Club Meeting: 19 Feb 2025
Report by: Kevin De Freitas
David, an experienced woodworker with 12 years of spoon-making expertise, shared his process for crafting wooden spoons and spatulas. Throughout the demonstration, he provided insights into his techniques, tools, and finishing methods.
Development of an Idea
David showcased various samples of his work, discussing how his designs have evolved over time. He emphasized the iterative nature of woodworking, where additional features, such as scraping edges, were added based on functionality and user feedback. Notably, he created a batch of spoons of Martha Stewart style, using native New Zealand wood for export to the USA.
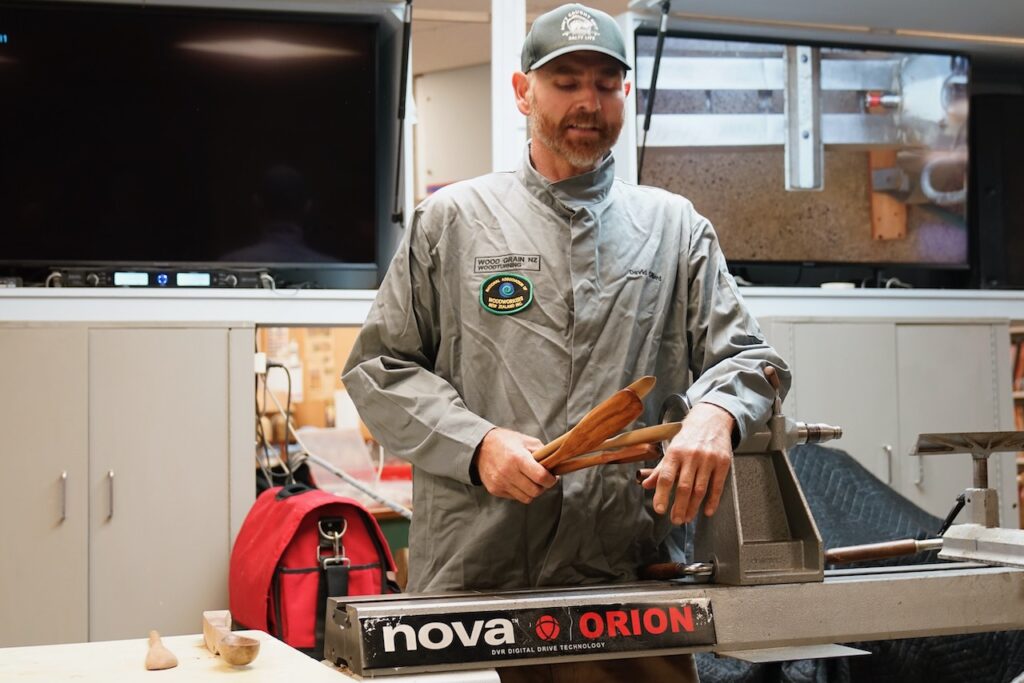
Making a Spatula
Materials and Preparation
- Uses wood scraps approximately 300x100x30mm.
- Layout includes two spoons or spatulas per blank.
- The bandsaw is used to cut away excess wood (referred to as “wings”), which is then repurposed as kindling.
- The spoon or spatula end is mounted at the tailstock end of the lathe for optimal shaping of the handle.
