Club Meeting: 21 June 2023
Report by: Kieran FitzGerald
What has the old master got in store for us this week? Dick’s demos always inform and entertain, so we wait expectantly. It starts off in a pretty routine manner – Dick takes a wet pin oak blank about 90 x 90 x 135 and turns it round between centres. After making a chuck bite at one end he mounts it in 50mm chuck jaws.
Applying the rule of thirds, he pencil marks at 45mm intervals and uses a spindle roughing gouge to quickly turn a pot shape. After facing off the neck end he takes a short 25mm forstner bit and commences to drill out the centre. He switches to a longer auger bit of the same width to complete drilling to a depth of about 125mm. The purpose of using the shorter drill bit to start the hole is to stop it wandering off centre. All the way along Dick is explaining his actions in detail so turners can take full advantage of the knowledge and experience he is passing on to us. Further tips about drilling included sharpening your drill bits and making a handle extension for the tailstock to allow extra leverage.
Dick hollowed the pot, starting with a spindle gouge and switching to a hollowing tool. He then substituted a partially completed pot from his magic box of tricks – the first of many pre-prepared pieces – and showed us how to take the spigot off using a hollow form reverse mount. This is pretty much a DIY tool consisting of a shaft with a sanding mandrel at one end and a cone which floats on the shaft and tightens with grub screws. The cone is fixed to a small faceplate. The mandrel fits inside the pot and secures the base against the tailstock. The cone fits inside the neck and is tightened down at the appropriate length to hold it snug. The whole affair secures the foot nicely to allow the base of the pot to be worked on. I’m guessing that because of the interest in this piece of apparatus that there will be a few more versions appearing in the workshops of club members.
So why is the demo named “Pot Black”? The answer became obvious as Dick produced pot after pot from his magic box and showed us techniques for enhancing the appearance by blackening them in a manner which totally highlighted the grain pattern.
He started with an NGR (non grain raising) black wood dye which he applied generously with a brush. Then he showed us how a significant amount of colour had penetrated through the wood to the inside of the pot. Next he took a pot which was already stained black, and simply put, didn’t look too great. After rubbing down with wire wool and applying a coat of Liberon Finishing Oil, the piece took on an improved, but not spectacular, appearance.
The next example was a pot which had been sand blasted, black stained and then rubbed down with wire wool. The sand blasting accentuates the grain pattern by taking away the softer wood between the grain lines. From experience Dick has learned that polishing grade crushed glass does the best job because other abrasives are too coarse. Then Dick thoroughly rubbed on Liberon Liming Wax with a soft rag (the tin says to use Liberon wire wool – Dick suspects that is a marketing ploy). After 3 to 5 minutes drying time he rubbed on generous amounts of the finishing oil with a paper towel. The surface wax is removed leaving the grain elegantly highlighted with the embedded liming wax. To get all the surplus wax off requires folding the paper towel to a clean surface or using several clean paper towels. This approach delivers a highly pleasing finish, and the process is completed by applying at least two more coats of finishing oil on successive days.
Next up was a pot which was ebonised. Ebonising is a process in which a solution is made up by leaving steel wool in vinegar for a few days, and applied to the wood. The acetic acid solution reacts with the tannin in the wood and turns the wood black. Tannin bearing woods like oak are suited to this process. This pot was rubbed down with black patinating wax (instead of the liming wax), and when the finishing oil was rubbed on, it brought out the grain beautifully. Sand blasting first and then ebonising will create bolder black lines and further enhance the look.
