Club Meeting: 13th November 2024
Report by: Rebecca Waite
Julie, a member of the North Shore Woodturners Guild, brings over 20 years of experience in woodturning and has mastered a variety of techniques. In tonight’s demonstration, she introduced the members to the traditional Shou Sugi Ban, also known as Yakisugi. This classic Japanese method involves charring the surface of cedar cladding to preserve the wood. By burning the wood, a protective layer of carbonized material is created, significantly enhancing its durability and resistance to the harsh elements of the Japanese climate.
The process typically involves the following steps:
- Charring: The wood is exposed to flame until the outer layer is charred. The level of charring can vary depending on the desired effect.
- Cooling: After charring, the wood is allowed to cool. This can sometimes involve wetting the wood with water.
- Cleaning: The charred surface is brushed to remove loose ash and reveal the textured surface beneath.
- Finishing: Often, the wood is treated with oils or sealants to enhance its appearance and further protect it.
Julie shared stunning examples of her work with this technique, and my favourite was her coffee canister. The Shou Sugi Ban method is particularly effective for items designed for heavy use.
Julie arrived well-prepared, bringing two half-turned bowls, each featuring spigots at both the top and bottom. The bowls were finished on the outside, and sanded to a smooth 240 grit, ensuring that there was no tear-outs, which would be noticeable after the charring process.
Additionally, she created a burn line on the rim of the bowls using Formica because she wanted a crisp definition between the burnt wood and the unburnt wood
Safety
Julie does the charring process outside with a bucket of water handy as her workshop has a lot of dust. Wear a safety shield/glasses, and also have a spray water bottle, Fire extinguisher, and fire blanket on hand.
