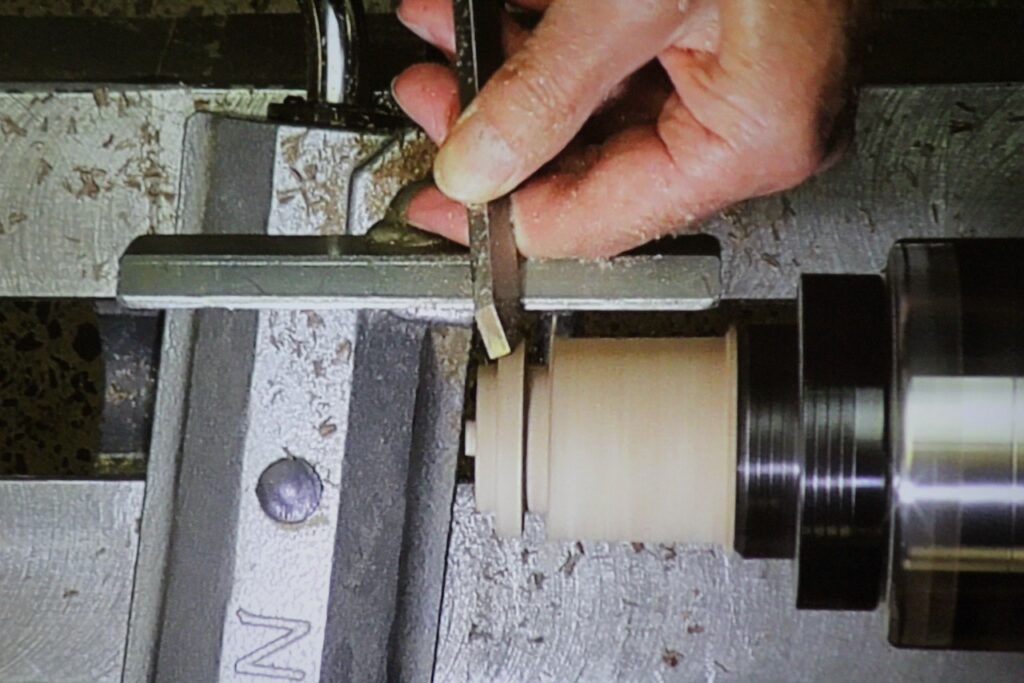
To start with John demonstrated the advantages of straight sided parting tools. A straight sided double beveled tool, is very useful for making shallow cuts to create beads, but can bind if parting off in one cut. He showed us a Sorby beading and parting tool, demonstrating some bead work with even precision. John attached the timber in 30mm spigot chuck, which has much deeper jaws, ideal for handling the pressure that comes with parting off.
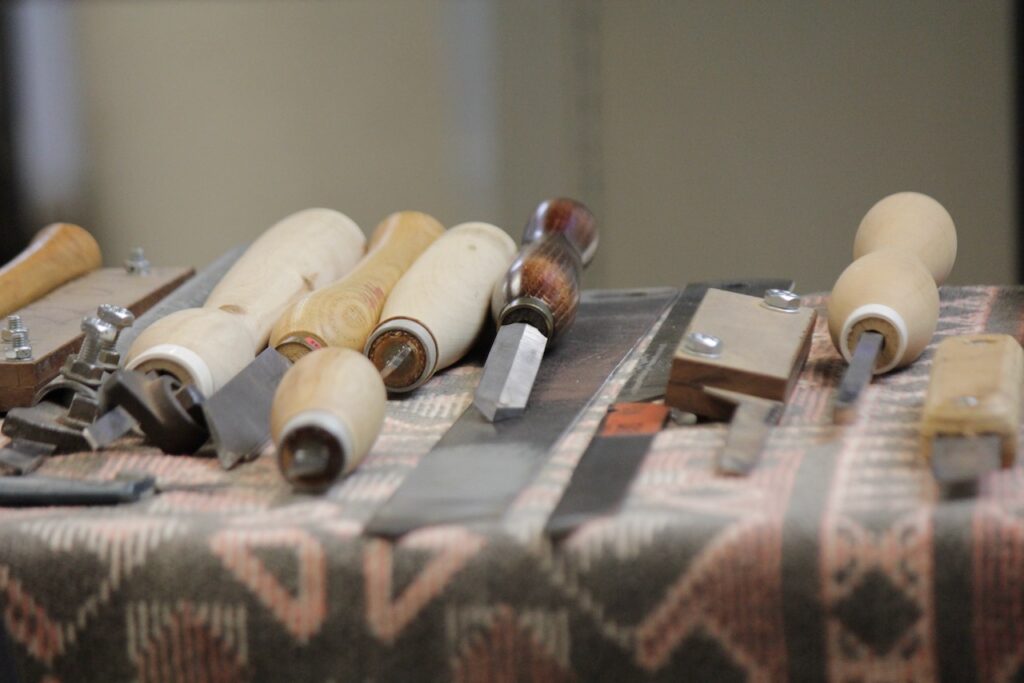
He went over the uses of hacksaw blades and how to convert them into parting tools. Strong, industrial steel is ideal and making the cutting edge just behind the tooth edge may be best. Banging the blades with a heavy duty hammer before sharpening, may spread the metal slightly and provides clearance behind the cutting edge.
