Club Meeting: 8 May 2024
Report by: Ian Connelly
Rocky started the evening by explaining that the origins of epoxy resins were linked to the dental industry. This set the tone for a very informative evening.
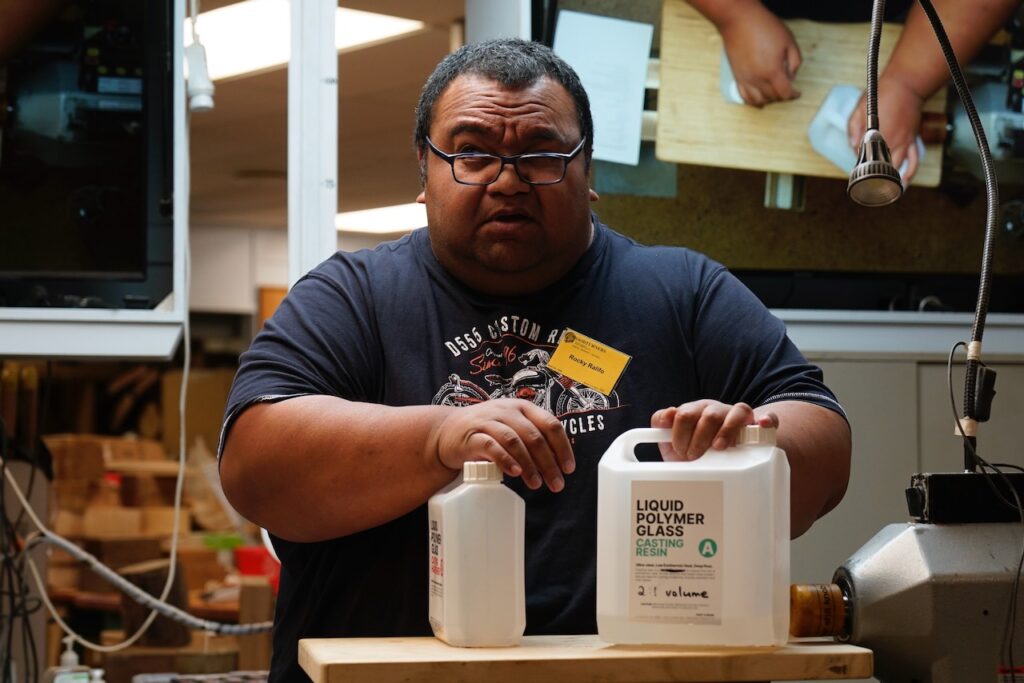
His main source of epoxy was Liquid Polymer Glass deep pour with a ratio of 2:1. He also used their Knot Filler resin for thin flood coats over the wood and resin. Here he highlighted the importance of checking the ratio of the resin you are using, as getting it wrong can have dire effects. He used a measuring cup from aliexpress that had various ratios on the side of the cup as well as indicators for different quanities. This works for resins designed to be mixed by volume, rather than by weight.

He then showed us an example board that took about 2 litres of resin.

Options suggested for colouring resin
- Mica Powder
- Metallic Powder
- Alcohol based inks
- Acrylic paint
- Gel Colourant
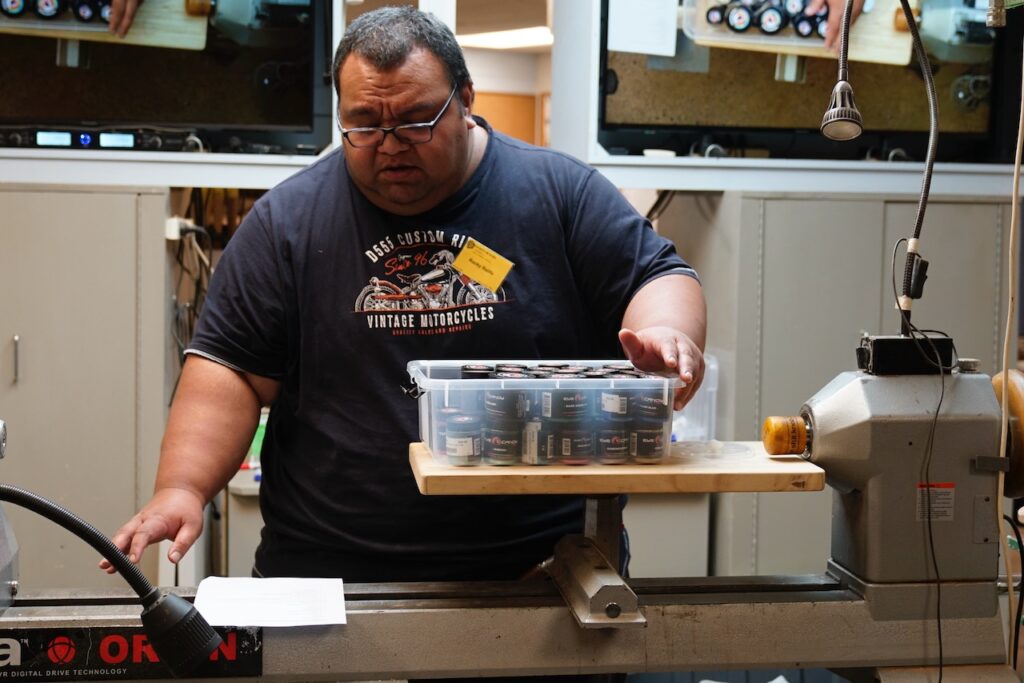
With the slow deep pour resin Rocky had found he could mix the resin, wait an hour for the bubbles to rise, then pop them with a flame. He would then pour a thin stream into the mold to minimise the addition of further air to the mix.
