Club Meeting: 5 Feb 2025
Report by: Peter Wyatt
Strett discussed the use of ‘JAM CHUCKS’ to allow turning in situations outside the normal lathe chucks.
Theoretically there could be jam chuck for all situation.
Small Bowl Chuck
This can be used to remove spigots and finish the bottom of the bowl. The jam chuck does need to completely fill the bowl tightly with the tail stock needed to centre the bowl and hold it in place.
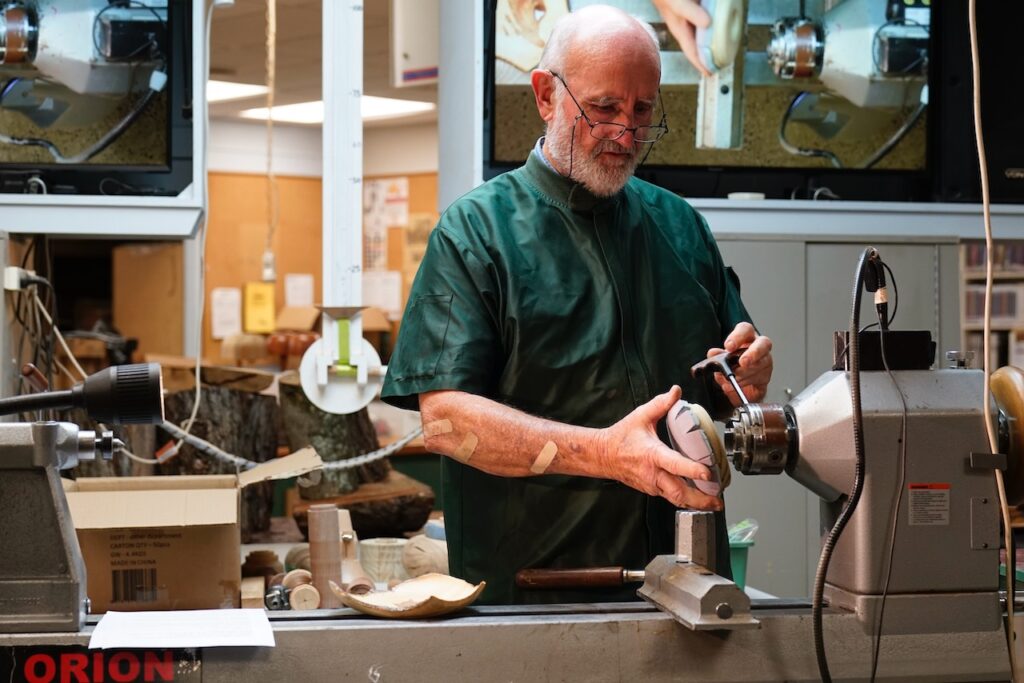
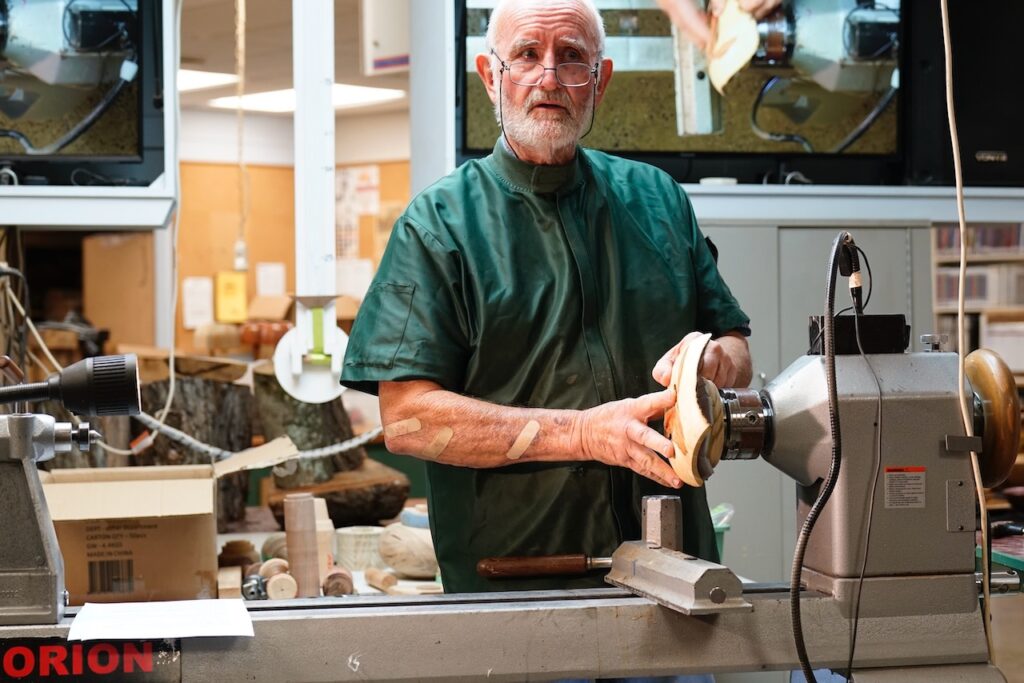
Larger Bowls
The same situation as small bowl
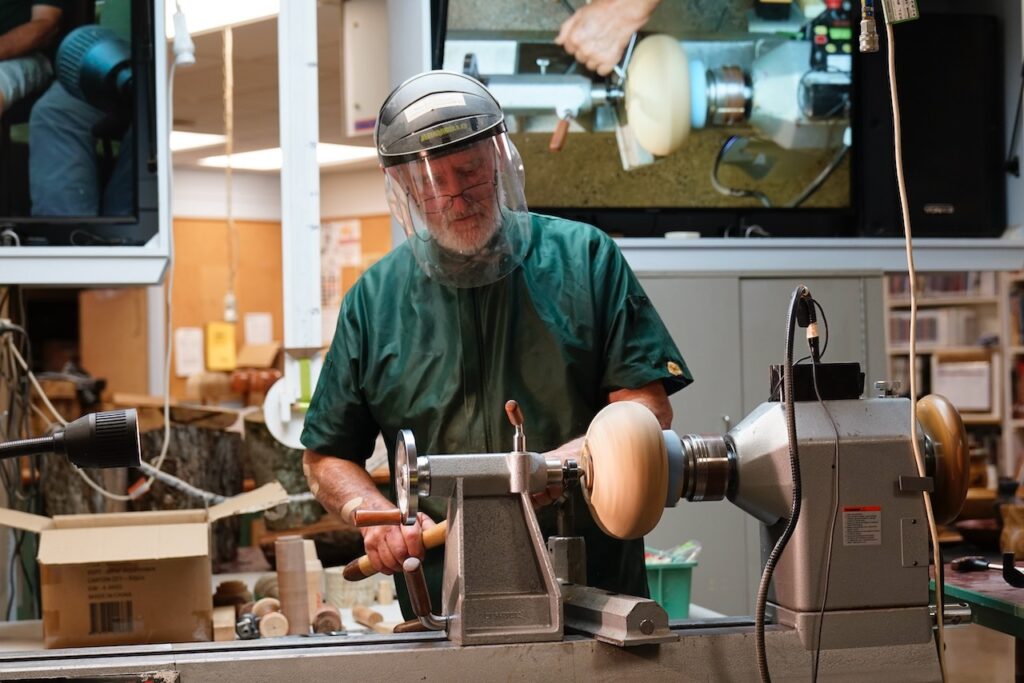
Internal Pointed Chuck
This chuck is cone shape with rubber around it and will go into hollowed out bowls, as in the photo. The tail stock must again be used to hold and centre the bowl.