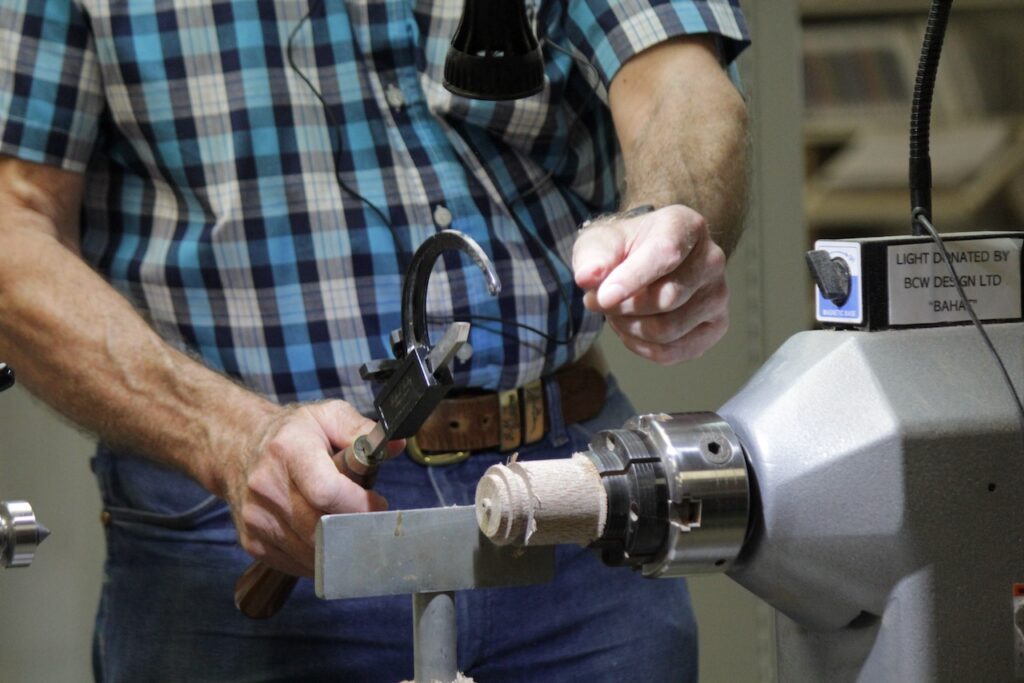
In the next stage in the demo, John showed us a range of tapered parting tools. The benefit to tapered tools is it creates a gap between the timber and the tool, behind the cutting edge, to avoid build up of heat friction and binding. The most common tapered tool is a diamond profile, which is what the club stocks at all the lathes. A parting tool with a fluted base can be good across end grain. John had glued a metal rod to the bottom of the flute, to rest on the tool rest. Incase of a dig in, it wouldn’t damage the rest, a good tip!
