Club Meeting: 3 May 2023
Report by: Kieran FitzGerald
John began by explaining what he was going to make and showing us some examples of the finished product that he had previously made. In simple terms, the idea is to make a shallow but normal bowl, cut it in half, and from there you can enhance it in many ways including piercing, carving, colouring, inlays, by adding a stand, a lid, a finial, and in so doing creating an art sculpture. John showed us a slide show of some pretty serious pieces made I think mostly by American wood artists using this technique. Some of our club’s experienced turners were able to quickly recognise who had made a number of the pieces shown.
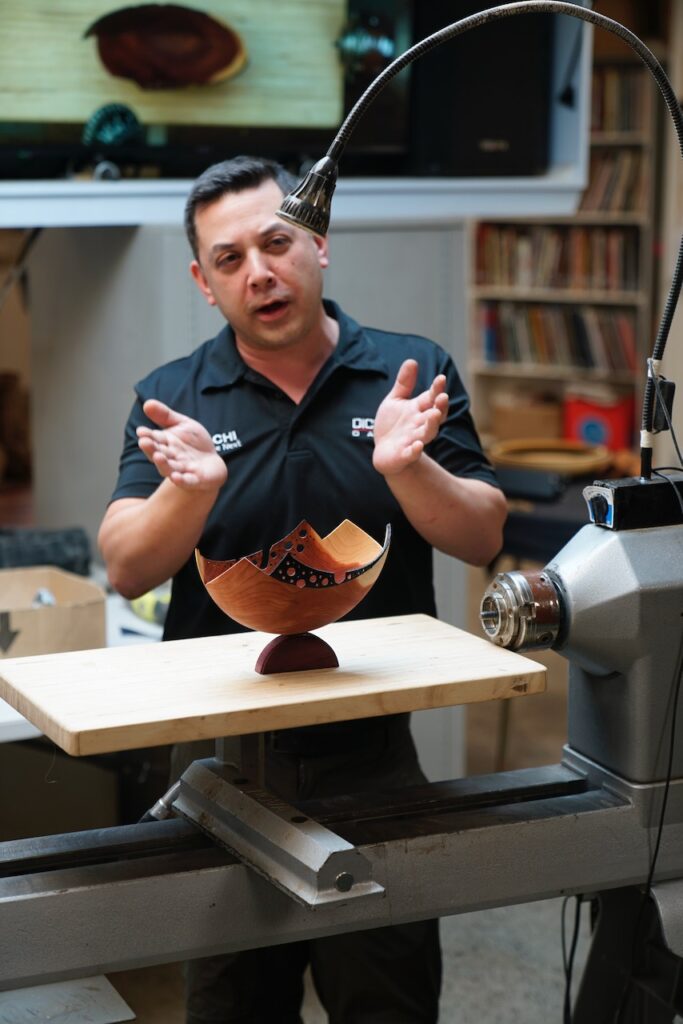
John accompanied the practical part of his demonstration with a clear, concise and satisfactorily detailed commentary which would easily enable all present to follow his example in their own workshops.
The blank you start with does not need to be huge, especially in depth, because the depth is doubled when the two halves are joined together at the end. In fact the symmetry achieved with a slim composition is very pleasing.
John began with a roundish blank about 200 x 40. Finding centre, he drilled a shallow hole to take a worm screw. He used a packer to take up some of the length of the worm screw before screwing on the blank. Mounting alternatives include using a faceplate with double sided tape or hot glue. Bringing up the tailstock for added security, John rounded the blank and made a spigot on the bottom. Procedure follows the normal bowl turning method, with some simple adaptations to ensure the joined halves have the desired end shape. These are that the bottom of the bowl should be cut fairly straight and flat, and the side near the top also needs to be straight and flat rather than coming to a point. This will create nice flat sides when the two halves are joined later on, and avoid a “v” shape at the join. John used a simple drawn template to give himself a visual reminder of the shape he needed to achieve on the outside of the turning. A shear scrape to remove any ridges left by the tool and minimise sanding followed, but in fact the final sanding was left til later when the bowl was in the cole jaws.