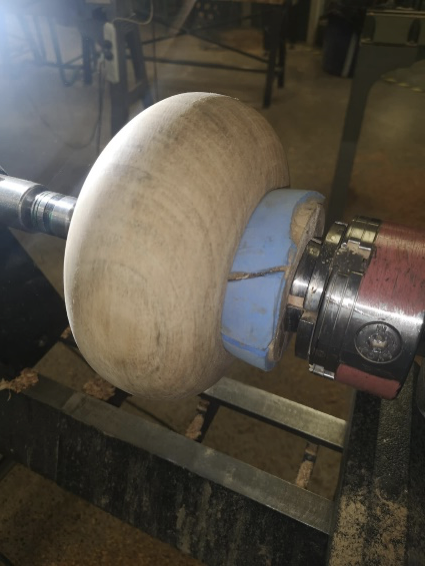
Oyster Catcher
This chuck is made with spigots at both ends It is round with holes in each end to suit the item to be placed inside. The holes will need to reduce in size to take the shapes to go in. Strett uses this chuck to make his Oyster catcher, as you can see in the photos
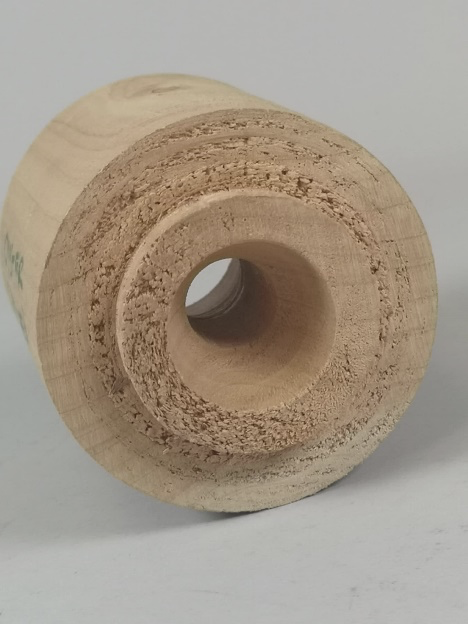
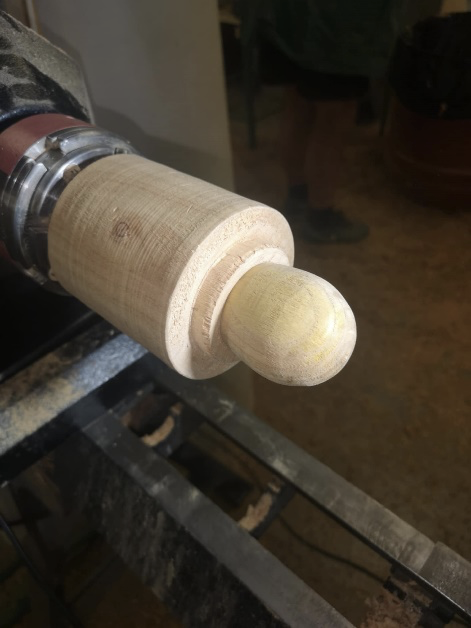
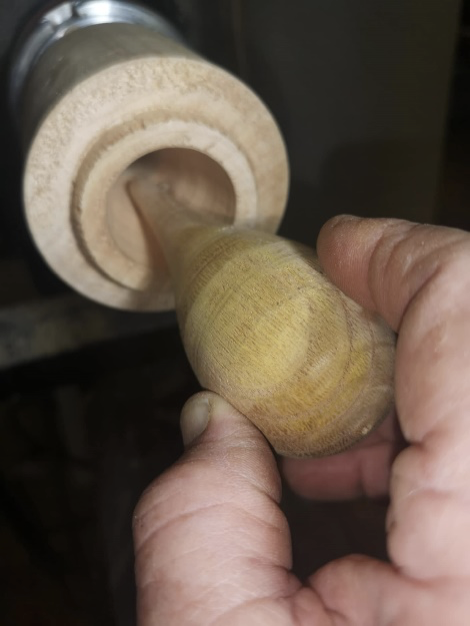
Glue Chuck