To achieve this you will need a blow torch.
Julie uses a canister from bunnings
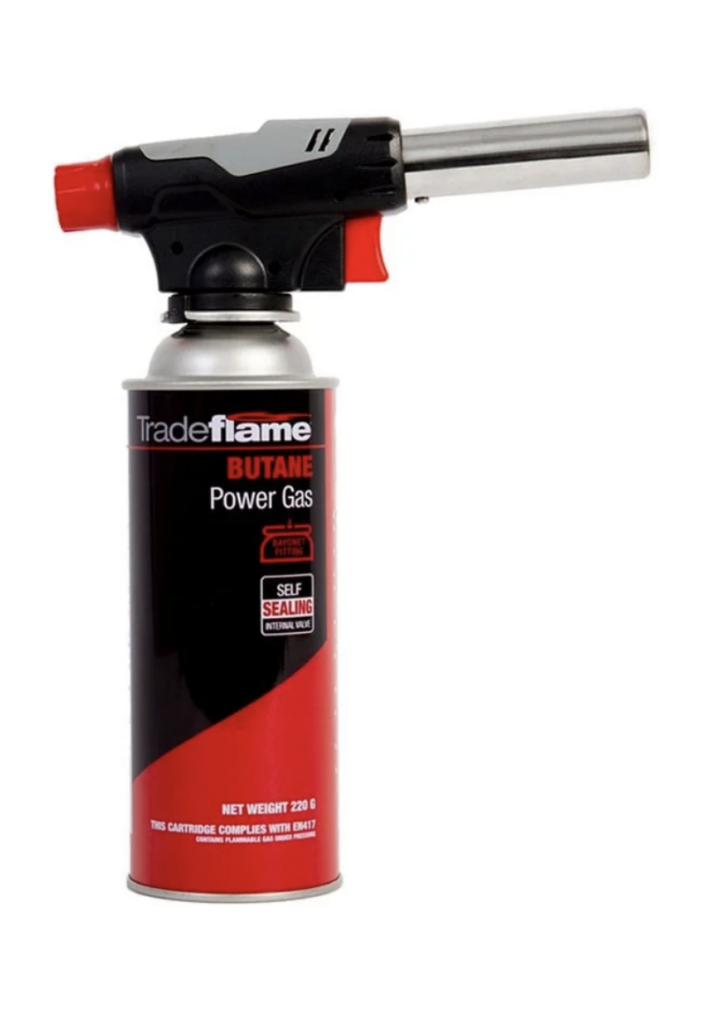
A brass brush – make sure it is brass and not steel coated in brass as it won’t be soft enough
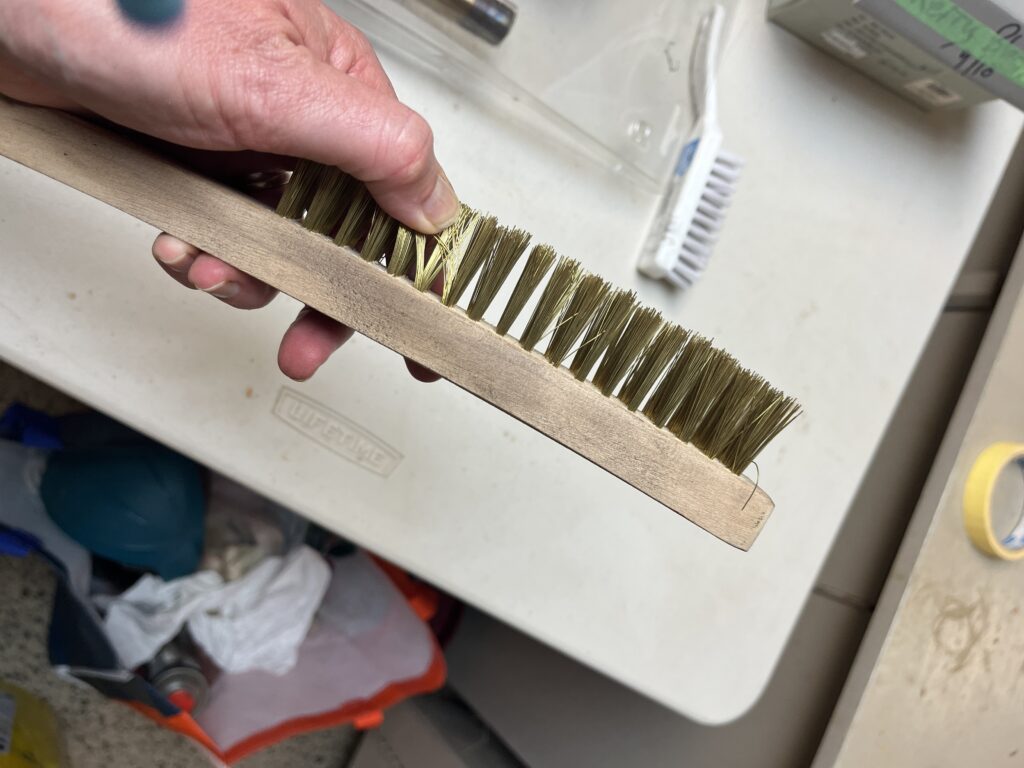
Julie’s first example was a Paulownia bowl, which she charred heavily.
She held it in a chuck on the tool rest, then hand-turned it and charred the bottom then the top. After brushing it, she charred it again and brushed it once more. Once she achieved her desired look, she turned the inside of the bowl, cutting just past the burn line at the rim. It’s important to make a clean cut for the rim before removing the top spigot.

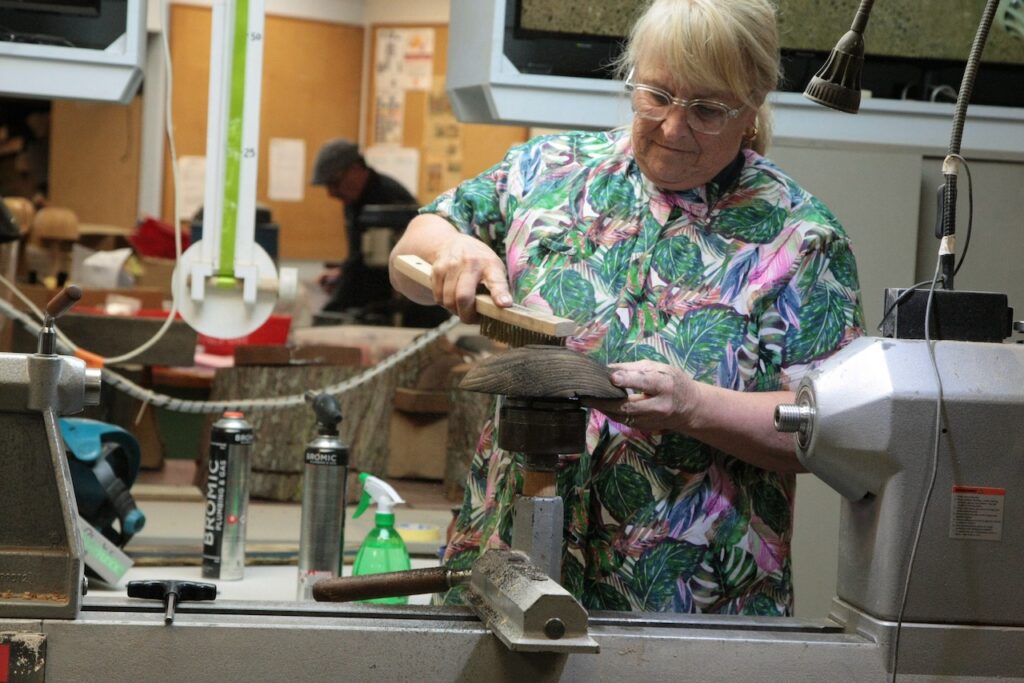
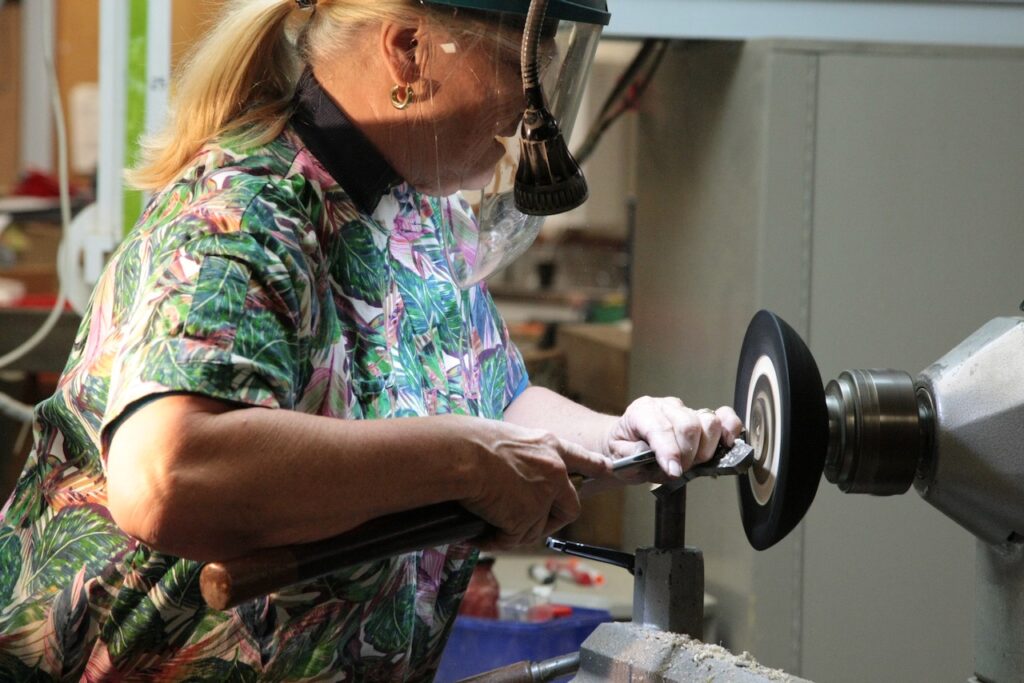
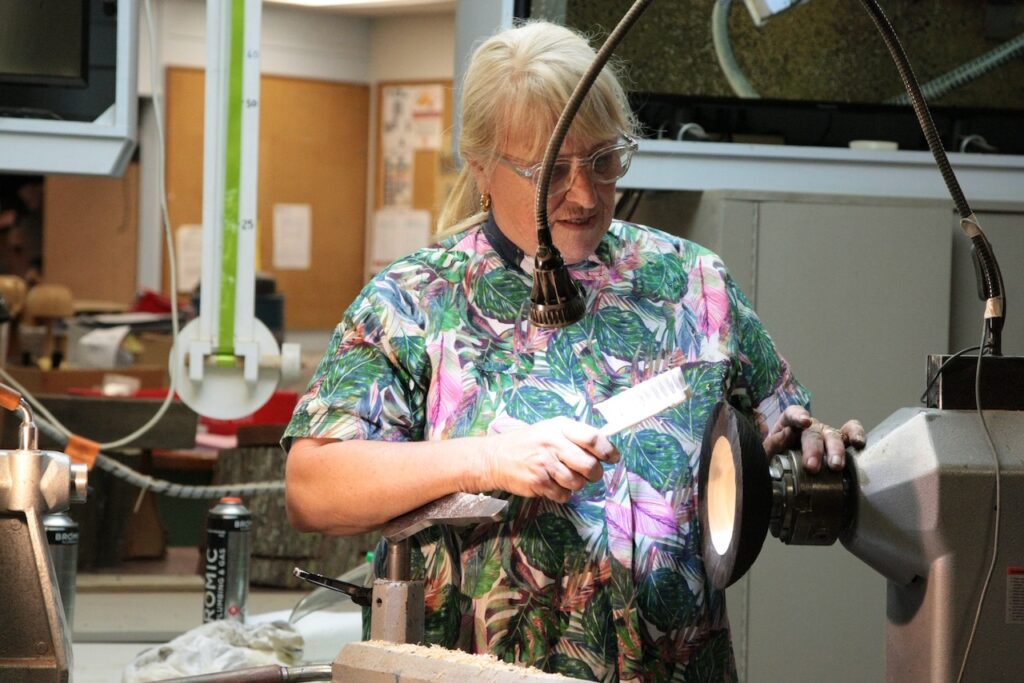
Sand carefully to avoid scuffing the finished rim.