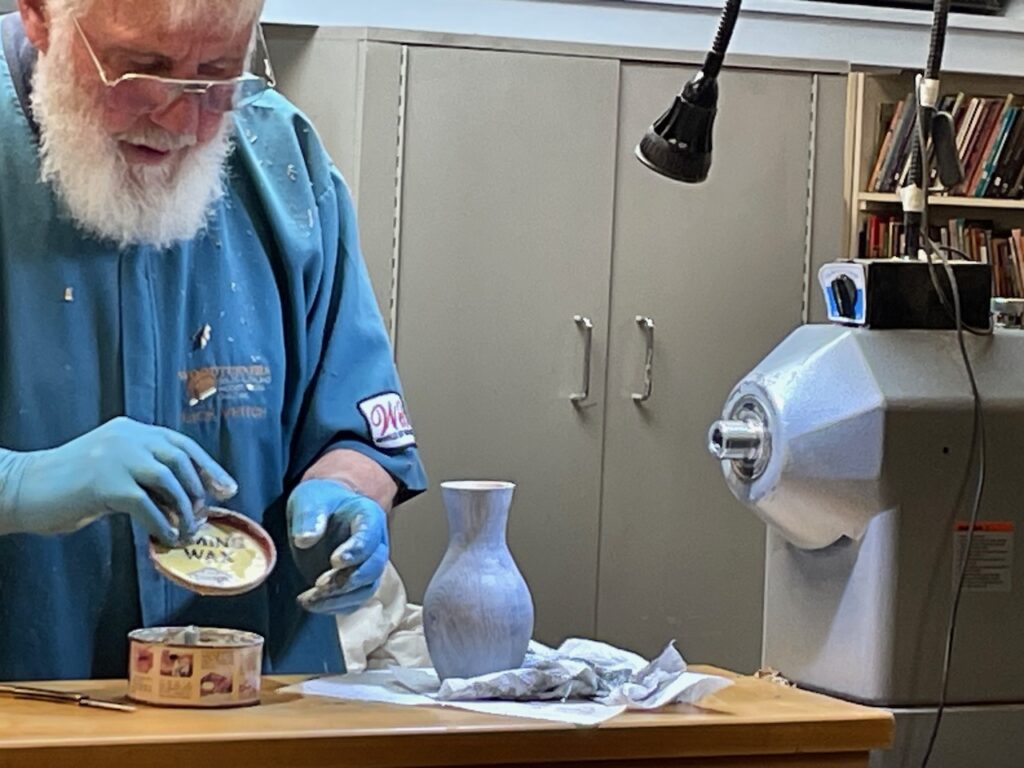
Some discussion took place around the effectiveness of using tea in the ebonising process. Dick’s conclusion is that tea contains tannin, and adding tannin to tannin has minimal effect.
Dick tried a pot with Artist black acrylic paint and white wax. This thicker viscosity of the paint tended to fill the grain more than Dick liked and was not quite so effective.
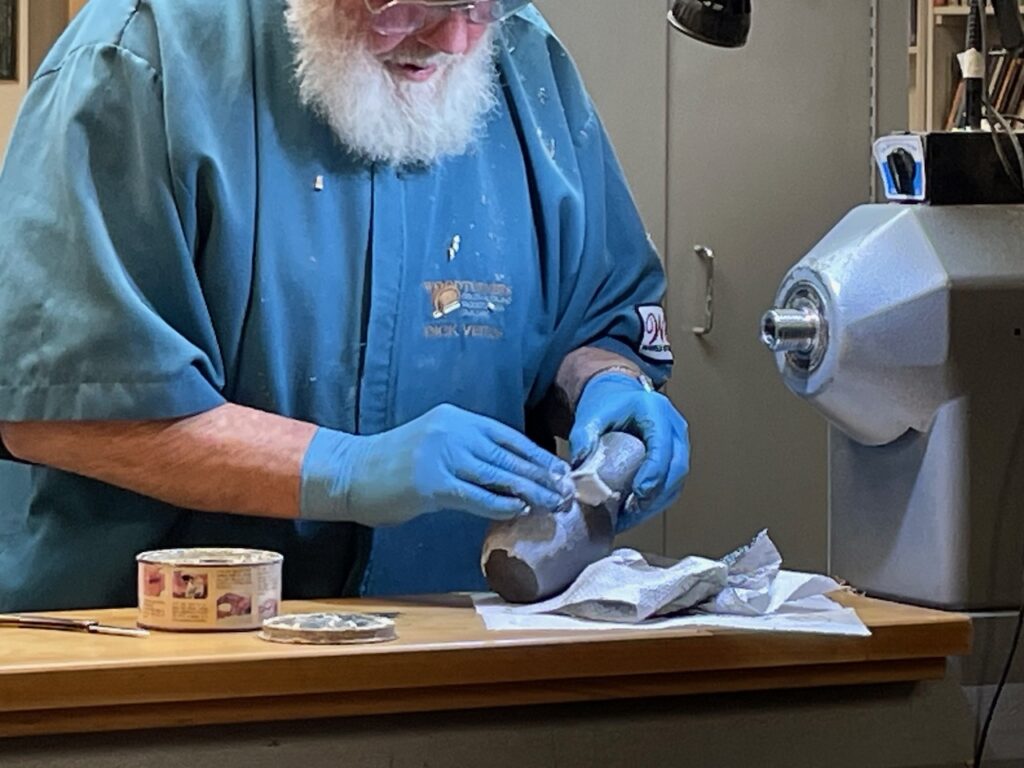
The next examples demonstrated the use of Dazzling Metallic acrylic paints by Deco Art. These are the pearlescent paints used so effectively by Robbie Graham in his work. The paints can be bought on line from Hobby Land, and come in a range of brilliant colours. Dick applied the black paint to a pot which was not sand blasted and the lines didn’t show up too well. Applying it to a sand blasted pot gave a better result. After the liming wax and finishing oil the pot still looked more grey than black, probably due to the pearlescence in the paint. Using the blue coloured Dazzling Metallic created a very beautiful wedgewood like effect.
