By Dick Veitch
Despite marbling being a craft practised since the 12th century we still don’t have a precise recipe on how to do it. It has, however, been part of the NAW National Certificate in Woodturning since its inception. In the training books we find a recipe that works – but, it seems, not well enough for many to use marbling as a frequent enhancement of their woodturning.
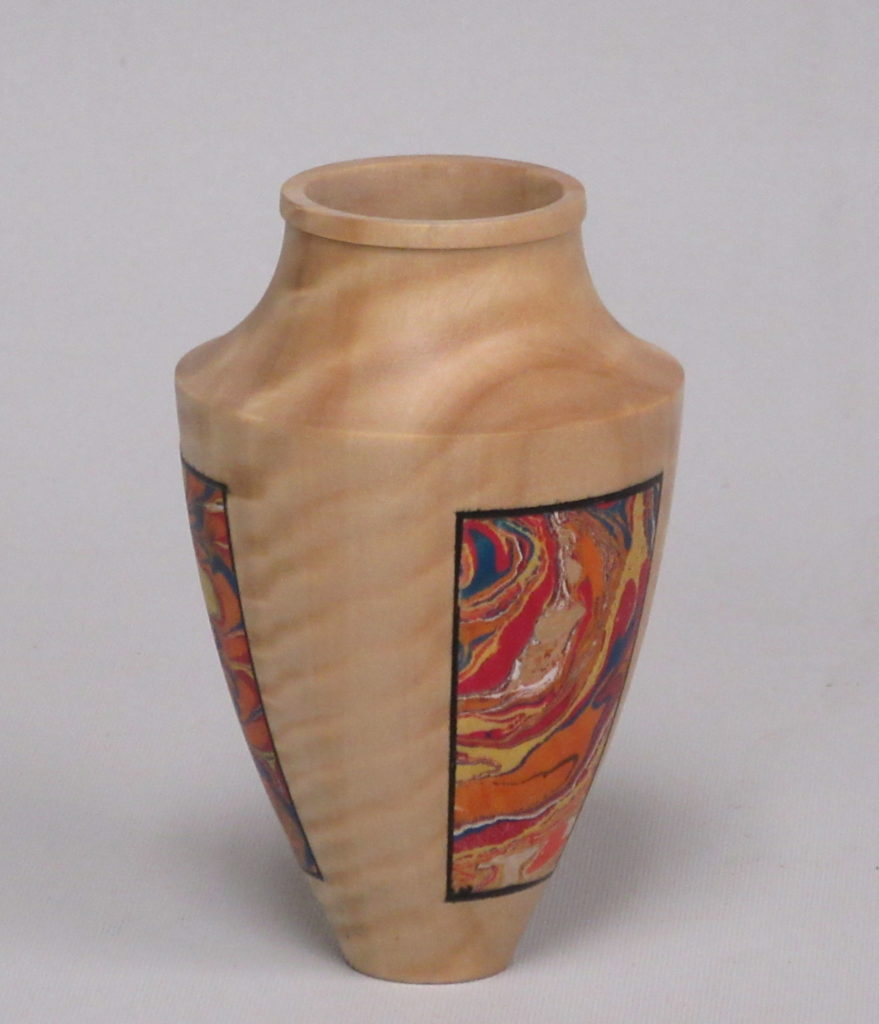
When Walter Wager, from near Tallahassee, offered us a marbling demo I was a bit ho-hum. He included a copy of his marbling report to the American Woodturner journal. Nice pictures, nice work, and yet another recipe requiring the mixing of spoonsful of this with quarts of that to make up gallons – probably US gallons. There also was a statement about “pure” this and using distilled water. A little web search established that I could buy distilled water in the supermarket and I could order in pure methylcellulose and pure alum.
That suggestion of not using our chemical-laden town water and not using wallpaper paste (methylcellulose with unknown additives) made great sense. Please do visit us, Walter.
