Club Meeting: 8 May 2019
Report By: John Whitmore
The intention was to both inform members and to preserve the Guild’s tools. Consistent sharpening of SAWG tools makes it easier for new turners to move between work stations and the tools last longer. Instruction is available for using the sharpening station.
Tools can be sharpened on either an abrasive wheel or on a flat abrasive surface such as a disc or linisher (a belt sander in disguise). Whilst all have their merits, the basic difference is that wheels produce a concave bevel and discs/linishers give a flat bevel. Honing was not part of this presentation but could usefully be incorporated in a later demonstration.
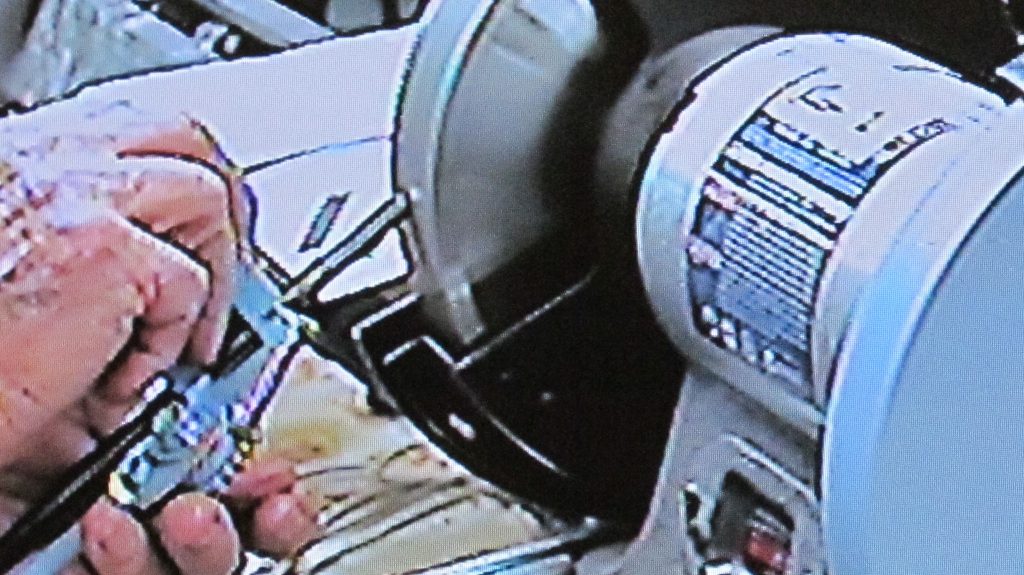
The usual form of abrasive wheel sharpening is via a double-ended grinder having wheels of 150mm (6”) or 200mm (8”) diameter, the larger size being preferable but more expensive. More specialised machines are available including several brands with larger 250mm (10”) wheels running in a water bath and slower speed grinders intended to reduce the generation of heat.
Ordinary ‘workshop’ grinders are usually supplied with (grey) carborundum wheels of low quality. Internationally, there is a variety of different coloured grinding wheels purporting to serve different purposes but the ideal approach is to have a cubic boron nitride (CBN) wheel for high speed steel (HSS) tools at one end, plus an aluminium oxide wheel (white) for other ferrous materials, at the other end. Both are readily available in NZ.
The use of a 300mm disc sander for sharpening was developed in-house and with a jig for each tool, enables a quick ‘polish’ rather than serious grinding to replenish an edge. The linisher is a much more expensive product by Robert Sorby having a useful variety of easily interchangeable belts and reliable jig settings for repeatability. Whereas all grinding wheels (except the CBN) gradually reduce in diameter, the disc and belt abrasive surfaces remain consistently flat.
Other useful points arising were:
- Recommended bevel angles for Guild tools are bowl gouges of 35 and 55 degrees, spindle gouges 30, spindle roughing gouges 45, parting chisels 30, skew chisels 30.
- Wheels, disc and linisher abrasives have different grits (or roughness) and hardness.
- Don’t dip HSS tools in cooling water as the temper will be ruined. Tool steel is OK for cooling.
- Always use a jig to achieve a single, smooth, and symmetrical bevel. This doesn’t work well for negative rake scrapers or if an asymmetrical bevel is wanted – the latter usually by professionals freehand sharpening.
- Putting a diamond-section parting tool sideways into the Guild’s Truegrind tool holder enables both bevels to be sharpened without any repositioning.
- A diamond dresser is available for cleaning dirt and glaze off all sintered (cooked in an oven) wheels. A CBN wheel is never dressed.
- Sintered wheels can shatter so always use them with guards in place.
- Do not sharpen on the side of a wheel unless specifically labelled as a side-cutting wheel.
- A 55 degree bowl gouge is useful across the inside bottom of bowls when a more ‘pointy’ 35 degree grind may result in a gouge shaft hitting the bowl rim.
- Sharpening a pencil is a good analogy to explain ‘cutting with the grain’.
- A plug was also given for using sharp sandpaper.
Alongside the theory, sharpening using Guild jigs and tools was demonstrated with some bowl shaping. The presentation was accompanied by excellent visual aids and invasive music from next door. Despite the music, a good time was had by all and clear information was received during a well-structured performance.