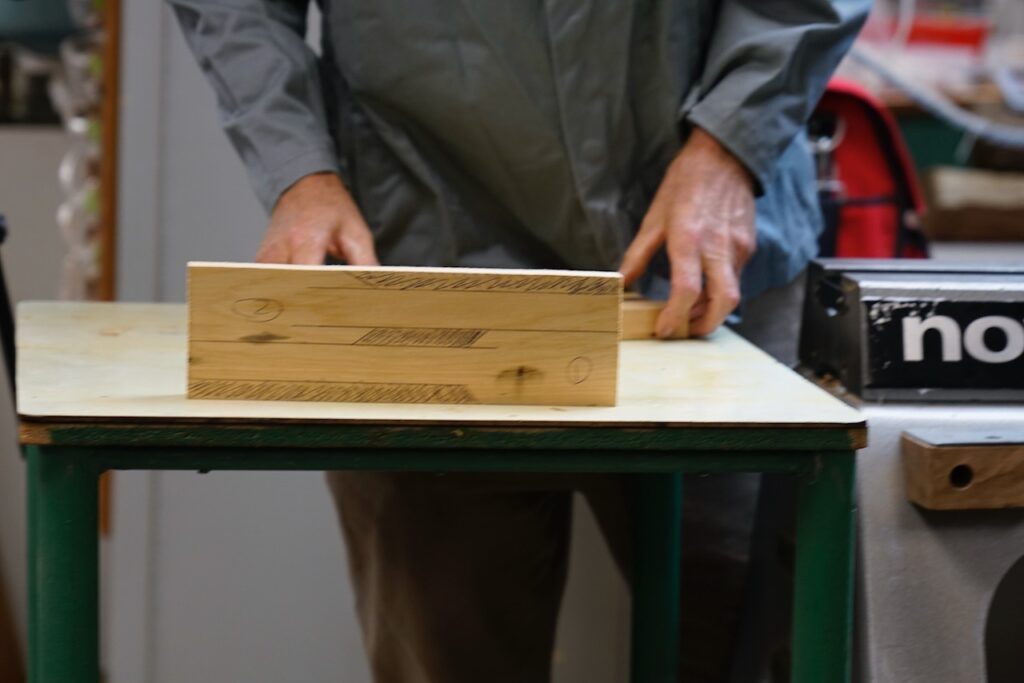
Turning the Handle
- Key considerations: Stability between centers and proper tailstock tension (not too tight) to avoid vibration.
- The lathe runs at 2400 RPM, and a face shield is worn for safety.
- A roughing gouge with swept-back wings is used, allowing it to function as a skew when required.
- The curve is shaped starting from the spoon end toward the headstock.
- The neck is refined while leaving the handle thicker initially to maintain stability.
- For the final cut, the handle is stabilized by hand—often using a paper towel to prevent heat buildup.
- A Detail gouge is used for final shaping of the end of the handle.
- The piece is parted off 1mm beyond the intended end, followed by power sanding to prevent grain breakage.
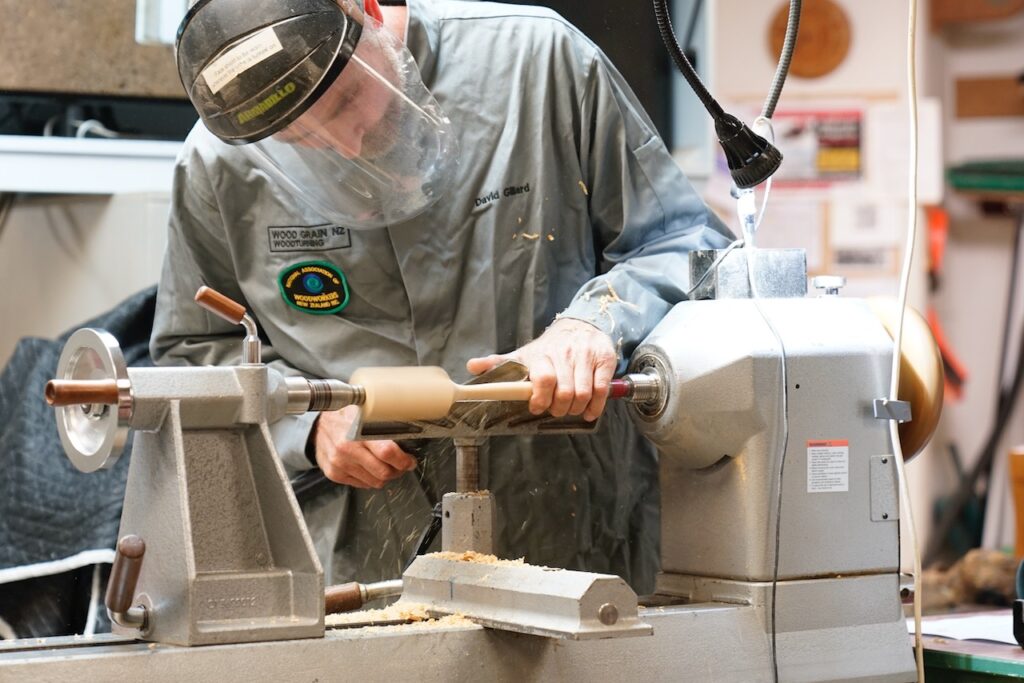
Shaping the Spatula End
- The bandsaw is used to remove excess material from either side.