To prepare for his visit I worked my way through many recipes to make up an alum solution and the methylcellulose size needed to float the acrylic paint needed to create the marbled effects.
Now, bear in mind that there are marbling kits available in some New Zealand stores and online – they all work, but most are designed for one-person use. We were going to have ten, or more, people wanting to put marbling on their choice of wood. The National Certificate in Woodturning also needs to cater for more than the single user. So, getting information on the important ingredients is necessary.
The important wood preparation is firstly to choose a dense white wood, turn it, sand it, and apply alum to the wood – just keep the items small please? That meant that most arrived with eggs, egg cups, a wig stand foot and little bowls but, as always, one had to arrive with an item that challenged our biggest dipping dish!
Any acrylic art paint is supposed to work – true, most do – but, as a rule, the cheaper the paint the coarser the granules within the paint.
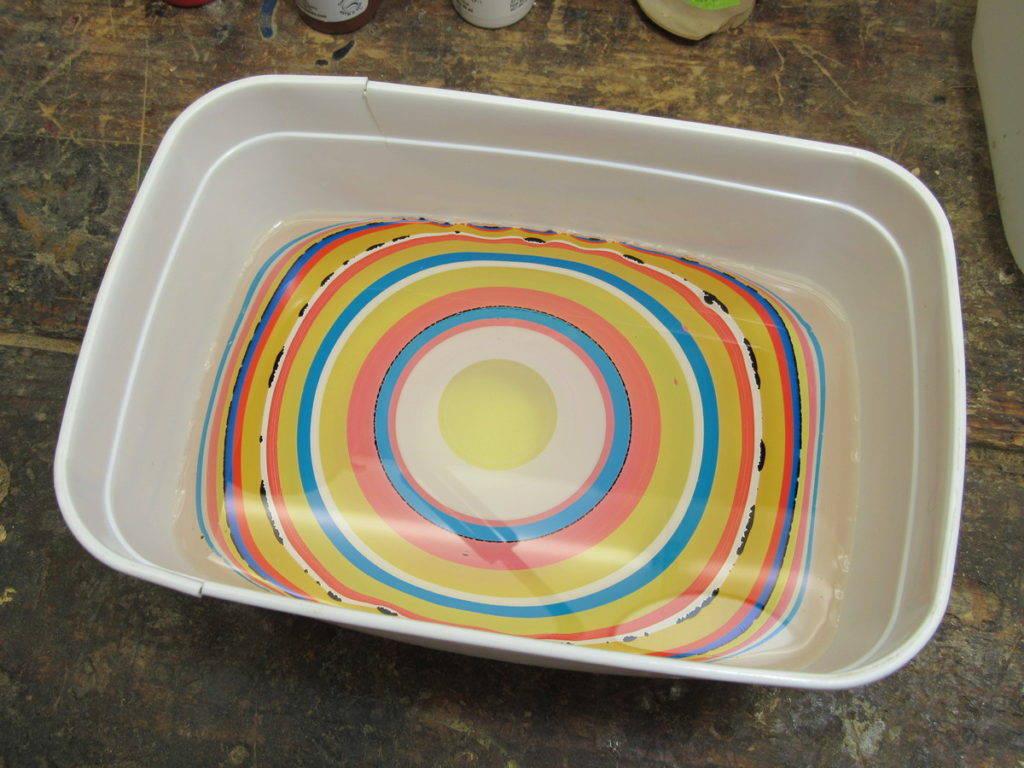
Next challenge is to get a nice pattern of paint floating on the surface of the methylcellulose size mixture. Amongst the crowd at Walter’s hands-on afternoon we had some fairly basic acrylics, tubes of quality colours and some of the Golden High Flow Acrylic mentioned above. Most of those had to be thinned with water (or, later, more paint added) so that the paint would float on the surface of the size. Some spread more readily than others. Some colours of the same brand spread well when used alone but then either would not spread when placed over other colours or would spread madly and push everything aside.