Further methods for blackening included burning and fuming. Burning worked to a degree, but it was a little hard to control without over burning. Fuming is a process which Dick followed by popping a pot in a Sistema plastic container along with 4 little pots of cloudy ammonia cleaner. In Dick’s example the black was not very dramatic, but depending on the wood stronger effects can be achieved. Oak can also be darkened by using a baking soda solution.
Although Dick did not have examples of these, the audience mentioned the use of wire brushing and Kiwi black nugget for achieving grain highlight effects.
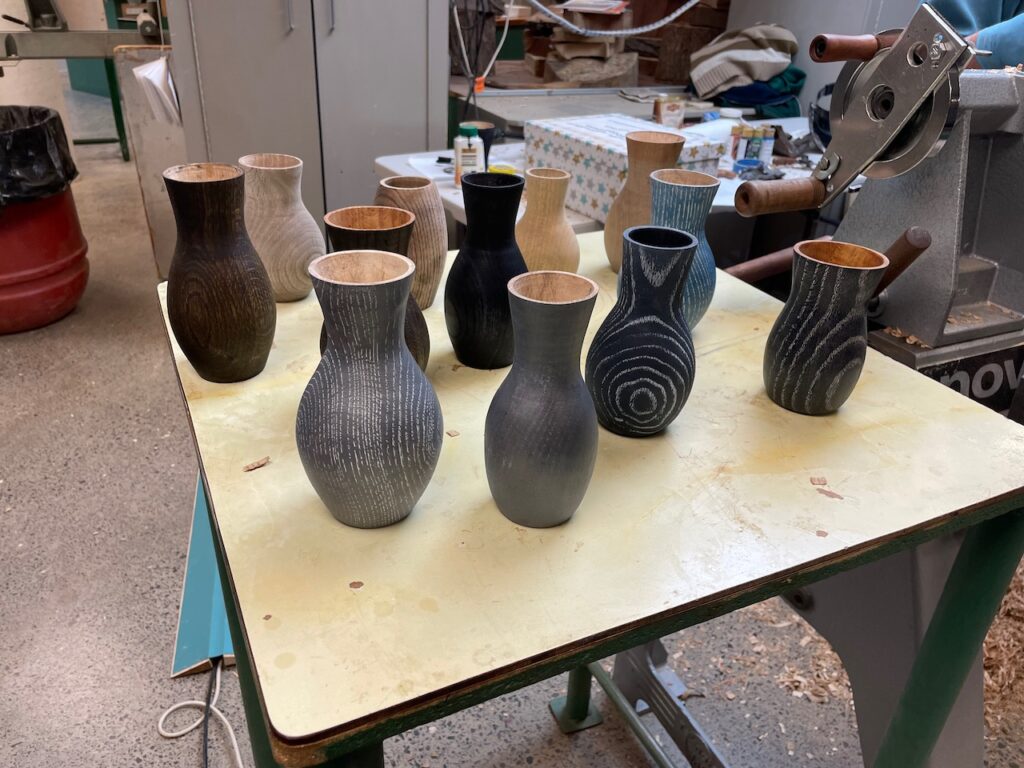
The demonstration illustrated the huge variety of finishing effects that can be achieved in simple and inexpensive ways, although Dick’s demonstration clearly showed that sand blasting as part of the process was a key ingredient for superior results. Preferred woods for grain highlighting are oak, cedar and ash.
Experimenting with different waxes, colours, processes etc can produce a wide range of results, so fill yer boots. I for one will definitely be buying some liming wax and probably the metallic paints.
Thanks a heap Dick, very enjoyable.