Glue chucks can be used to support small to very large items for turning. They can have spigots for attaching to the lathe or a threaded piece to screw the board to the lathe. The items to be turned are held in place by the tail stock and then glued to the supporting timber plate. This chuck is used in off centre turning, and for small items such as Deer antler buttons
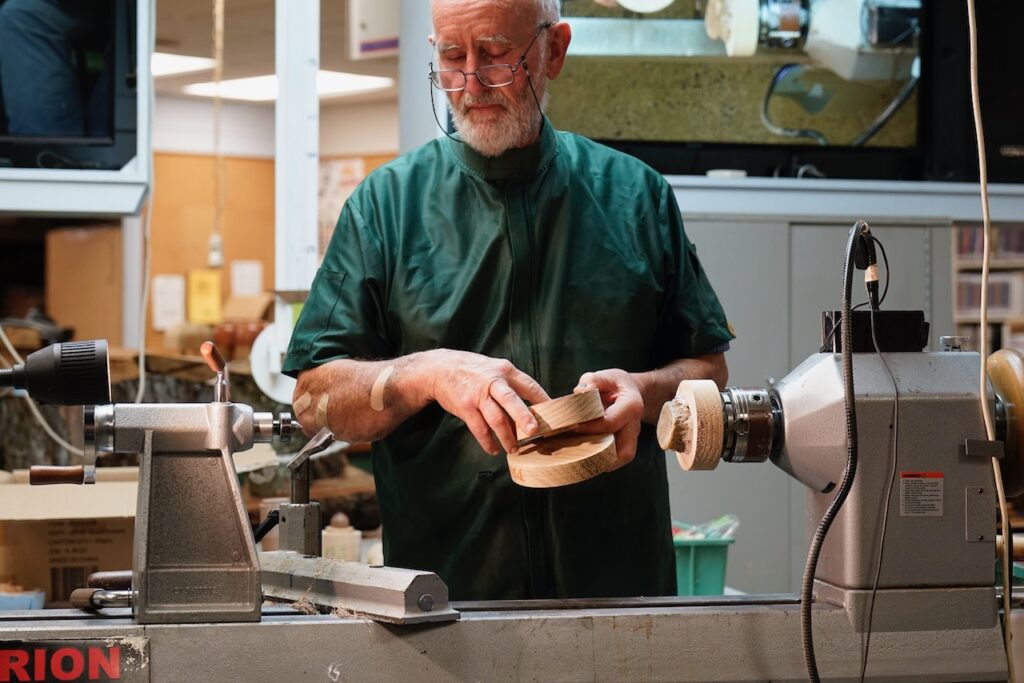
Dowel Work and Finials
Strett showed us a jam chuck, in the photos, that can be used for turning dowel. The dowel is griped by the 4 piece plug that can be seen. Once centred by the tail stock