Julie’s second bowl was a small oak bowl, which she lightly charred without brushing. She then painted it with Red Briwax colourfast spirit-based wood dye. If you use a spirit-based colour, be sure to apply a water-based finish; using a spirit-based finish could risk removing the colour.
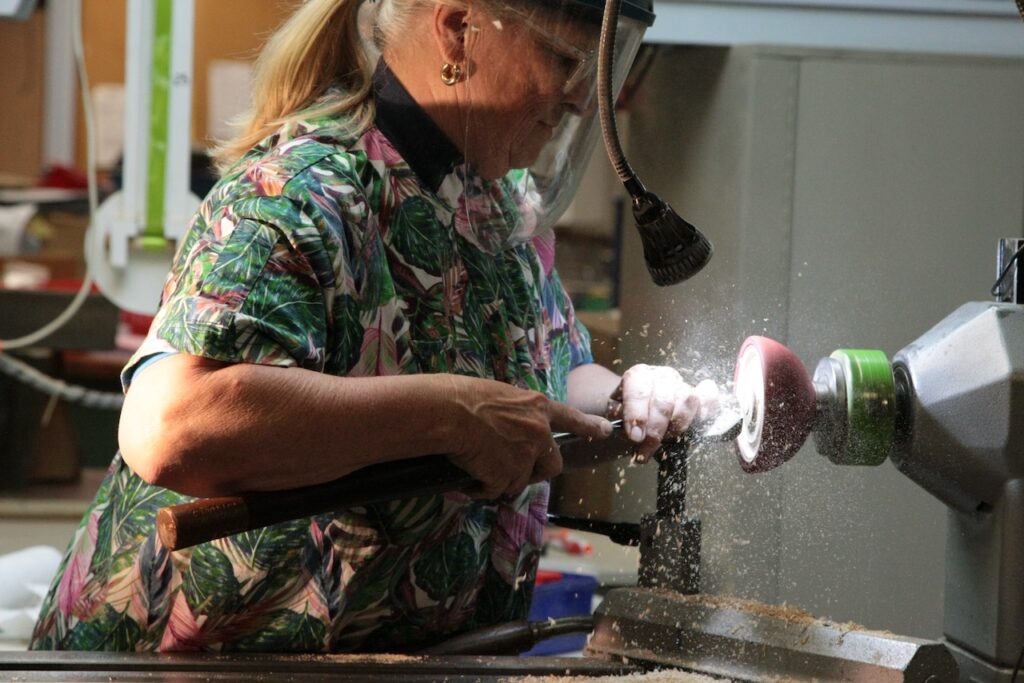
With oak being a hardwood, you can turn the bowl thin without leaving a “chicken bottom”—a term Julie used to describe a thick bottom due to being too chicken cutting deeper. Once your bowl is finished, let it sit for a day before applying a final finish.
Some helpful information from Woodworking Magazine when thinking about using this technique
Wood types suitable for this treatment
Non-porous or Softwoods lack vessel cells, as water is conducted through tracheid cells in the living tree. Various softwoods exhibit distinct growth-ring patterns. For instance, white pine has non-distinct rings with relatively uniform stain absorption, similar to diffuse-porous woods. In contrast, yellow pine features clearly defined rings, with more noticeable stain uptake in the earlywood compared to the latewood, resembling ring-porous woods. Examples include cedar, pine, spruce, redwood, and Julie’s favourite, Paulownia.