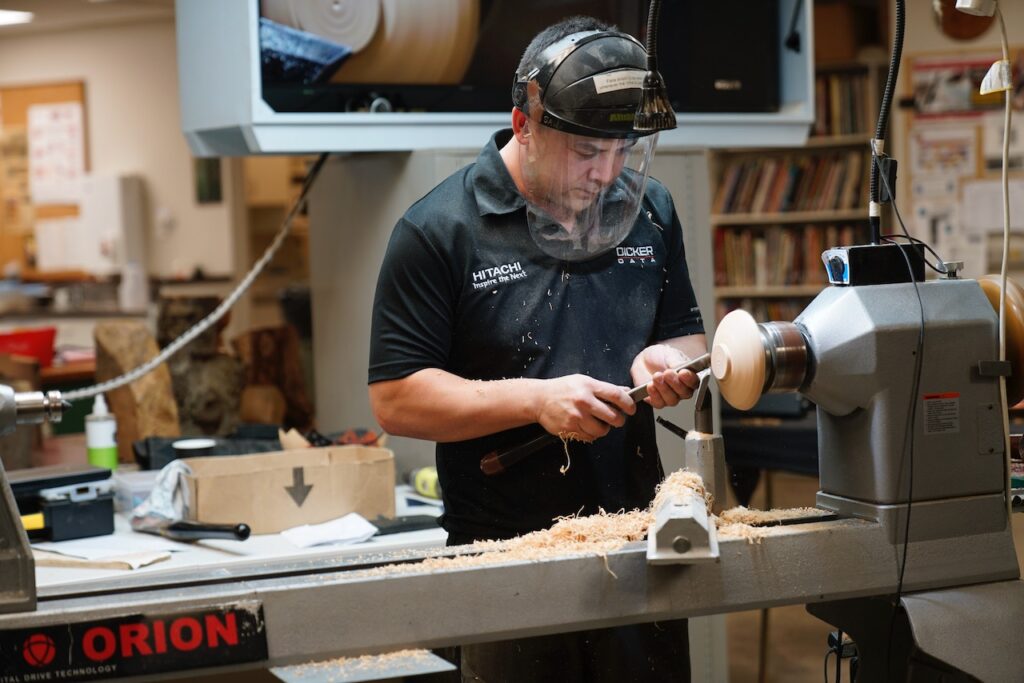
As per normal bowl process, John mounted the wood in the chuck using the spigot and commenced to face off and hollow. The inside shape needs to mimic the outside, with a flattish bottom. An even overall wall thickness is important because when the bowl is cut in half and joined the wall thickness of course is visible. John hollowed his to about 4mm, but thickness can vary depending on the look you are going for. The rim also needs to be perfectly flat to create a seamless glue joint, and John ensured this by sanding with a sandpaper faced board while the bowl was still turning on the lathe.
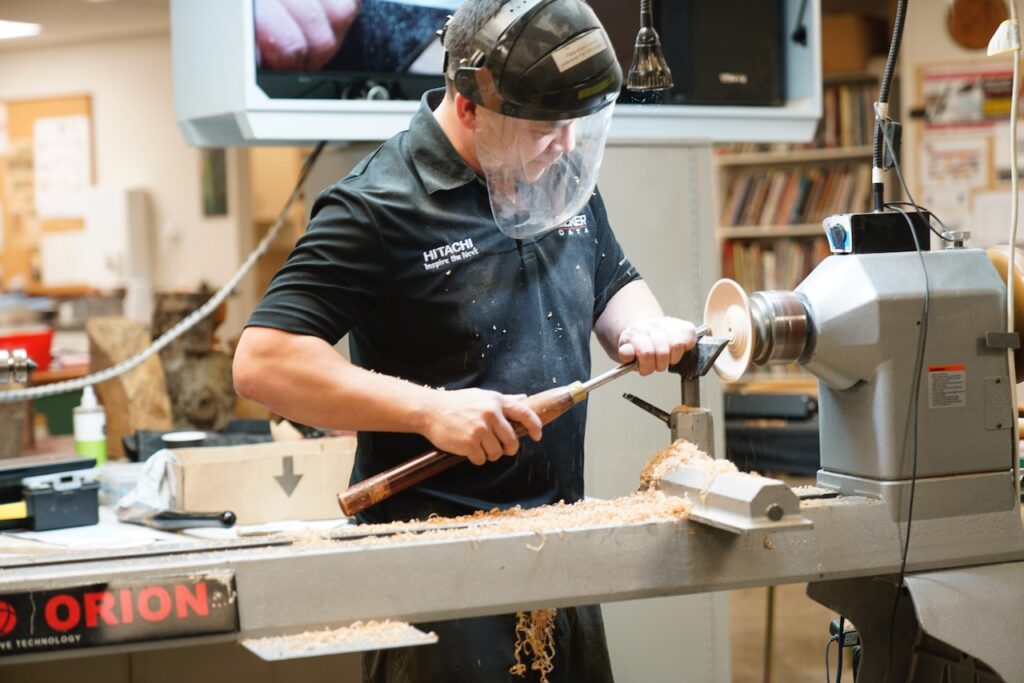
Taking the bowl from the lathe, the next step was to mount in cole jaws and remove the spigot. Give it a sand. John left the foot flat, then advised that this is a good time to add embellishments. He marked the centre to indicate where the halving cut will be made, and then scribed two circles about 30mm out from the centre, using a modified screwdriver. The idea of this is to cut a more square edged trench rather than a “v” shaped trench, because the latter diminishes in size with