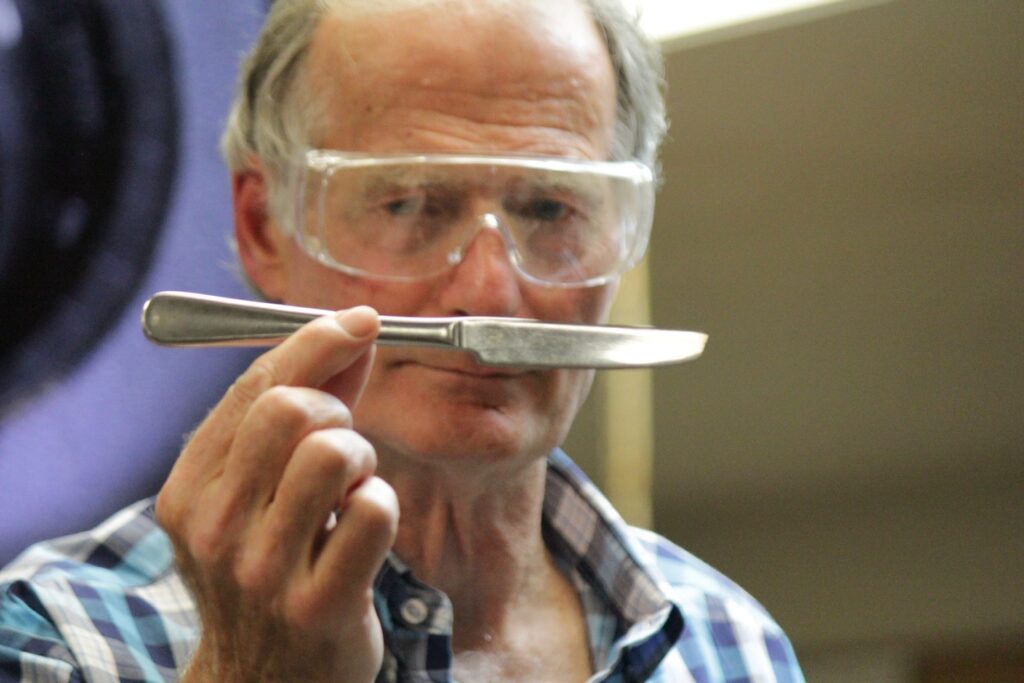
John let us know that another good option for parting off, was an engineering holder than you can purchase from Machinery House (Just make sure they’re in stock before making the trip!) The engineering holder could then be set into a gas pipe handle to give maximum stability and strength. Another unusual tapered parting tool that was shown, was one made out of a kitchen butter knife! At this point in the demo John asked for help from the biggest cynic in the room, which was of course Cam Cosford! Cam was asked to part off a piece of Tawa dowel, using the kitchen knife. After a small dig in, he managed to do it twice, a good sport thanks Cam. A larger Bowie/hunting knife can also be used in the same way. Just a note when looking for knifes to convert, make sure they aren’t tapered towards the tip. The last example of a parting tool shown, was a straight sided Kelton Bowl Saver that could be used for very heavy duty parting. Bedans and straight sided keyway steel, can also be used for the same purpose.
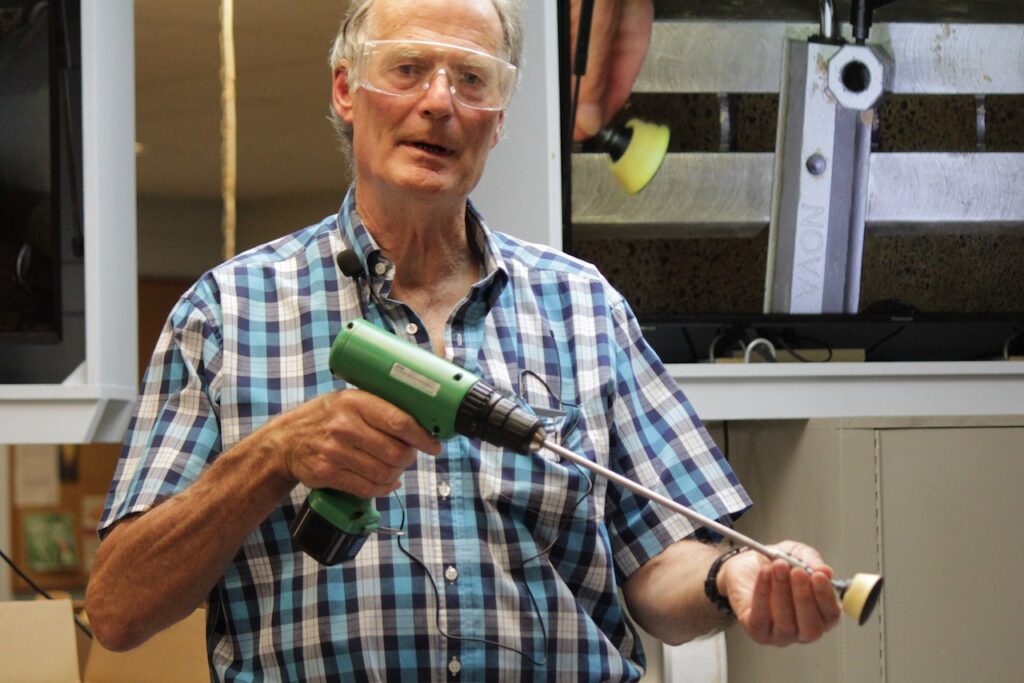
The next part of the demo went into depth around different odds and sods that are useful to know in woodwork. John showed us his creation of a long shafted sanding arbor that uses hex screws, to avoid wobble and damage to the shaft that can occur with standard grub screws. John then had to create his own sanding arbors to fit the hex screws, as no