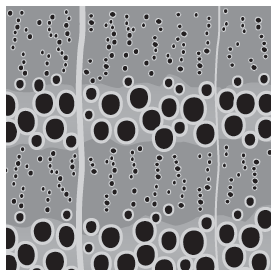
Ring-porous woods are hardwoods recognised by a unique growth pattern in their wood structure. In these woods, larger and more abundant pores are present during the early growth season (spring), while in the later growth season (summer and fall), the pores become smaller and more closely packed. This creates a clearly identifiable annual growth ring. As a result, these woods typically exhibit a coarse texture due to the size of their pores. – Oaks, Ash, Chestnut, Black Locust, Honey Locust, Elms, Pecan, Ban Tree, Hickory
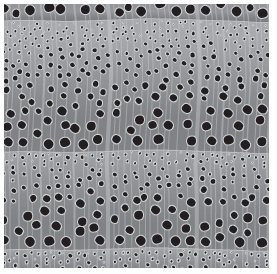
Semi-Ring Porous Wood: This type of wood features a mix of both ring-porous and diffuse-porous characteristics. In semi-ring porous wood, the early wood (spring growth) has larger pores, while the late wood (summer growth) has smaller, more densely packed pores. This structure allows for a balance between strength and moisture management. Common examples include some species of oak and ash, Black walnut, black cherry
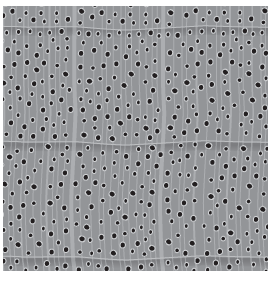
Diffuse Porous: In certain species, such as maple, cherry, and yellow poplar, the pores are fairly evenly distributed throughout both the earlywood and latewood. While most domestic diffuse-porous woods feature relatively small-diameter pores, some tropical varieties, like mahogany, possess larger pores. These woods typically exhibit uniform stain absorption, They are commonly referred to as closed-grain woods. Examples are American beech, birches, maples, American sycamore, sweet gum, sour gum, aspens, willows, dogwoods, tulip-poplar, basswood, red alder, sugar maple, yellow birch, and yellow poplar