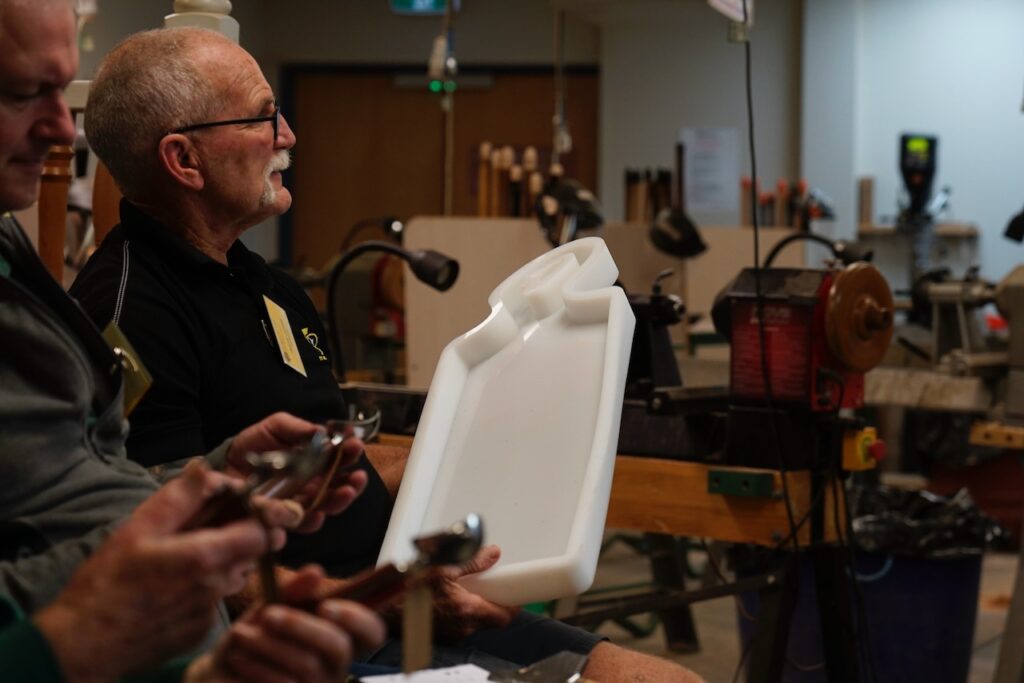

When Rocky start his journey into epoxy resins he made home made molds, but found this too risky as the resin would find the smallest pinhole to escape. He then moved to using commercial molds, silicone molds which the resin releases from quite easily, although the use of a mold release product improves the lifetime of the mold and reduces the likelihood of tearing the silicone. The other molds he has are made from hdpe, and have draft on the side (an angle) that allows them to release with a twist and a tap on the bench.