one currently makes them. He had struggled a bit to cut the padding neatly, however suggestions of Stanley knives and hot wire could be used. Another little adaption to the arbor, was creating a sliding handle to use to steady the shaft when sanding, a very useful idea. John also went over the different tools and handles that can be created out of obscure objects, including a blade from broken garden shears and a scraper made from a garden trowel! He showed us how to sand a piece of gas pipe evenly on a sanding disc and Texas style tool rest table. I have been very impressed with John’s ambition and can do attitude towards making his own tools and creating solutions to problems that can arise in woodturning.
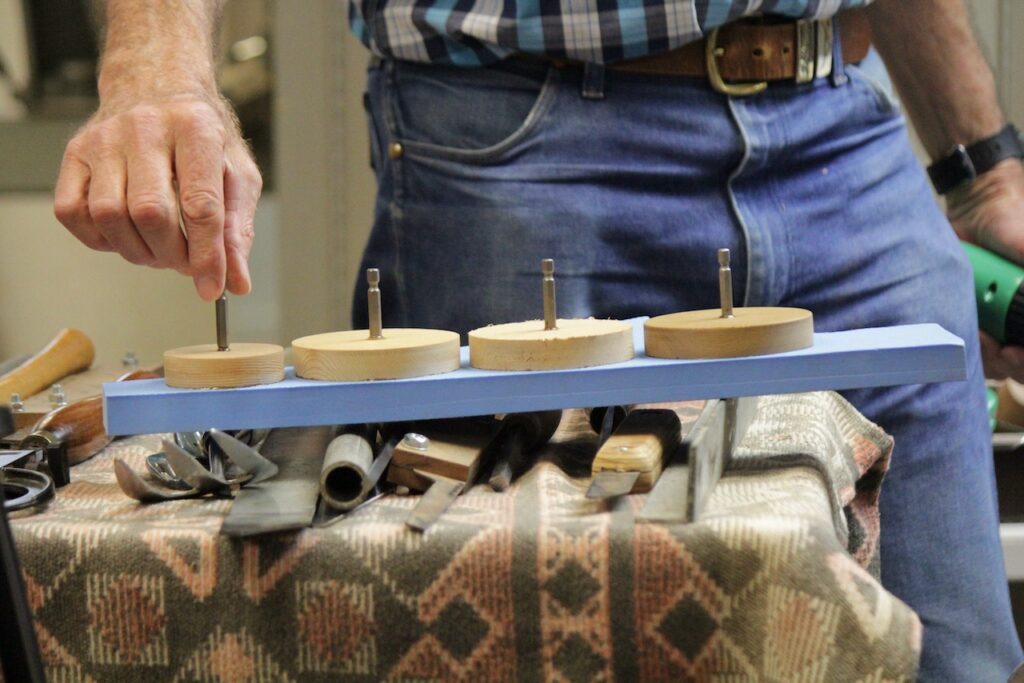
To finish up the demo, John showed us a piece of Norfolk pine that he’d found on the side of the road. He’d used PVA glue as a filler and showed us the result as an alternative option to resins. Also another clever little idea, was to save the stubs of the pine branches to create little boxes that still contained the unique branch growth pattern. A very knowledgeable demonstration that was executed with precision. I definitely learned a lot, thank you John!
(ed: caution should be exercised when using very hard steel for making woodturning tools, a dig in is likely to shatter the tool. As always use a impact rated full face mask whenever possible when using the lathe, and stay safe)