it is tightened by pushing the plug in. The hole in the chuck goes right through to allow a length of dowel to go in.
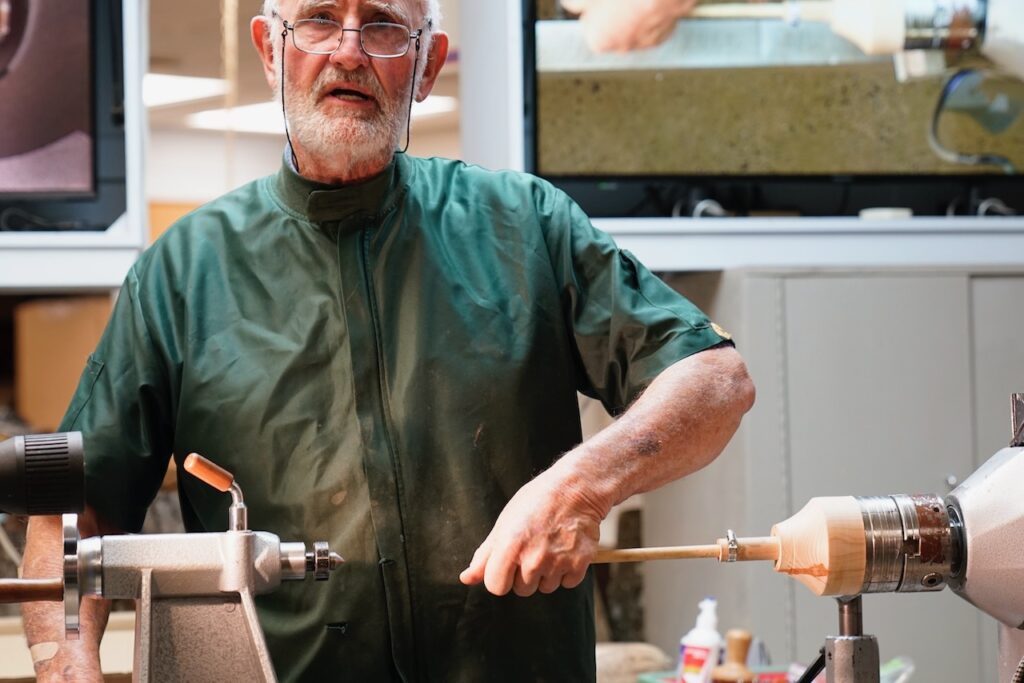
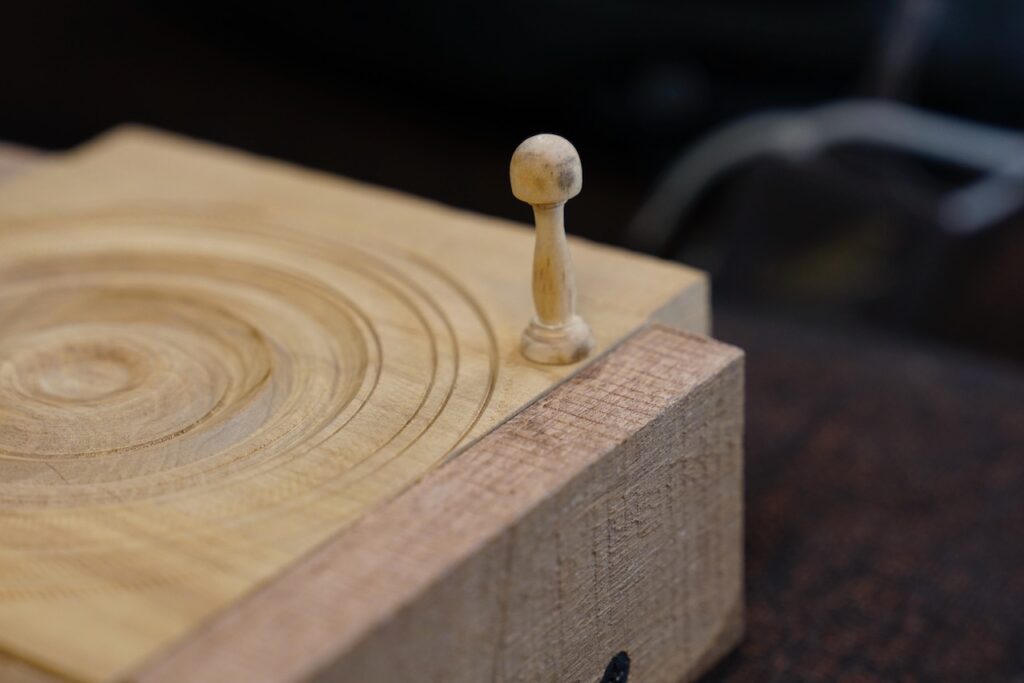
Strett stressed that jam chucks are limitless, and he advised that he only showed a few to show what can be done.
He mentioned:
Box spigots, Pencil repair kits, All off centre turning, and all dowel and finial work.
“Keep all left over ends, and pieces as they will come in handy one day”
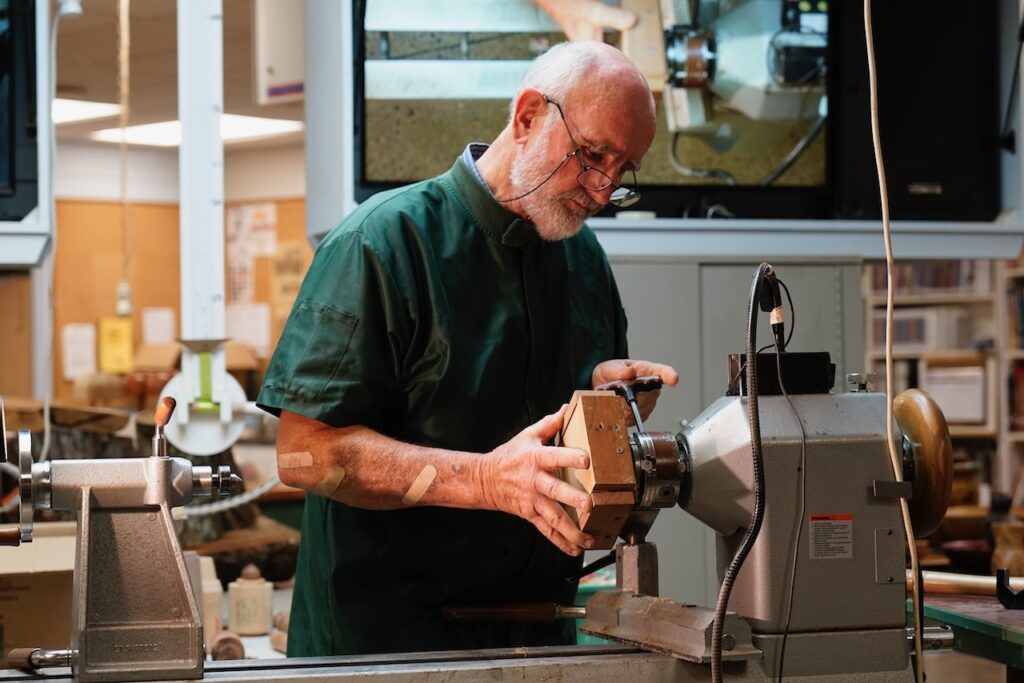