Illustrations above by Mary Jane Favorite, based on photographs from R. Bruce Hoadley’s “Understanding Wood”
Julies garden Sculptures using this treatment
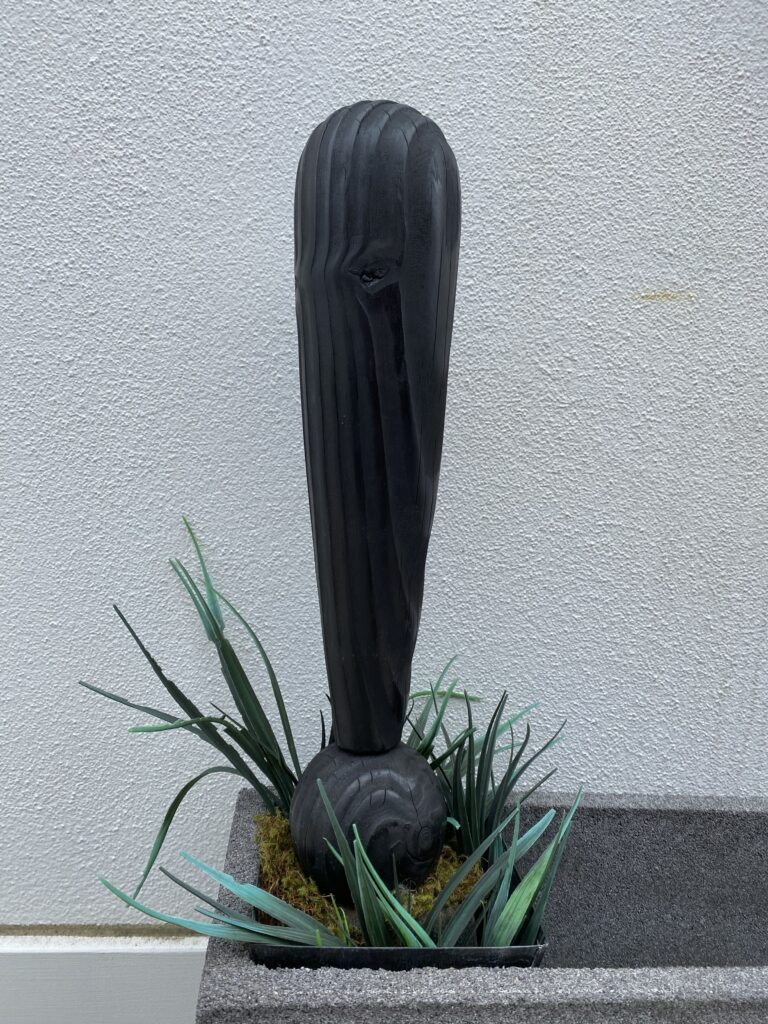
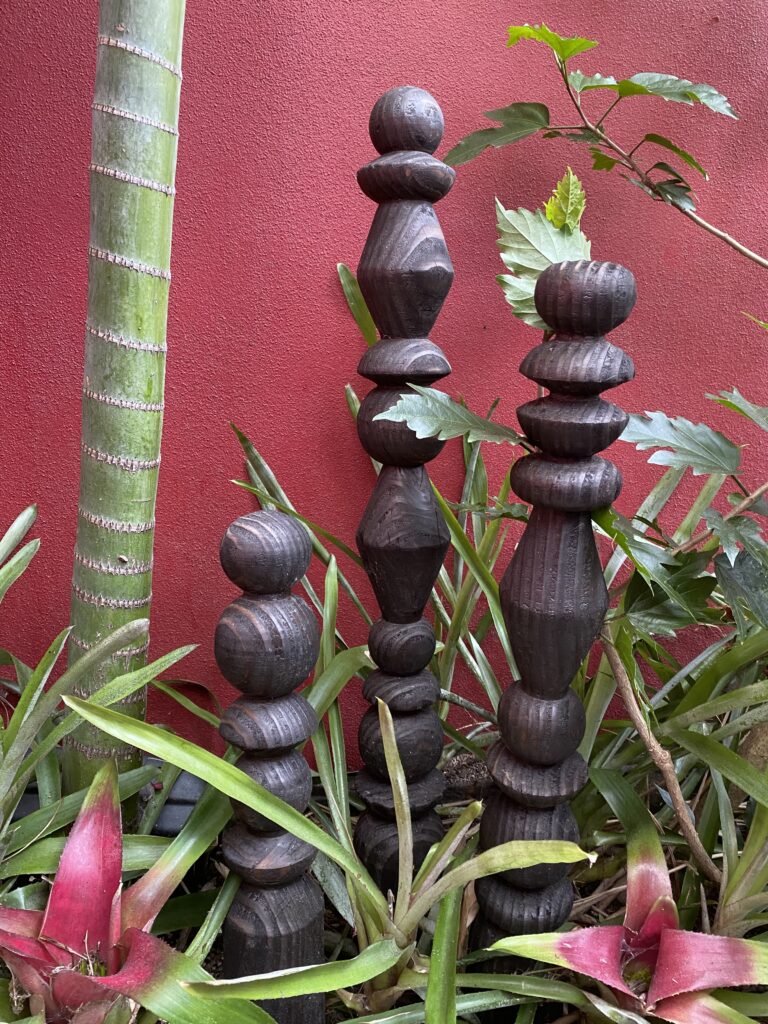
Factors Julie considers when using this technique:
Planning: Carefully plan the sequence of tasks since sanding cannot be performed after charring. Ensuring all shaping and detailing are completed before applying heat to achieve the desired finish without the option to go back.
A massive thank you to Julie for a fantastic, entertaining and informative demonstration. If you would like to get hold of Julie, you can contact her via email at julie@gannaway.nz
Julie mentioned other techniques like sandblasting your piece, examples and inspiration visit Pascal Oudet on Facebook https://www.facebook.com/@PascalOudetSculpture/ or his website https://www.lavieenbois.com/welcome/
Wood Dryness: Ensuring the wood is adequately dried to prevent warping or cracking.
Grain Alignment: Assessing the grain direction for optimal aesthetic and structural results.
Hardness Suitability: Choosing wood hardness appropriate for the intended use; softer woods may not hold intricate details well.
Ease of Finishing: Avoid complex designs on softer woods, such as kauri, as they can be challenging to sand and may not retain fine details effectively.
Colour of the Wood: Considering the natural colour and any desired finishes, as this impacts the final appearance of the project. Whitewood like oak is great for Briwax colourfast wax