- The belt sander (80 grit) is applied to smooth the spatula’s surface.
- To avoid linear scratches, the spatula is moved up and down quickly during sanding.
Making a Spoon
David employs a Pantorouter, a pattern-following router jig developed by Matthias Wandel (YouTube creator). The Pantorouter ensures precision, as the template used is double the size of the final spoon, eliminating inconsistencies.
Steps:
Routing the Spoon Bowl
- The router is equipped with a ball-nosed bit.
- Mount the blank and carefully follow the pattern to create the concave spoon profile in the blank
- Can create both right-handed and left-handed spoons (typically at a 40:4 ratio).
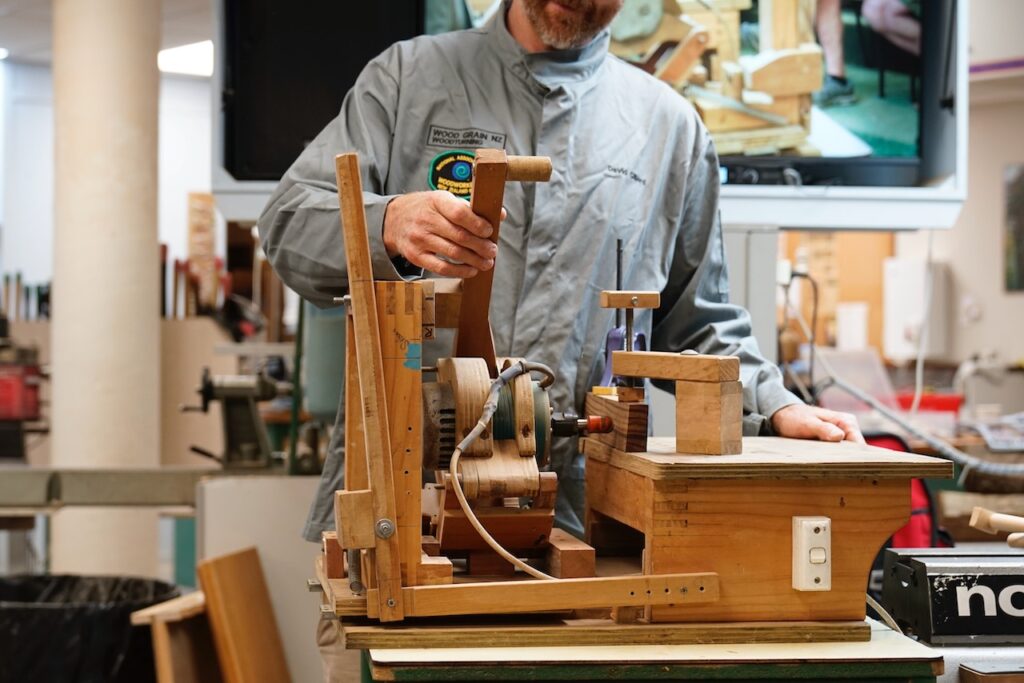
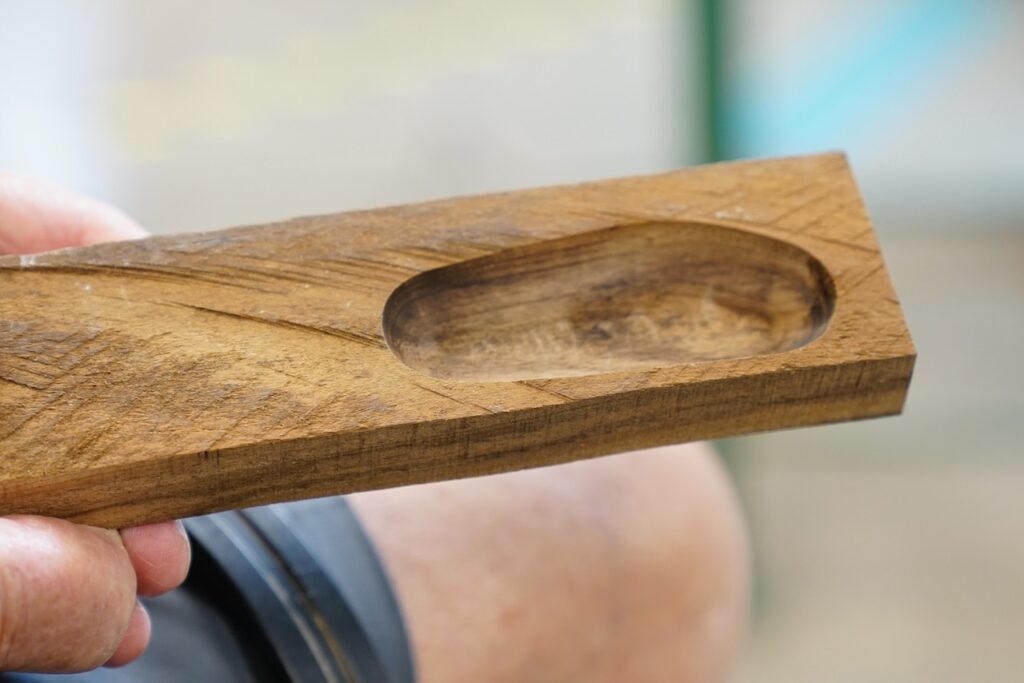
Turning the Handle
- The process follows the same steps as spatula handle shaping.
Finishing the Spoon Bowl
- Cut away excess wood to form the outer shape of the spook
- Superglue is applied to stabilize torn grain before sanding.
- The spoon is carefully sanded for a smooth finish.
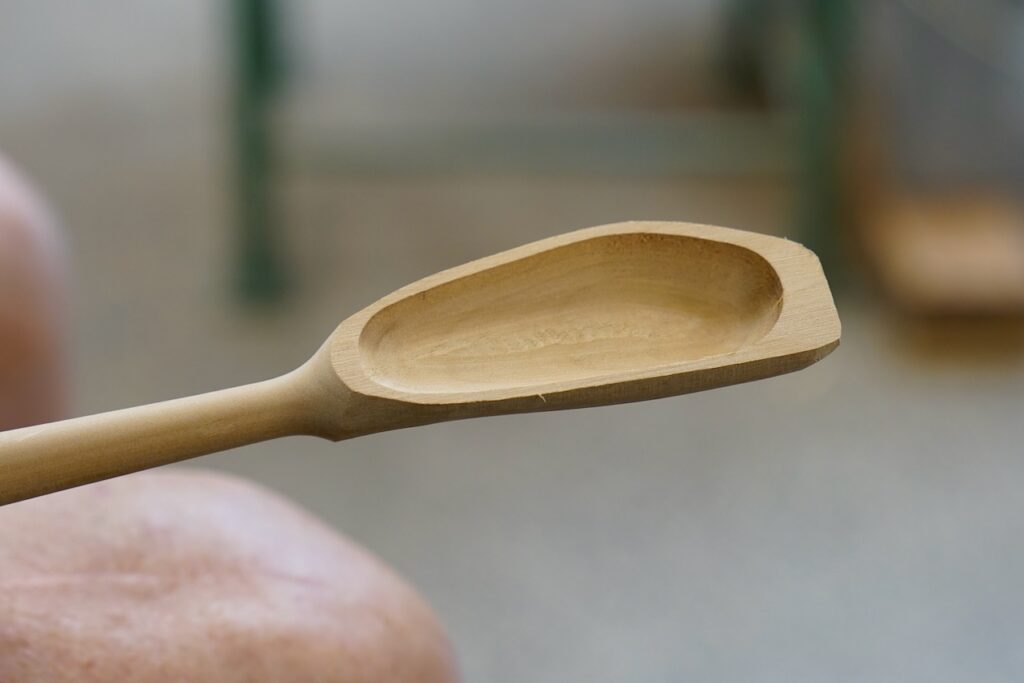
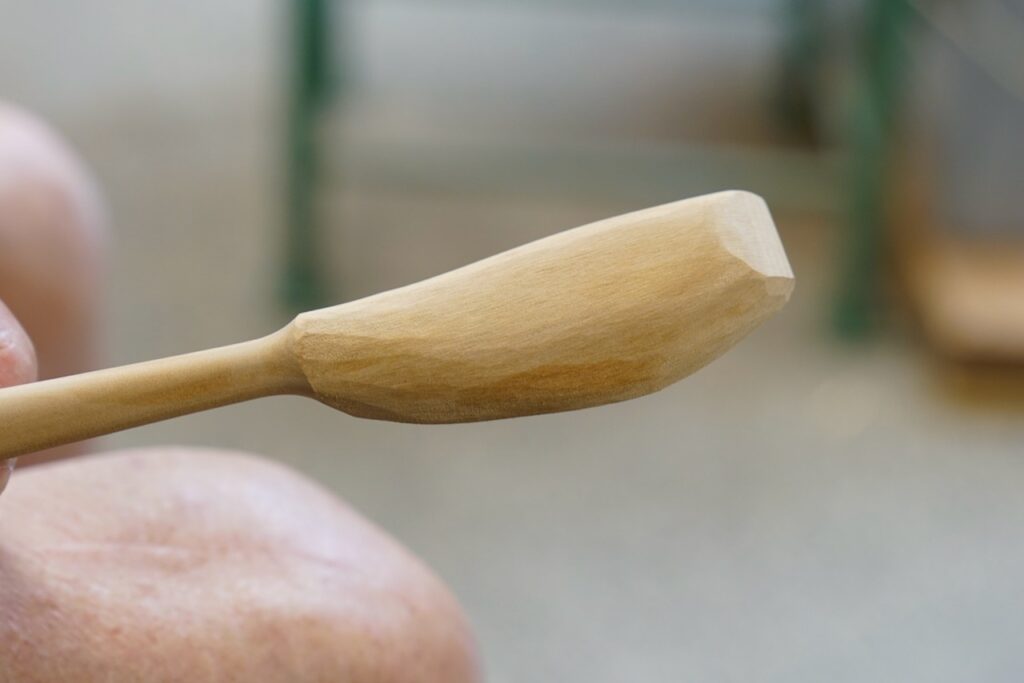
Finishing Process
- After sanding, the spoons and spatulas are treated with Woodgrain Wood Conditioner.
- The pieces are oiled and waxed, with the wax left overnight for better absorption.
Packaging for Sale
David demonstrated how he packages his finished spoons and spatulas in hemp bags, making them ready for sale at markets.
David’s demonstration provided a comprehensive look into the artistry of wooden spoon and spatula making, from raw materials to a finished product ready for sale. His combination of traditional craftsmanship with modern tools like the Pantorouter highlights the balance of precision and hand-finishing required for high-quality wooden kitchenware.