Our choice now is Golden High Flow Acrylic. Ok, appears to not be cheap but only a few drops are needed for each marbling action. This paint has a fine and consistent texture and is available in more than 50 colours.
Obviously, putting drops of colour sequentially at the centre of a bowl results in rings of colour. You can have these rings of colour on your wood or take a comb and stir it a little. Then dip the wood in. Rinse it off and let it dry. When thoroughly dry put a finish over it.
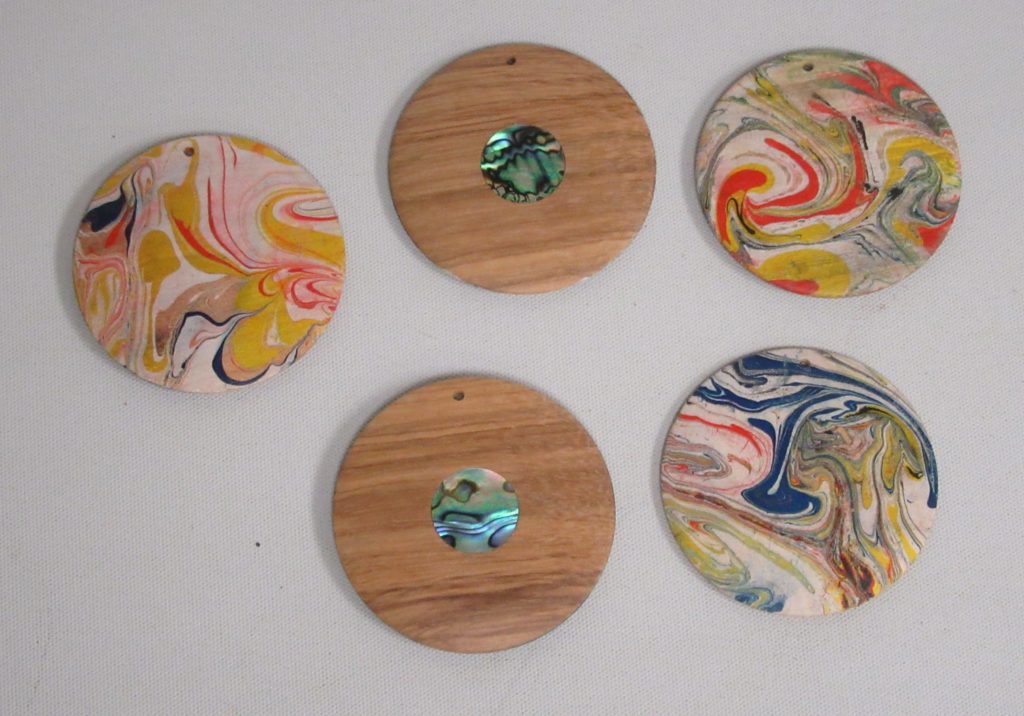
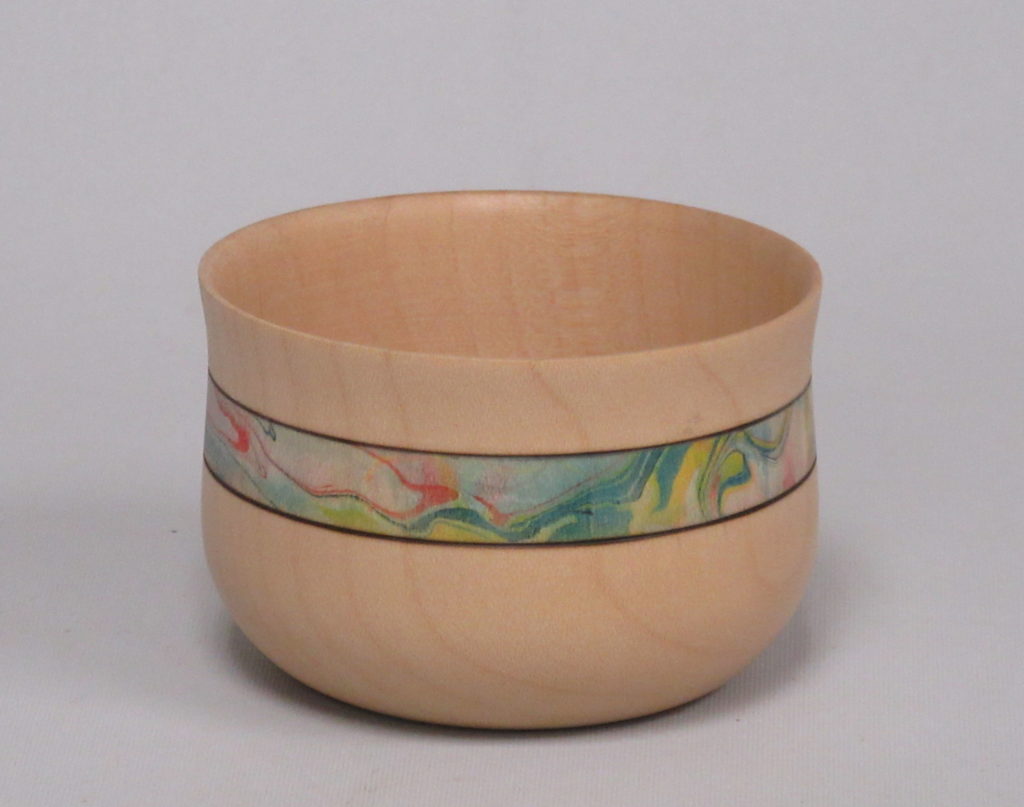
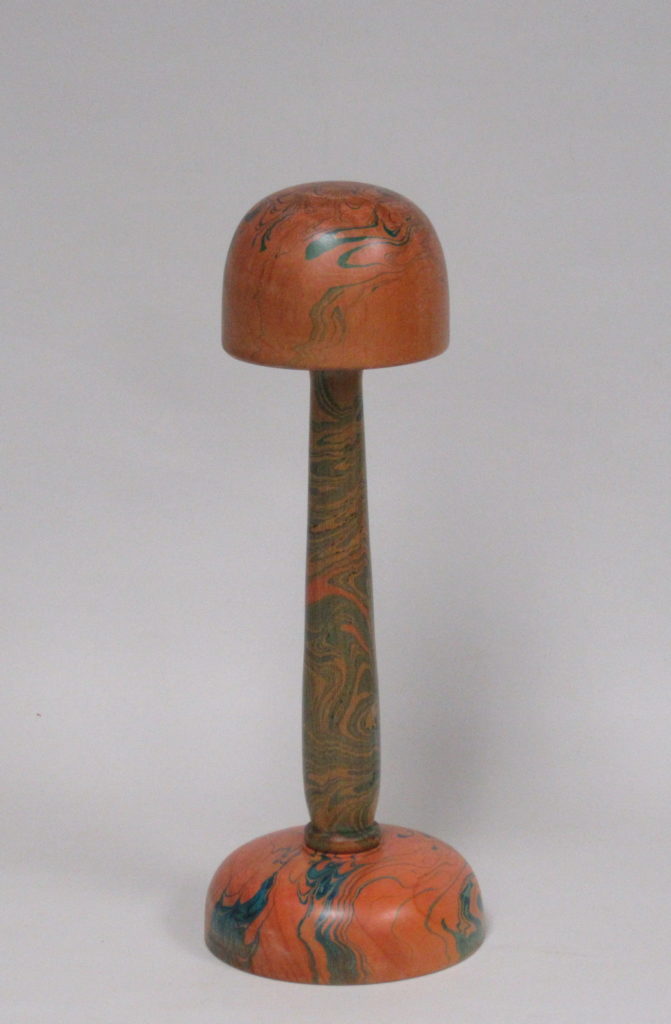