sanding. When the two halves are cut and joined the rings will appear as half circles on the mid top side of each half of the split bowl. John experimented filling the cuts with cayenne pepper and fixing with CA glue. As with a previous attempt using paprika, the plan was not totally successful, so perhaps revert to a tried and tested filler like copper powder.
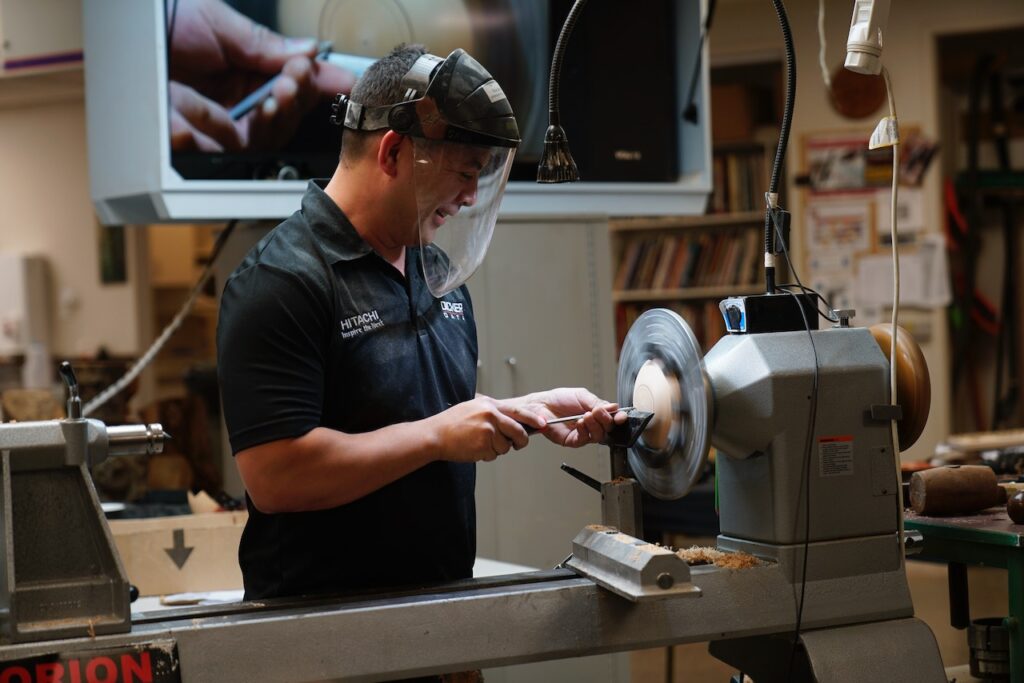
Use a flexible ruler laid across the centre mark to rule a line through which the cut will be made. When cut, hold the two halves together to check the join and sand a bit more if necessary. Glue it up; John uses pva, and hold it together with rubber bands. When selecting wood, and cutting into halves, be mindful of the grain pattern and what will look best. To achieve a different look, contrasting veneers may be laminated between the join. If a lid is to be made, a photocopy of the top of the bowl may be used as a template. The lid is rebated with a router. Further variety can be achieved at this time in the way the split bowl is mounted and the decoration that is applied to the bowl.
Thank you John for an enjoyable, instructive and well planned demo.