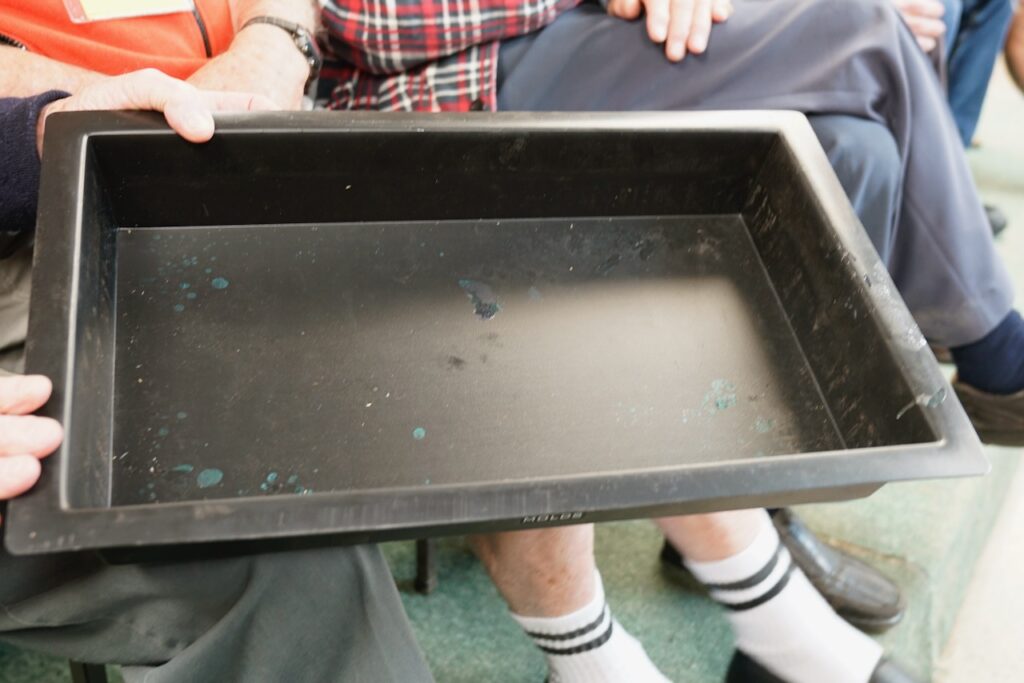
Other topics covered included
- Use of a spirit level to make sure the mold was level before a pour.
- A cardboard box over the item to prevent dust (especially for items that received a flood coat).
- Painters cones to raise the board when flood coating, to it does not stick to the workbench.
- Having some small items to pour was also suggested to minimise waste of resin, Rocky makes handles for ice cream scoops
- Wood should be dry – Rocky suggests 10-12% moisture max before using with resin
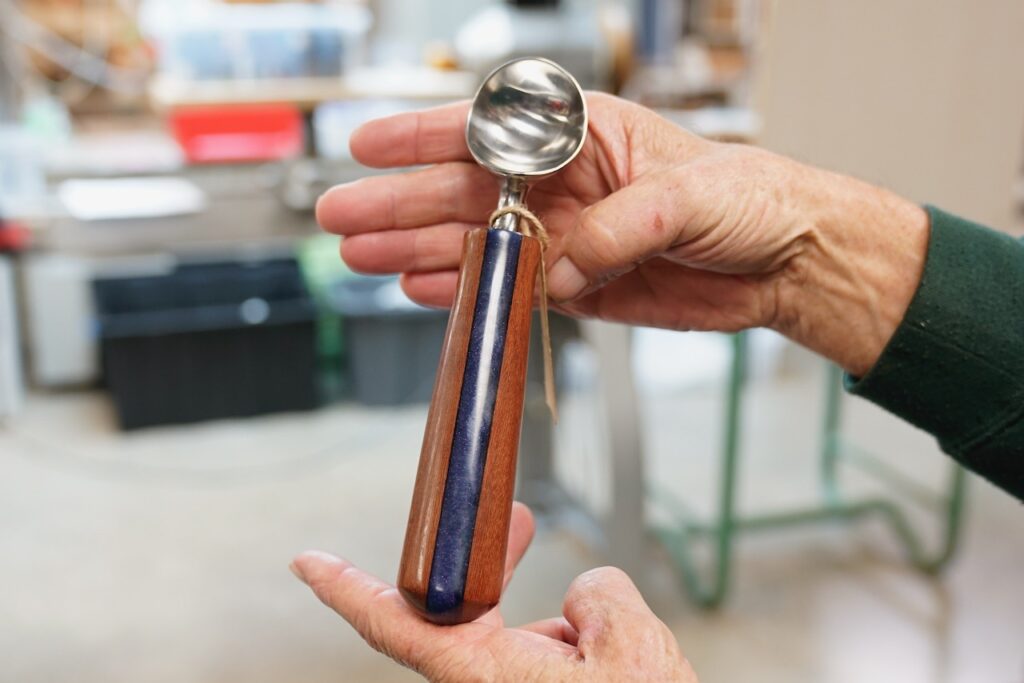
Another thing that was noted is that Rocky left the ice cram scoops for 2 weeks after pouring before he would attempt to turn them.

It was a very informative night, and if somehow people failed to learn something from Rocky then they must have been sleeping.